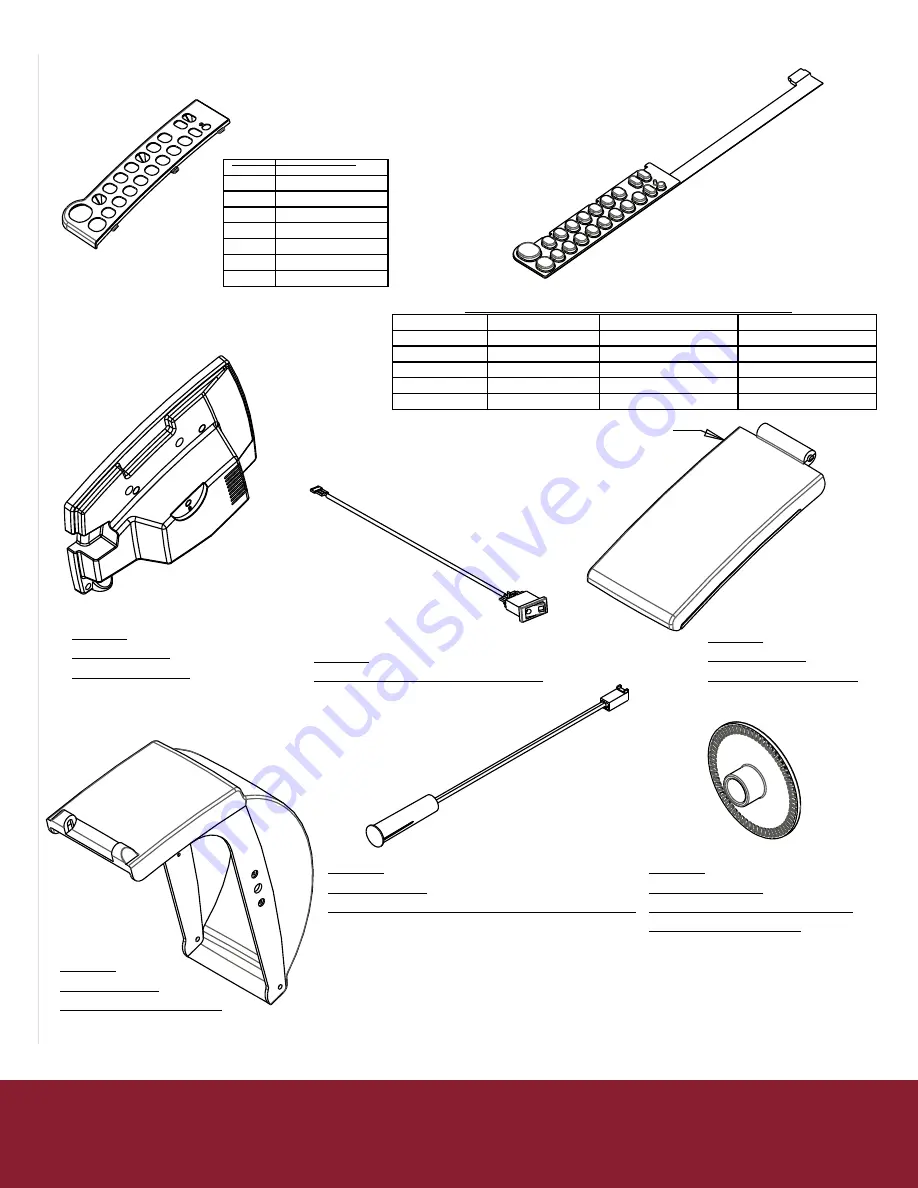
38
Rev 9 2022
R
Better Packages,Inc.
Shelton, CT 06484
MODEL PART NUMBER
ES
E555-039-01
ESA
E555-039-02
EL
E555-039-03
ELA
E555-039-04
EMA
E555-039-06
EJA
E555-039-08
EFA
E555-039-10
MODEL
PART NUMBER
PAD ONLY P/N
SWITCH ONLY P/N
ES
E555-003-01
E555-003-01-PAD
E555-003-01-SW
ESA / EFA
E555-003-02
E555-003-02-PAD
E555-003-01-SW
EL
E555-003-03
E555-003-03-PAD
E555-003-01-SW
ELA
E555-003-04
E555-003-04-PAD
E555-003-01-SW
EMA / EJA
E555-003-06
E555-003-06-PAD
E555-003-01-SW
BP555e ITEM LIST
REVISED 11/04/2011
NOTE:
METAL ENCODER DISK IS NO LONGER AVAILABLE
REPLACE METAL ENCODER DISK WITH PLASTIC ENCODER DISK.
CONVERTING TO PLASTIC DISK REQUIRES A COMPATIABLE
FEED WHEEL ASSY (ITEM 47 - P/N E555-024-01 ) WHICH MUST
BE ORDERED SEPARATELY
ITEM 3
E555-031-00
RIGHT COVER
ITEM 1 - BEZEL
ITEM 2 - MEMBRANE SWITCH PAD ASSY
ITEM 4
E555-071-01 - SWITCH ASSY
ITEM 5
E555-035-01
TOP COVER ASSY
ST-2344
MAGNET
ITEM 7
E555-075-01
MAGNETIC PROXIMITY SWITCH ASSY
ITEM 8
E555-150-00 -
PLASTIC ENCODER DISK
SEE NOTE BELOW
ITEM 6
E555-034-01
REAR COVER ASSY
E555-270-01
BLACK MAGNETIC PROXIMITY SWITCH ASSY
Summary of Contents for 555e
Page 2: ......
Page 36: ...36 Rev 9 2022 Parts Listing ...
Page 46: ...Model BP555e Tape Dispenser ...