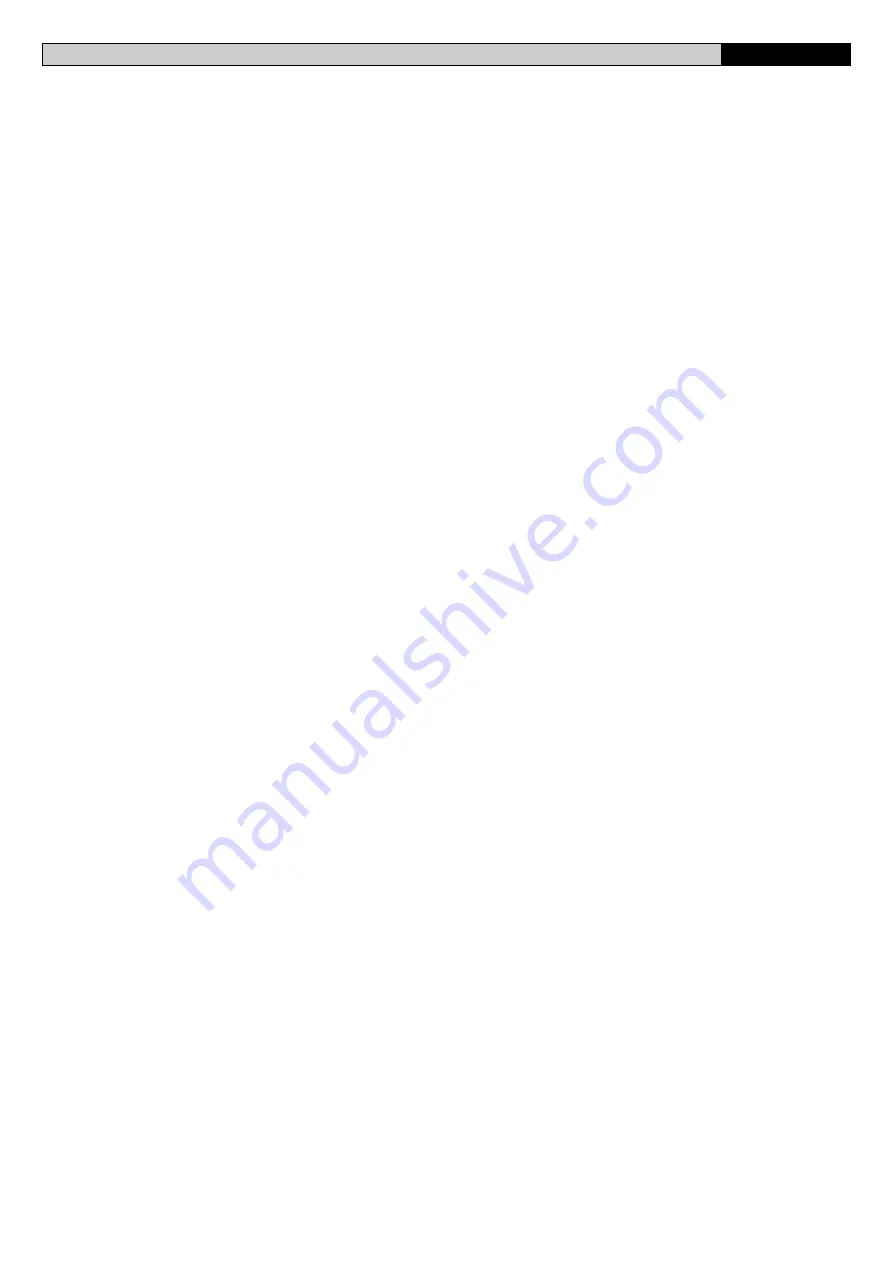
P7 - P4.5 Ver. 02 -
11
D811293_02
INSTALLATION MANUAL
ENGLISH
time, and allows the catch to stay lifted when it reaches the closing position,
without opposing any resistance; the catch will drop into position when the
gate has completed the closing cycle. The electric lock can also be used to
keep the block of the gate in case of actuator malfunction or current failure.
8) ELECTRICAL INSTALLATION SET-UP
Set up the electrical installation as shown in fig.16, making reference to the
current standards for electrical installations. The mains power supply
connections must be kept totally separate from the service connections
(photocells, electric edges, control devices etc.).
Warning!
For connection to the mains, use a multipolar cable having
minimum 3x1.5mm
2
(16AWG) cross section and complying with the
previously mentioned regulations (UL1015).
Connect the control and safety devices in compliance with the previously
mentioned electrical installation standards. Fig.16 shows the number of
connections and the cross section for power supply cables having a length
of approximately 328 ft (100 metres); in case of longer cables, calculate the
cross section for the true automation load. When the auxiliary connections
exceed 164 ft (50-metre) lengths or go through critical disturbance areas,
it is recommended to decouple the control and safety devices by means of
suitable relays.
8.1) The main automation components are
(Fig.16):
I
Type-approved omnipolar circuit breaker with at least 0.118 in (3mm)
contact opening, provided with protection against overloads and short
circuits, suitable for cutting out automation from the mains. Place, if not al
ready installed, a type-approved differential switch with a 0.03A threshold just
before the automation system.
Qr
Control panel and incorporated receiver.
SPL
Preheating board for operation with temperature lower than 5
°
C
(optional).
S
Key selector.
AL
Blinker with tuned antenna and RG58 cable.
M
Actuator.
E
Electric lock.
Fte
Pair of external photocells (emitter section).
Fre
Pair of external photocells (receiver section).
Fti
Pair of internal photocells with CF posts (emitter section).
Fri
Pair of internal photocells with CF posts (receiver section).
T
1-2-4 channel transmitter.
Important:
Before electrically activating the actuator, remove bleed screw
“S” (fig. 17) which is positioned under the articulated joint block and keep
it for any later reuse. Only remove bleed screw “S” when the actuator is
installed. Fit the release cover block provided, as illustrated in the drawing
(fig.18).
“Warning!
For the connection of the accessories, please refer to
the relevant instruction manuals. The type of control boards and accessories
must be suitable for the intended use and in compliance with the current
safety standards”
9) MANUAL OPENING
In case of emergency, for example when the electrical power is discon-
nected, open the electric lock by means of the appropriate key to release
the gate, and open the leaf manually; you may also reach the release knob
to facilitate the manoeuvre. In order to get access to the release knob, move
the small cap in the direction indicated by the arrow (fig.18) to reveal the
lock, insert the key, turn it clockwise by 90
°
and lift the entire release cover
by pulling with the key. The knob must be allowed to turn as far as possible
in the direction indicated by the arrows.
OPEN
to release: the gate can be opened manually with ease.
CLOSE
to lock: turn the knob clockwise until it is completely locked, and
so restore the actuator electrical operation.
10) PUSHING FORCE ADJUSTMENT
For safety reasons, proceed as follows in order to get access to the
adjustment valves:
•
Move the release cover block cap in the direction indicated by the arrow
(fig.19) to reveal the lock.
•
Insert the key, turn it clockwise by 90
°
and lift the entire block by pulling
with the key. Unscrew the two fixing screws and remove the entire
release system.
•
The pushing force is adjusted by two valves marked with the writing
“
Close
” and “
Open
” respectively, which are used to adjust the closing
and opening pushing force (fig.19).
Turn the valves towards the “+” sign to increase the force transmitted;
turn the valves towards the “-” sign to reduce the force. To achieve
proper antisquash safety, the pushing force must be slightly higher than
that needed to move the leaf during both closing and opening
manoeuvres; the strength, which is measured on the leaf edge, must
never exceed the limits set out by the current national standards.
Under
no circumstances whatsoever must the by-pass valves be fully
closed.
Complete the adjustments and restore the release system,
taking care to refit the packing rings and washers. The actuator is not
provided with electrical limit switches. Therefore the motors switch off at
the end of the operation time set by the control unit. The said operation
time must last approximately 2-3 seconds after the moment when the
leaves meet the ground stop plates.
11) COVERING ELEMENT POSITIONING
Covering element “C” for all models can become left or right-handed by
reversing the position of cap “T” (fig.22), taking care to keep the water
drainage channel always at the bottom.
12) AUTOMATION CHECK
Before the automation device finally becomes operational, scrupulously
check the following conditions:
•
Check that all components are tightly fixed.
•
Check that all control devices (photocells, pneumatic edge etc) operate
correctly.
•
Check the emergency manoeuvre command.
•
Check the opening and closing operations using the control devices
provided.
•
Check the normal (or personalised) function control logic in the control unit.
13) AUTOMATION OPERATION
Since the automation system can be remotely controlled by means of a
radio control device or a Start button, all safety devices must be frequently
checked in order to ensure their perfect efficiency. In the event of any
irregular operation, request immediate assistance from qualified personnel.
Children must be kept at a safe distance from the automation
operation area.
14) CONTROL
Various types of control are provided (manual, radio control, magnetic card
access control etc.) depending on the installation requirements and
characteristics. (See the specific instructions for the various control systems).
The installer undertakes to instruct the user about the correct
automation operation, and also point out the operations required in
case of emergency.
15) MAINTENANCE
Before carrying out any maintenance to the controller, disconnect the
system power supply. Periodically check the system for oil leaks.
Topping up should be carried out as follows:
a)
Remove the release system (see fig.19).
b)
Keeping the gate closed, top up using the prescribed oil until its level
reaches above the piston pipe (fig.20 ref. ”P”). To check this, insert a
screwdriver through the release cover block fixing hole, so as to reach
the piston pipe and make sure it is oiled.
c)
Refit all the component paying attention to the seals. Check all automation
safety devices.
When any operational malfunction if found, and not resolved, disconnect
the system power supply and request the assistance of a qualified
technician (installer).
If the power supply cable is damaged, it must be replaced directly by
our company or our technical service department or by a technician
having similar qualification so as to avoid any risks.
When automation
is out of order, activate the manual release knob to allow the manual opening
and closing operations to be carried out by means of the electric lock.
16) MALFUNCTIONS AND REMEDIES
16.1) Faulty operation of the actuator
Using an appropriate instrument, check that the ends of the actuator are
supplied with voltage after the opening or closing command is given. If the
motor vibrates but does not turn, the causes could be as follows:
•
Wrong connection of common wire C (always light blue).
•
No connection between the drive capacitor and the two drive terminals.
•
If the leaf movement is opposite to what it should be, reverse the motor
drive connections in the control unit.
Leaf stops: when the operation time is insufficient, the leaves may not
complete their strokes. In that case, slightly increase the operation time
setting in the control unit.
16.2) Faulty operation of the electrical accessories
All faulty control and safety devices can cause abnormal operation or
automation block. If the control unit is provided with a self-diagnosing
system, identify the fault. In case of malfunction, it is advisable to disconnect
Summary of Contents for P7 - P 4.5
Page 2: ...2 P7 P4 5 Ver 02 D811293_02...
Page 15: ...P7 P4 5 Ver 02 15 D811293_02 Fig 11 Fig 12 Fig 10 Fig 9 P L Z a b c a b c PF F F F T PF F 7...
Page 17: ...P7 P4 5 Ver 02 17 D811293_02 Fig 19 Fig 18 Fig 17 O P E N C L O S E CLOSE OPEN a c b S...
Page 18: ...18 P7 P4 5 Ver 02 D811293_02 Fig 22 C T Fig 21 Fig 20 P...
Page 19: ...P7 P4 5 Ver 02 19 D811293_02...