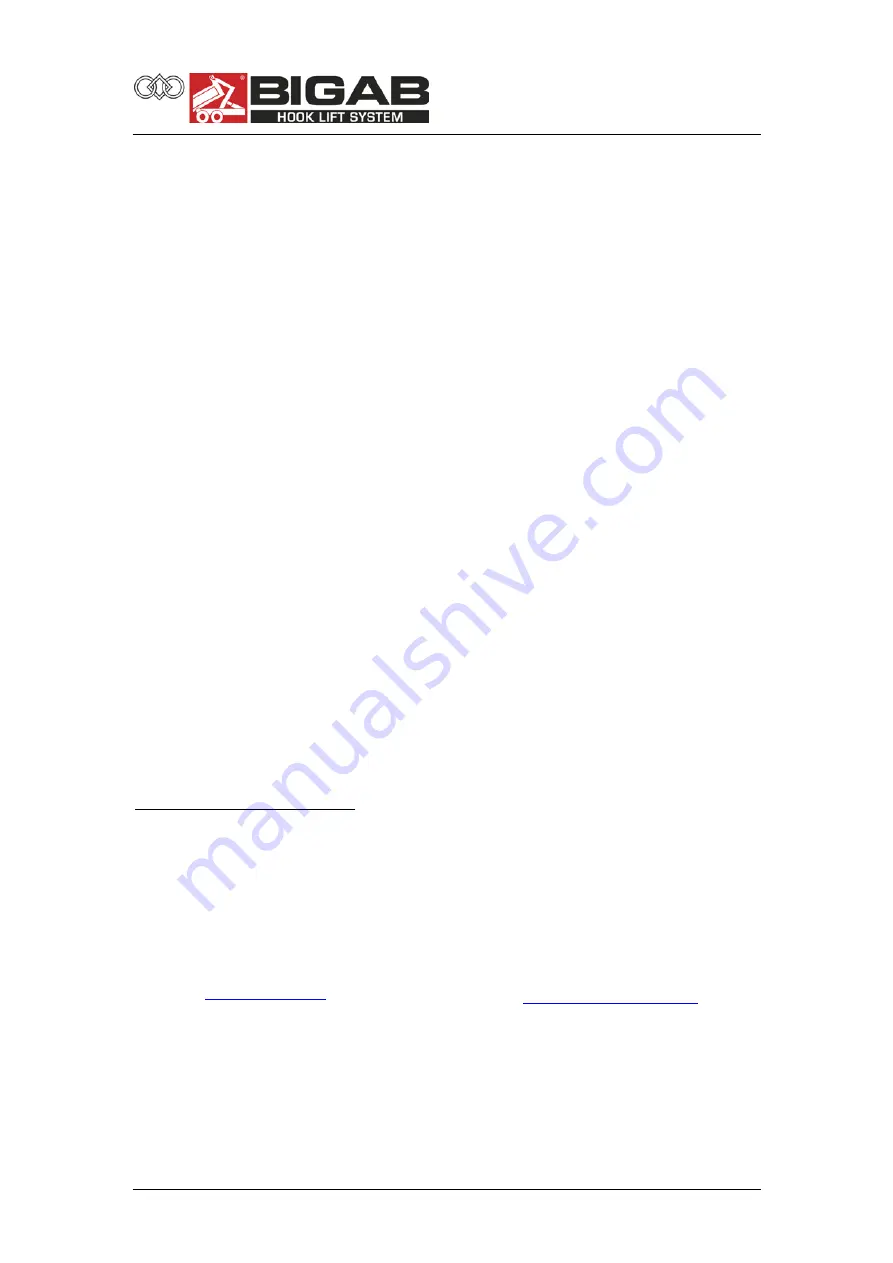
20-24
© 2005 Ver. 1 Fors MW Ltd
www.forsmw.com
1
Table of contents
................................................................................................. 2
................................................................ 3
.......................................................................... 4
......................................................................................... 5
..................................................................................... 13
................................................................................................ 20
.............................................................................................. 20
......................................................................................... 20
WITHDRAWAL FROM USE AND STORAGE
........................................ 20
......................................................................... 21
HANDLING IN ROLL ON – ROLL OFF
.................................................. 21
........................................................................... 23
................................................................ 24
................................................... 25
............................................................................ 26
............................................................................. 28
................................................................................. 30
............................................... 32
................................................. 32
................................................................... 34
.................................................................. 34
.............................................................. 35
............................................................................................ 40
....................................................................................... 51
Factory:
CONTACT INFORMATION:
AS FORS MW
Tule 30
765 05 Saue
Estonia
Tel: + 372 679 00 00
Fax: + 372 679 00 01
E – ma
Aftermarket:
Language spoken is English and Swedish.
FMW Farma Norden AB
Hornsväg 2
605 97 Norrköping
Sweden
Tel: + 46 (0) 165 770
Fax: + 46 (0) 128 370
E – ma