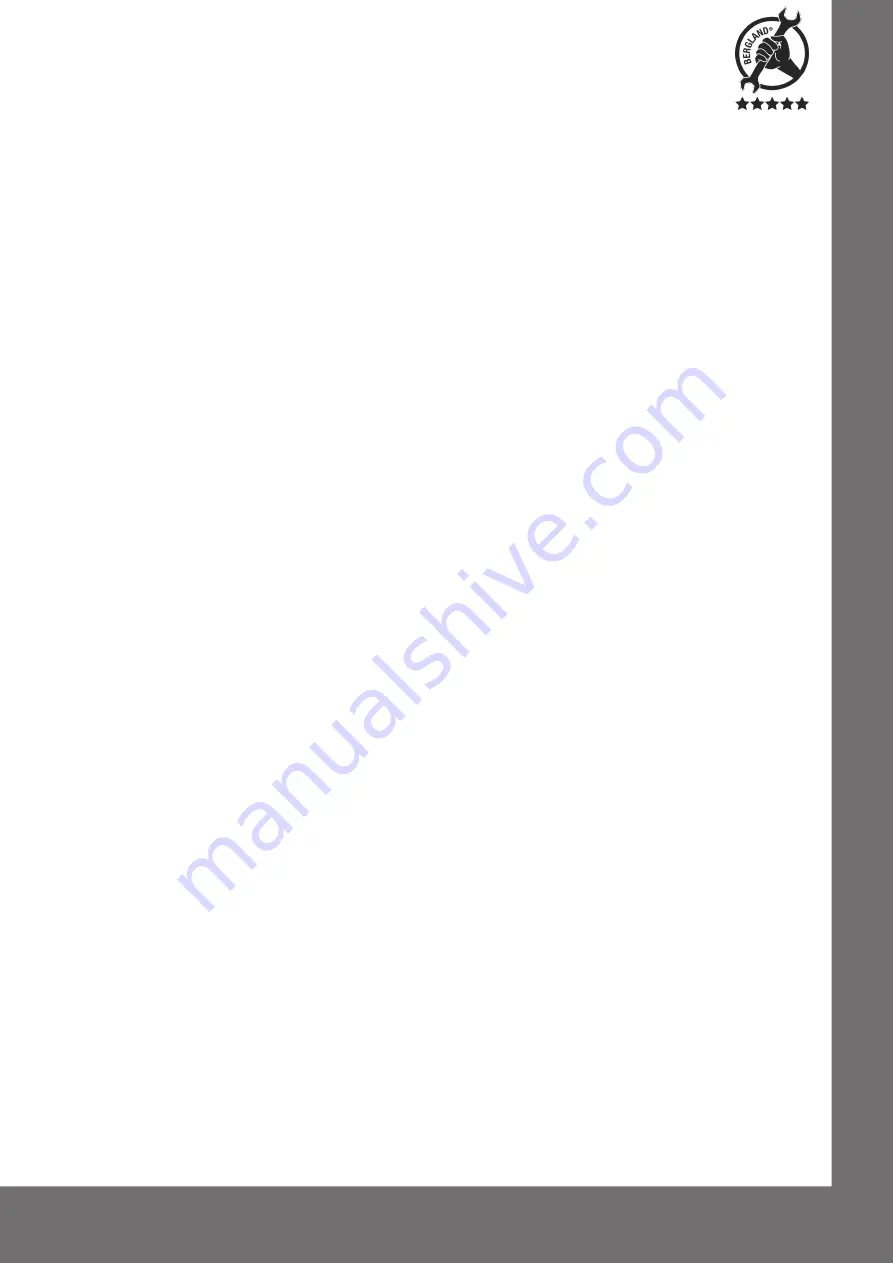
SW-Stahl und Werkzeugvertriebs GmbH
Tel. +49 (0) 2191 / 46438-0
F
5 6
e s s a r t S r e s u k r e v e L
ax +49 (0) 2191 / 46438-40
e d . l h a t s w s
@
o f n i : l i a
M - E
d i e h c s
m
e R 7 9 8 2 4 - D
Instruction Manual
BGS technic KG
Bandwirkerstr. 3
D-42929 Wermelskirchen
Tel.: 02196 720480
Fax.: 02196 7204820
www.bgstechnic.com
Operation
Important Note
: Be sure the Regulator Knob (9) is turned fully counter-clockwise before connecting the
Cylinder Leakage Tester to a pressurized air source. Failure to do so may result in damage to the tool.
Note
: The engine must be at normal operating temperature for accurate testing.
Start the engine and let it warm up to normal operating temperature, then turn it off for testing.
Caution
: Always run an engine in a well ventilated space. Running engines produce Carbon Monoxide, a
colorless, odorless gas which can cause serious personal injury or death if inhaled.
Warning
: Wear protective gloves and ANSI-approved eye protection when working on a hot engine Keep
hands away from the fan and other moving parts, and protect yourself from electrical shock or burns. Be
aware that working on a gasoline engine is inherently dangerous, and suitable precautions must be taken.
1. Before removing the spark plugs, clean the area around the spark plugs using compressed air It is
important to prevent foreign materials from ailing into the cylinders once the spark plugs are removed.
2. Disconnect the coil wire from the coil, and remove all spark plugs. Note the position of the wires so that
the correct wire may be replaced on each plug at the end of the job on engines with two spark plugs
per cylinder remove only one plug per cylinder
3. Remove the oil dipstick, radiator cap, remove the air cleaner and open the throttle all the way.
4. Position the cylinder to be tested at TDC on the compression stroke so all valves are closed.
5. Pull the pressure regulator knob and turn it fully counter-clockwise. Connect the Cylinder Leakage
Tester to a compressed air source. NOTE: Be sure the air compressor's regulator is set from 7 to 100
PSI. Never operate this tester with air pressure set higher than 100 PSI, which can damage this tool.
6. Turn the Regulator Knob (9) clockwise until the Leakage Gauge (6) reads "0" (zero) at the right end of
scale. Lock the regulator knob.
7. Tighten the Adapter Hose (10) by hand into the spark plug hole of the cylinder to be tested.
8. Connect the quick coupler of Adapter Hose (10) to the quick coupler of the Test Hose (4).
9. You can now read the amount of leakage on the Leakage Gauge (6) as a percentage loss.
10. Test the remaining cylinders to determine which cylinders are bad.
11. Use the diagnostic techniques in the next section to determine the cause of the problem.
Diagnostic Techniques
If one or more cylinders are identified as having 15% to 30% greater compression loss than the others,
you can listen for escaping air pressure to diagnose the problem. Air escaping at the following locations
indicates a potential problem.
1. Oil dipstick tube indicates pressure escaping from the cylinder into the oil jacket. This usually indicated
stuck, burned or worn piston rings.
2. Radiator filler opening bubbles or sound indicates pressure escaping into the coolant jacket. This can
indicate cracked cylinder walls or damaged head gasket. In case of a damaged head gasket, often two
or more adjacent cylinders will show the same problem.
3. Adjacent cylinder indicates a damaged head gasket.
4. Tail pipe indicates burned, stuck or worn exhaust valve.
5. Intake manifold indicates stuck, burned or worn intake valve.
Maintenance
Very little maintenance of this tool is required. Keep this tool clean and free from dirt, grease or grit. Store
it in its case when not in use. Periodically check the threads for damage. Release the pressure from the
gauge before storing.