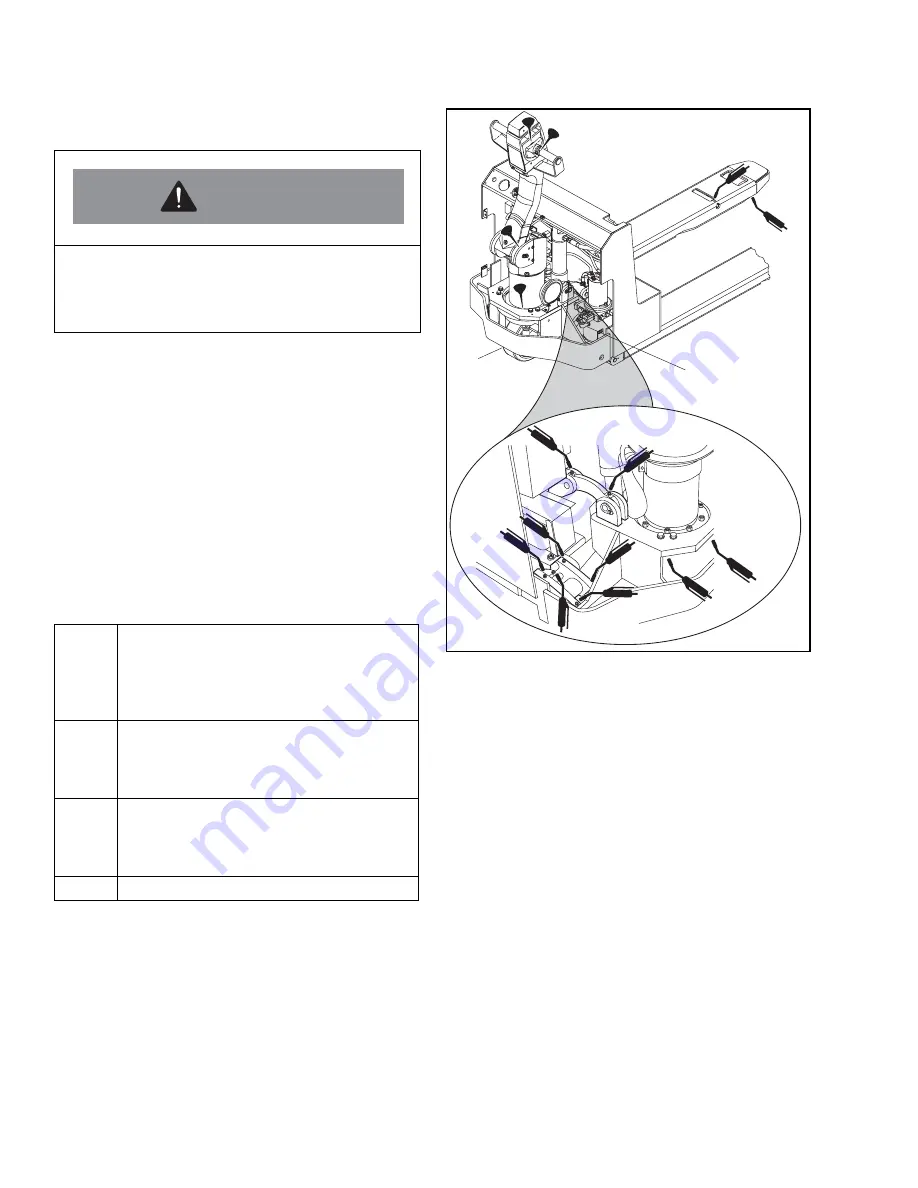
3-4
PPT0104-901336
3.
Charge batteries in accordance with hydrometer
readings.
NOTE:
A fully charged battery has a specific
gravity of 1.260 to 1.275.
4.
After charging, again check water level in each cell
of the flooded cell batteries. Water level must cover
plates but not be higher than the base of the
battery cell filler neck.
3-5. LUBRICATION
Refer to Table 3-3 for recommended types of grease
and oil. Table 3-3, in conjunction with Figure 3-1,
identifies the items requiring periodic lubrication and
where they are located on the lift truck.
Table 3-3. Recommended Lubricants
(See Table 3-4 for Application)
Figure 3-1. Lubrication Locations
•
Do not service batteries while they are being
charged.
•
Do not connect or disconnect battery from
charger while charger is on.
No. 1
Transmission oil - EP SAE 80W-go.
Capacity - 1.5 quart. Big Joe No. 055780
(Replace with 055790. 1W-30, if cold
conditioning option for continuous
operation below 320F is installed).
No. 2
Grease-Lithium base, general purpose. Big
Joe No. 055750 (Replace with 055753 if
cold conditioning option for continuous
operation below 320F is installed).
No. 3
Hydraulic oil. Big Joe No. 900855 (Gallon)
or 900893 (Quart). (Replace with 055784 if
cold conditioning option for continuous
operation below 320F is installed)
No. 4
Engine lubricating oil - No. 20
WARNING
I-7044
Summary of Contents for PPT 45 Series
Page 6: ...vi PPT0104 901336...
Page 12: ...2 4 PPT0104 901336 NOTES...
Page 18: ...3 6 PPT0104 901336 NOTES...
Page 50: ...5 2 PPT0104 901336 NOTES...
Page 66: ...6 16 PPT0104 901336 NOTES...
Page 67: ...PPT0104 901336 7 1 Section 7 PARTS LIST...
Page 82: ...7 16 PPT0104 901336 THIS PAGE INTENTIONALLY LEFT BLANK...
Page 86: ...7 20 PPT0104 901336 THIS PAGE INTENTIONALLY LEFT BLANK...
Page 100: ...7 34 PPT0104 901336 NOTES...
Page 101: ...PPT0104 901336 i...
Page 102: ...PPT0104 901336 ii Big Joe Manufacturing Company Lincolnwood IL 60646 Manual Price 35 00...