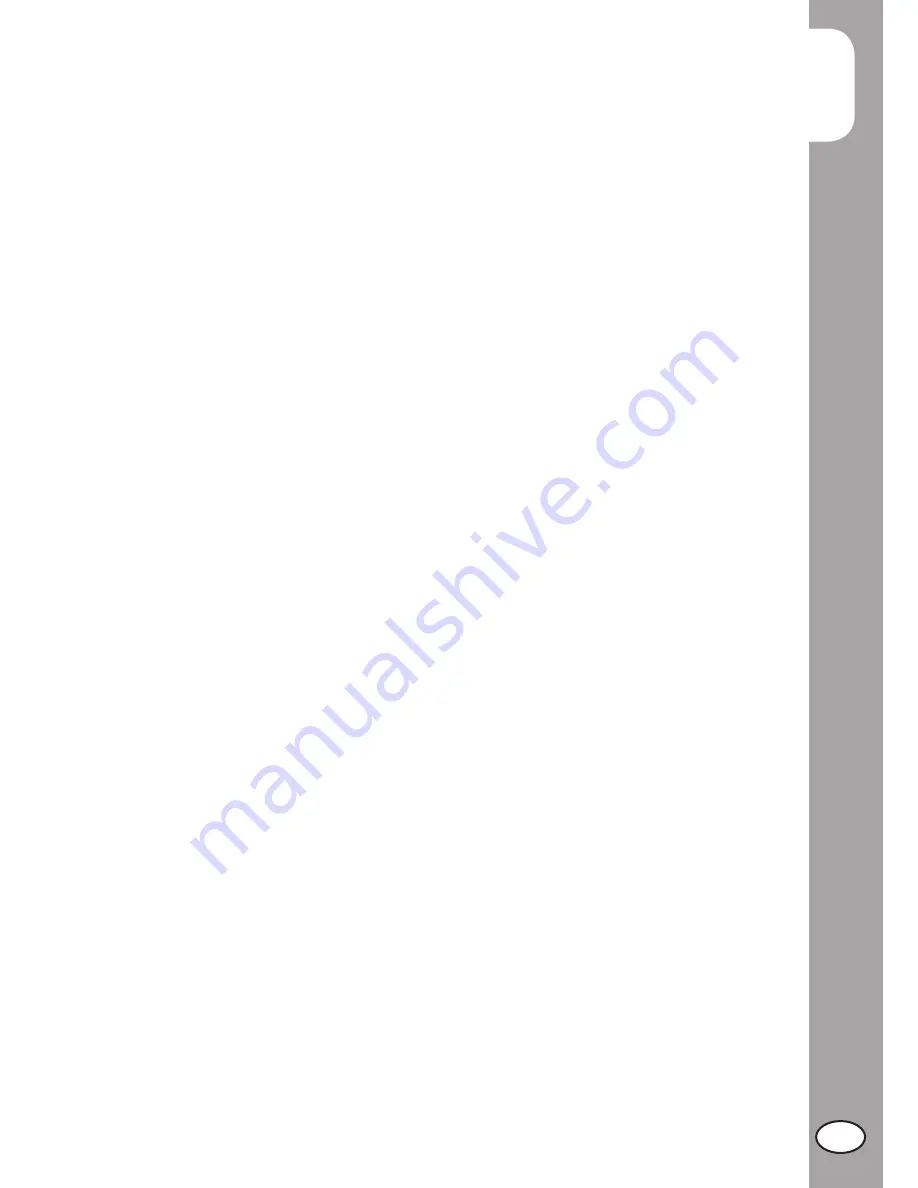
3
ADJUSTMENTS
31
GB
CHAPTER 3 ADJUSTMENTS
CONTENTS
Key to symbols..................................................................................... 32
Brakes ................................................................................................ 32
Front brake ..................................................................................... 32
Rear brake ..................................................................................... 32
Clutch ................................................................................................. 32
Adjustment of gas clearance .................................................................. 33
Idle adjustment .................................................................................... 33
Handlebar adjustment .......................................................................... 33
U-bolt position adjustment ................................................................. 33
Adjustment of the handlebar position ................................................. 34
Adjusting fork ...................................................................................... 35
Adjusting the rebound damper .......................................................... 35
Adjusting the compression damper .................................................... 35
Shock absorber.................................................................................... 35
Adjusting the rebound damper .......................................................... 35
Adjusting the hydraulic compression damper (high and low speeds) ...... 36
Adjusting the spring preload ............................................................. 36
Static sag load test .......................................................................... 37
Suspensions settings according to the weight of the rider ...................... 38