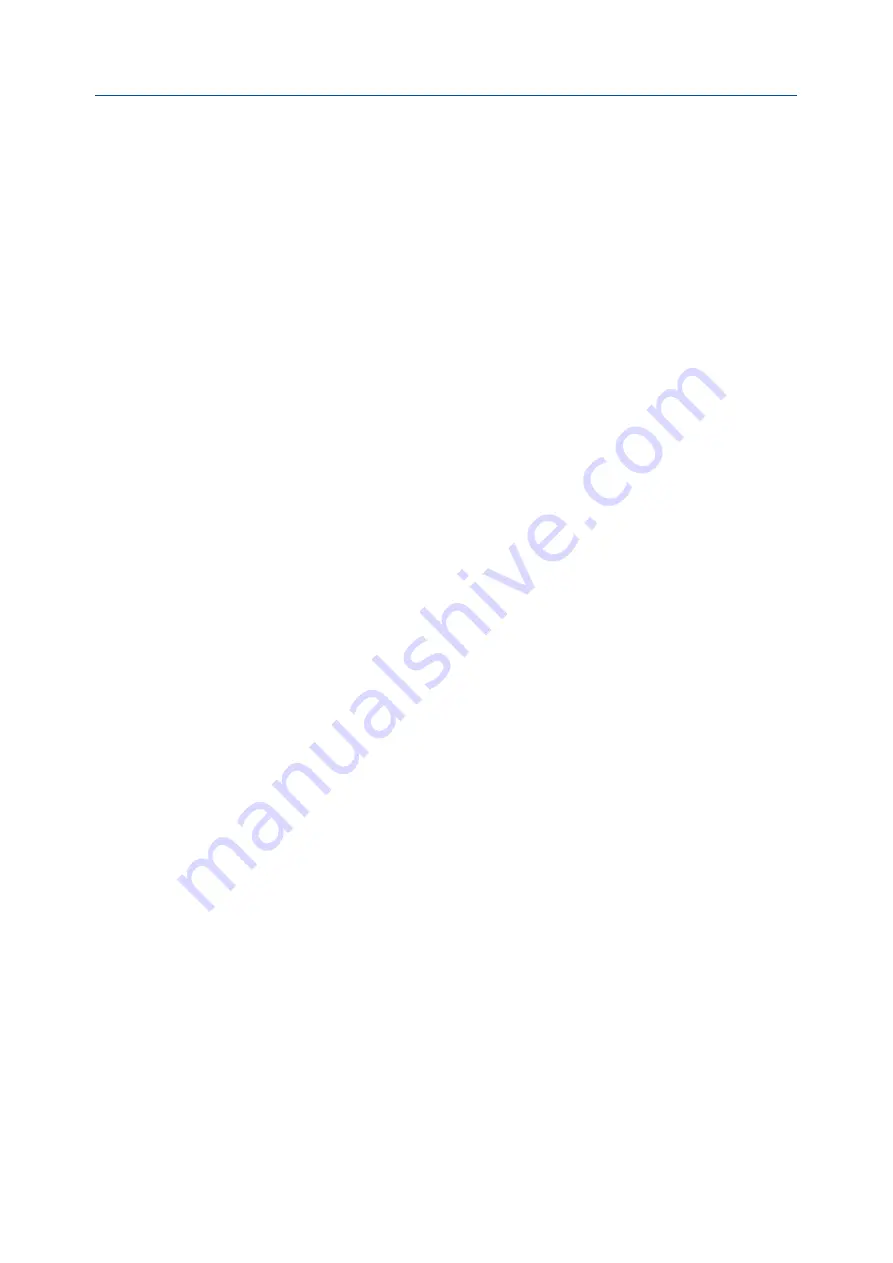
September 2021
Installation, Operation and Maintenance Manual
VCIOM-01249-EN Rev. 0
61
Set-Up Routines
Section 9: Set-Up Routines
Auxiliary relays AS1, 2, 3, 4, 5, 6, 7 and 8
•
Press NO to answer prompt “MONITOR RELAY change?”.
•
Press YES to change AS1, press NO to select the other relays.
•
Press YES if the condition associated to AS1 relay is correct, press NO to scrolls the
list of conditions and press YES to set.
•
Press YES or NO to either confirm or change the type of contact when the
condition occurs (break, make). Since relay AS8 is change-over, this option is
not available.
•
Press NO to pass to AS2 and then repeat the procedure for the other relays.
•
Press NO to exit.
9.1.7 Positioner
The positioning function is only available in inching or modulating F01-2000 actuators and
allows to position the valve according to a “position request R%” command signal.
The positioning function compares the present actuator position % with the position
request R%, and if the difference is greater than the dead band the actuator is driven to
reach the new requested position.
The “position request R%” signal may either be received from the bus or the 4 - 20 mA
analog input. If the F01-2000 is set to receive the position request R% from the bus, a
fieldbus interface card must be present, or a Hardware alarm will be generated. If the
F01-2000 is set to receive the position request R% from the 4 - 20 mA generator, the
Ain/Aout card must be present, or a Hardware alarm will be generated.
The following options can be configured via local operator interface:
•
Dead band: configurable from “position resolution%” to 25.5% of the
maximum position error. The configured value should be great enough to avoid
the hunting effect.
•
Polarity of the 4 - 20 mA position request signal: it allows to reverse the
relationship between the 4 - 20 mA input signal and the “position request R%”,
according to the following diagrams. The option is not available when the
F01-2000 is set to receive the “position request R%” from the bus.
•
Motion inhibit time: it allows to adjust the length of the delay time between two
cycles of the motor. It can be configured from 1 to 255 s and allows to set the
maximum number of start/hour of the electrical motor.
•
% MIN and % MAX, 4 - 20 mA input signal range: it allows to change the
relationship between the input signal and the position request R%. This function
is useful when a single 4 - 20 mA signal is used to control the position of 2 valves
(e.g.: split range applications). The option is not available when the F01-2000 is set
to receive the “position request R%” from the bus.