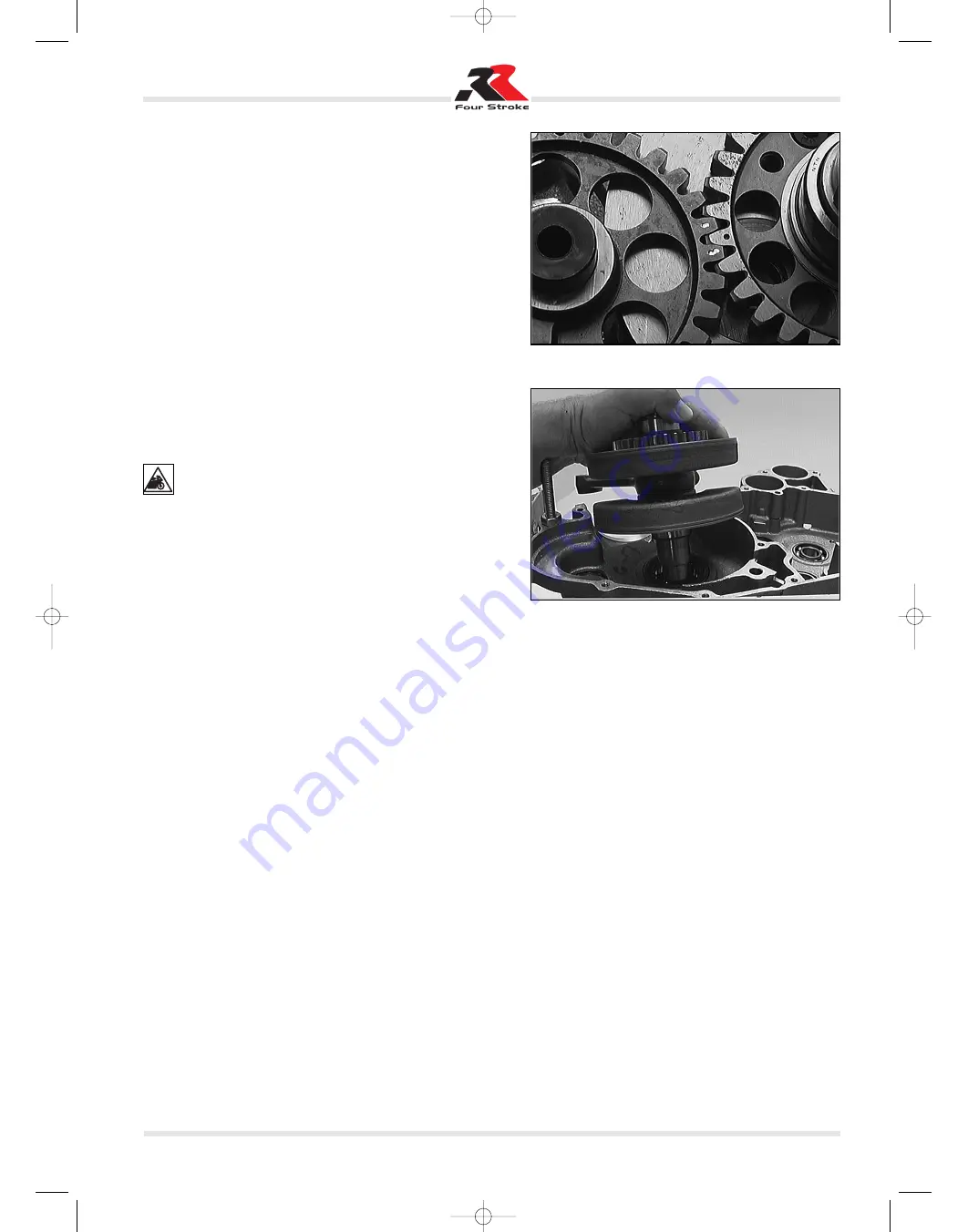
25
6 - Engine
Release 01 Date 09/2007
Removing the countershaft and the crankshaft
– Turn the crankshaft until the marks on the countershaft and
the crankshaft are aligned.
– In this position the crankshaft can be removed from its seat.
– Remove the crankshaft.
– Clean all the parts, check them for wear and replace as nec-
essary.
NOTE:
When the engine is overhauled, it is advisable to
replace all gaskets, oil seals, O-rings and bearings.
64_Inghilterra_059311 27-12-2007 18:22 Pagina 25
Summary of Contents for RR 4T - 250
Page 1: ...WORKSHOP MANUAL 01_Inghilterra_059311 27 12 2007 17 52 Pagina 1 ...
Page 2: ...01_Inghilterra_059311 27 12 2007 17 52 Pagina 2 ...
Page 5: ...Pag 5 GENERAL INFORMATION 1 01_Inghilterra_059311 27 12 2007 17 52 Pagina 5 ...
Page 14: ...14 Workshop manual RR 4T 400 450 525 01_Inghilterra_059311 27 12 2007 17 52 Pagina 14 ...
Page 15: ...SPECIAL TOOLS 2 02_Inghilterra_059311 27 12 2007 17 57 Pagina 1 ...
Page 20: ...6 Workshop manual RR 4T 400 450 525 02_Inghilterra_059311 27 12 2007 17 57 Pagina 6 ...
Page 30: ...10 Workshop manual RR 4T 400 450 525 03_Inghilterra_059311 27 12 2007 18 00 Pagina 10 ...
Page 31: ...MAINTENANCE 4 04_Inghilterra_059311 27 12 2007 18 10 Pagina 1 ...
Page 58: ...28 Workshop manual RR 4T 400 450 525 04_Inghilterra_059311 27 12 2007 18 10 Pagina 28 ...
Page 59: ...BODYWORK AND FITTINGS 5 05_Inghilterra_059311 27 12 2007 18 14 Pagina 1 ...
Page 66: ...2 Workshop manual RR 4T 400 450 525 63_Inghilterra_059311 27 12 2007 18 17 Pagina 2 ...
Page 90: ...26 Workshop manual RR 4T 400 450 525 64_Inghilterra_059311 27 12 2007 18 22 Pagina 26 ...
Page 117: ...ENGINE SECTION REASSEMBLING THE ENGINE 6 66_Inghilterra_059311 27 12 2007 18 32 Pagina 53 ...
Page 137: ...CARBURETTOR 7 07_Inghilterra_059311 27 12 2007 18 44 Pagina 1 ...
Page 150: ...14 Workshop manual RR 4T 400 450 525 07_Inghilterra_059311 27 12 2007 18 44 Pagina 14 ...
Page 151: ...Pag 1 FRONT SUSPENSION WHEEL 8 08_Inghilterra_059311 27 12 2007 18 49 Pagina 1 ...
Page 168: ...18 Workshop manual RR 4T 400 450 525 08_Inghilterra_059311 27 12 2007 18 49 Pagina 18 ...
Page 169: ...Pag 1 REAR SUSPENSION WHEEL 9 09_Inghilterra_059311 27 12 2007 18 53 Pagina 1 ...
Page 174: ...6 Workshop manual RR 4T 400 450 525 09_Inghilterra_059311 27 12 2007 18 53 Pagina 6 ...
Page 175: ...Pag 1 BRAKING SYSTEM 10 10_Inghilterra_059311 27 12 2007 18 56 Pagina 1 ...
Page 182: ...8 Workshop manual RR 4T 400 450 525 10_Inghilterra_059311 27 12 2007 18 56 Pagina 8 ...
Page 183: ...Pag 1 ELECTRICAL SYSTEM 11 11_Inghilterra_059311 27 12 2007 18 59 Pagina 1 ...
Page 186: ...4 Workshop manual RR 4T 400 450 525 11_Inghilterra_059311 27 12 2007 18 59 Pagina 4 ...
Page 188: ...6 Workshop manual RR 4T 400 450 525 11_Inghilterra_059311 27 12 2007 18 59 Pagina 6 ...