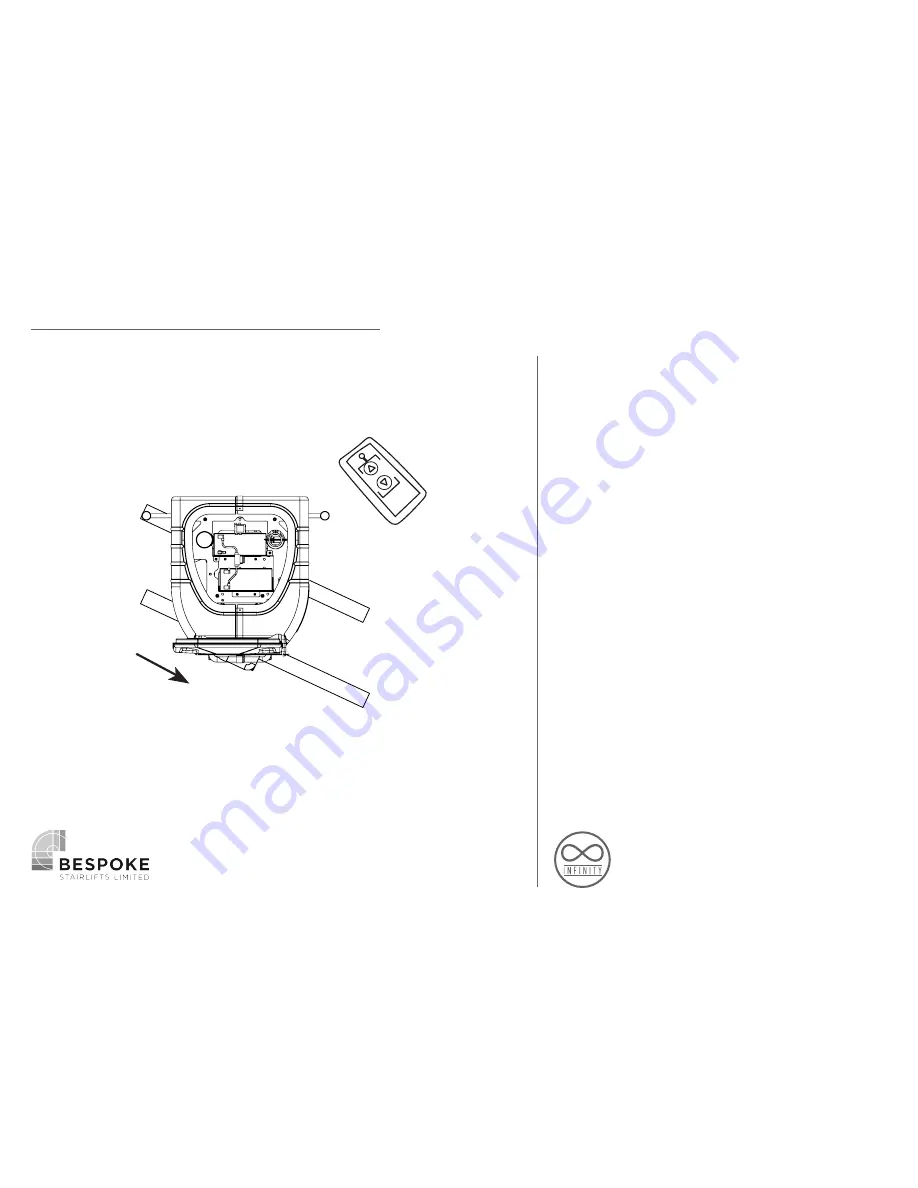
28
MOVE THE CARRIAGE DOWN THE RAIL
Using the temporary remote move the
carriage down the rail to a position that
is accessible. This will enable the seat
and armrest component to be easily
assembled.
Switch off the carriage by the main switch
and disconnect the temporary remote.
The seat and armrest components are
ready to be assembled.
CARRIAGE ASSEMBLY
(Fig 1)
Summary of Contents for Infinity
Page 1: ...1 INSTALLATION MANUAL Infinity Stairlift Rail Carriage Seat Huddersfield England ...
Page 10: ...10 CARRIAGE PREPARATION ...
Page 15: ...15 C OFF INSTALLATION OF THE POWERED SWIVEL UNIT Powered Swivel Board Powered Swivel Unit ...
Page 16: ...16 INSTALLATION OF THE POWERED SWIVEL UNIT ...
Page 17: ...17 INSTALLATION OF THE POWERED SWIVEL UNIT 2a 2b 3 1 1 2 4 3 RH 1 2 4 3 LH ON ...
Page 18: ...18 INSTALLATION OF THE MANUAL SWIVEL LEVER In the Box ...
Page 19: ...19 INSTALLATION OF THE MANUAL SWIVEL LEVER 1 2 ...
Page 20: ...20 INSTALLATION OF THE MANUAL SWIVEL LEVER 3 ...
Page 21: ...21 M8 x8 M5 x4 Manual Swivel Unit INSTALLATION OF THE MANUAL SWIVEL UNIT ...
Page 22: ...22 C OFF INSTALLATION OF THE MANUAL SWIVEL UNIT ...
Page 24: ...24 INSTALLATION OF THE MANUAL SWIVEL UNIT 2a 2b 3 1 1 2 4 3 1 2 4 3 RH LH ON ...
Page 36: ...36 TROUBLESHOOTING ...
Page 44: ...44 Infinity Stairlift Rail Carriage Seat Huddersfield England ...