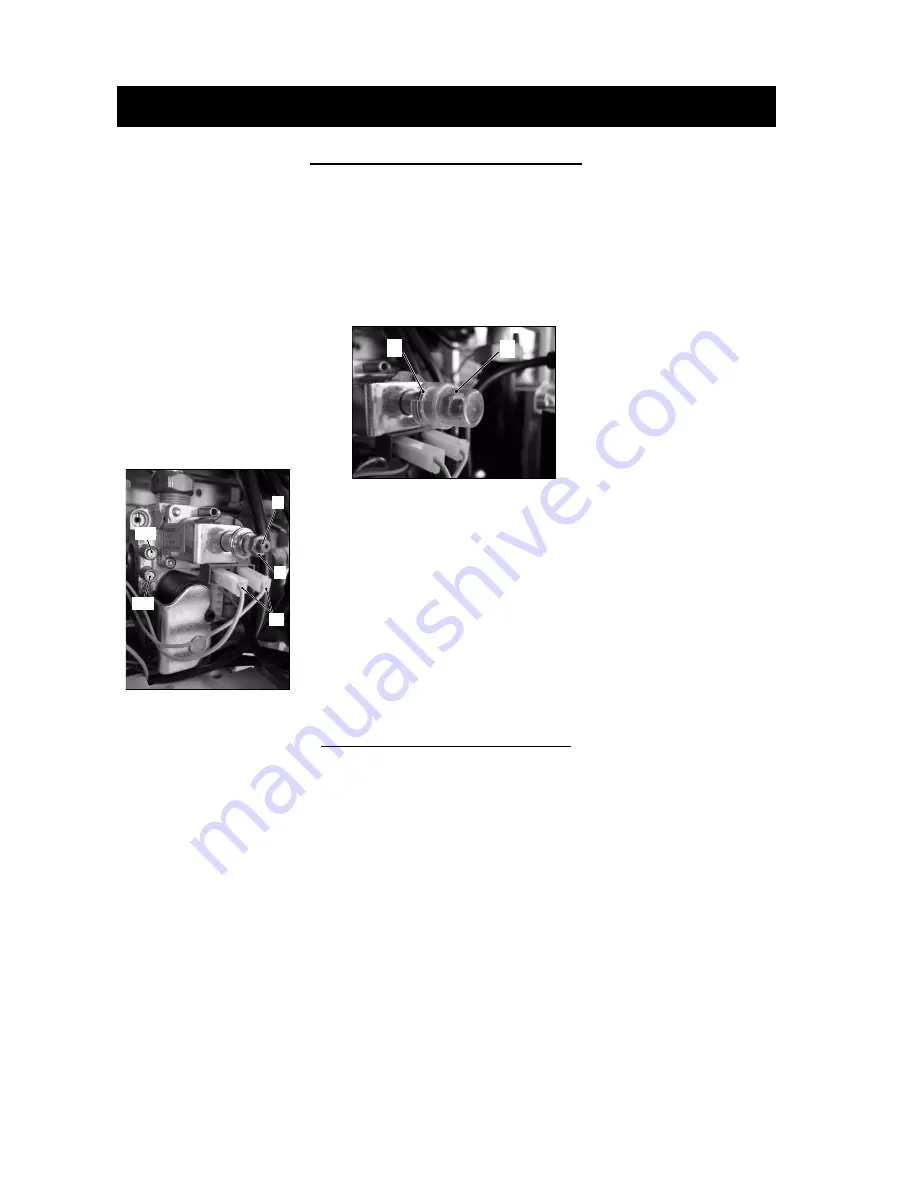
RIVA COMBI MANUAL - REV B
38
15.5 Adjustment of the gas pressure:
•
Remove the front panel
of the case.
•
Open the gas valve inlet
pressure test point (20
in Fig. 15.6) at the valve
input, connect a
suitable pressure gauge
and check the gas
pressure of the supply
network.
•
Remove the gauge and
close the pressure test
point 20.
•
Open the gas valve
outlet pressure test
point (19 in Fig. 15.6)
and connect the gauge.
E
F
G
20
19
Figure 15.6
•
Remove the protection
cap I (Fig. 15.7) from
the mechanical
pressure adjustment
components levering
with a flat screwdriver in
the slots H.
•
Start the boiler at its
maximum power.
H
I
Figure 15.7
•
Operate the boiler in
d.h.w. mode or ensure
that the boiler is not
range rated if the test is
carried out in c.h. mode.
•
Rotate the maximum
gas pressure
adjustment (F in Fig.
15.6) until you obtain
the required pressure
(by rotating clockwise
the pressure increases).
•
Turn the boiler off and
disconnect one of the
two connectors (E in
Fig. 15.6).
•
Start the boiler and
rotate the minimum gas
pressure adjustment (G
in Fig. 15.6) until you
obtain the required
pressure (by rotating
clockwise the pressure
increases).
•
Turn the boiler off and
re-connect the wire to
the modulating
operator.
•
Start the boiler and
check again the
maximum gas pressure
setting.
•
Turn the boiler off and
disconnect the gauge.
Important: after the
checks all of the test
points must be sealed.
15.6 Checking the ignition device:
With the burner on high flame close the gas cock. After three ignition attempts (within about
three minutes), the lock-out signal lamp must appear (D on Figure 15.4). To reset the boiler turn
the knob B (figure 15.4) on the 0 position and then press and release the boiler reset button (C
on Figure 15.4).
15. Commissioning Cont.
Summary of Contents for RIVA COMBI
Page 13: ...RIVA COMBI MANUAL REV B 13 5 1 Sequence of Operation...
Page 51: ......