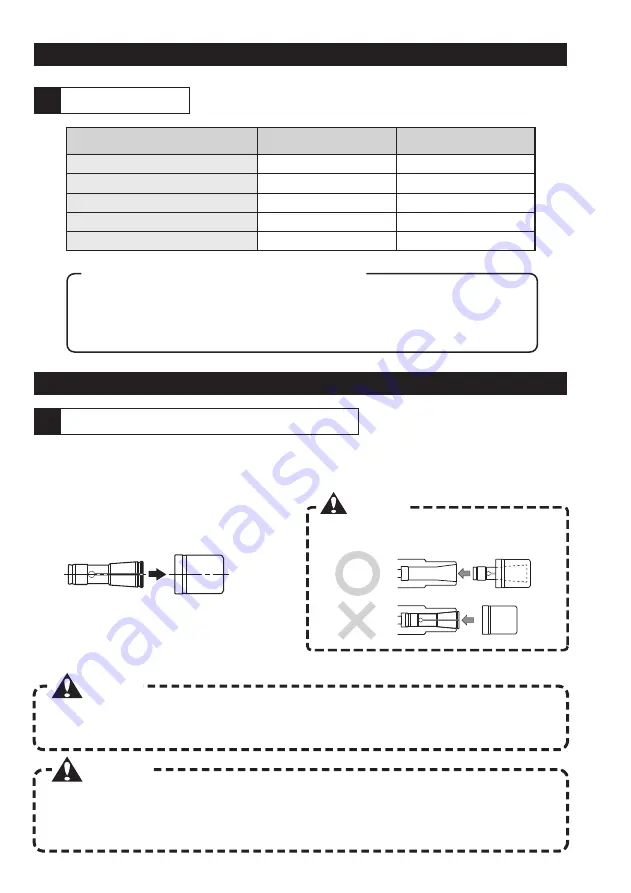
Caution
Before installing a cutting tool, always use, on the internal diameter of the chuck, the internal and
external surfaces of the collet and on the shank of the cutting tool, kerosene or other degreasing
agents and wipe the dirty parts with a cloth.
Warning
The Air Turbine Spindle rotates at very high speed. In case of using cutting tools with a big
unbalance or tools with small diameter and long overhang, due to the centrifugal force, the
cutting tool may break creating an extremely dangerous situation. Use a cutting tool with high
rigidity and make it short as much as possible.
SPECIFICATIONS
UTILIZATION PROCEDURES
Clamping range (mm)
Tool diameter (mm)
Minimum spindle speed (min
-1
)
Maximum spindle speed (min
-1
)
Collet
ø0.45 - 4.05
ø1.5 or smaller
About 40,000 (0.3MPa)
About 50,000 (0.6MPa)
NBC4S-dAA (Option)
ø0.45 - 4.05
ø1.5 or smaller
About 60,000 (0.3MPa)
About 80,000 (0.6MPa)
NBC4S-dAA (Option)
Type
RBX5 / RBX5C
RBX7 / RBX7C
BIG-PLUS is a standard product of BIG Daishowa Seiki. Use machine tools with the
BIG-PLUS trademark to obtain a correct double face contact. BIG-PLUS holders are
also compatible with spindles of standard machines. In this case, check that there
are not projecting objects in the machine spindle’s surface and in the holder’s surface.
How to install / remove a cutting tool
1
Specifications
1
About BIG-PLUS (BBT, BDV, and BCV)
Use the X-Wrench and the Mega Wrench for install/remove the cutting tool. Please consult P4 “How
to use the X-Wrench” regarding how to use the X-Wrench.
Always install the collet in the chuck body
after have inserted it into the nut.
Caution
Insert the collet from the rear part of the nut
and push it until the ribbed part of the collet is
set with a “click”.
It is possible to remove the collet from the nut
by pulling the collet straight along the spindle.
[Collet installation procedures]
[Collet removal procedures]
3