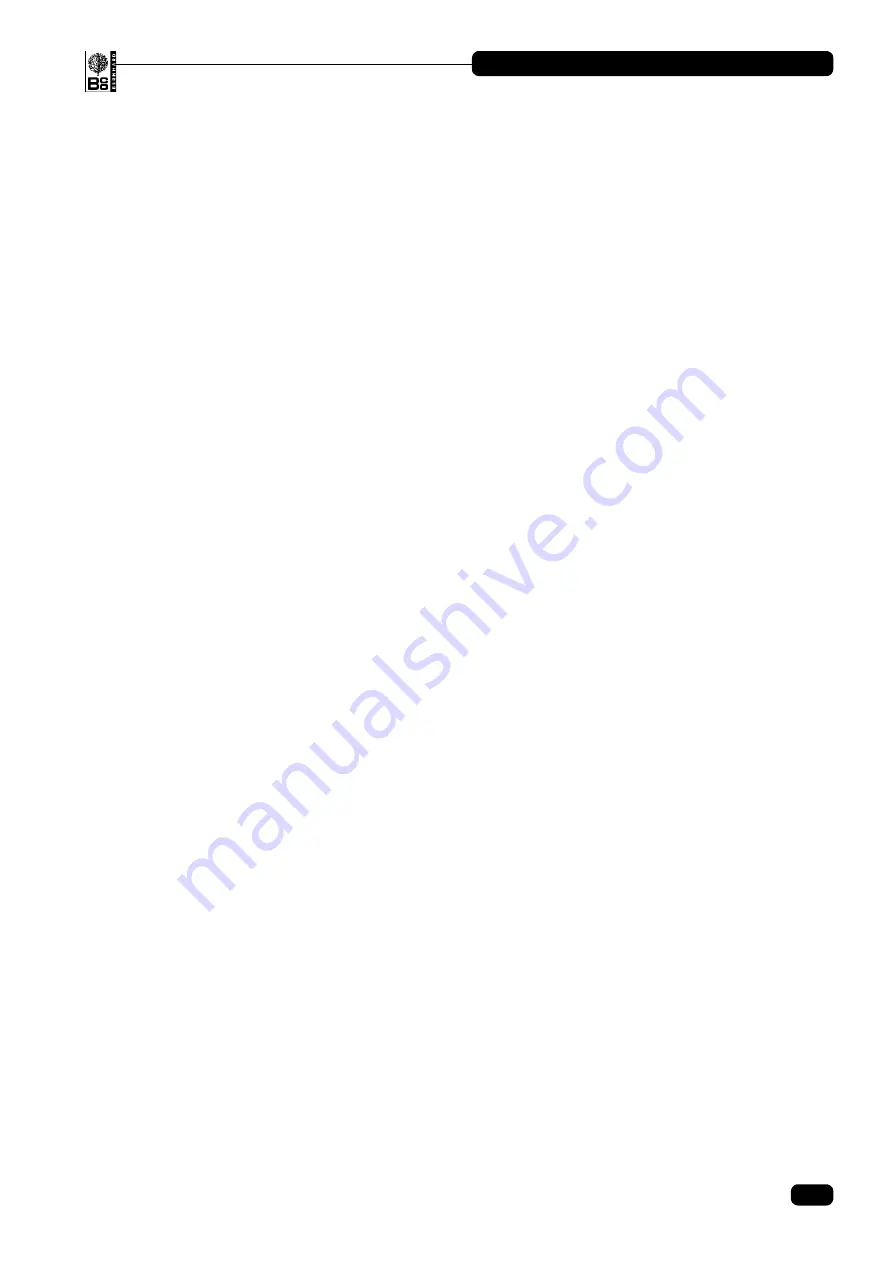
17
EXPRESS DUAL • ED3000
© Bernhard and Company Limited
6.7
To Commence Actual Grinding
NOTE
With experience and familiarity setting / applying the cut can start here, speeding up the
set up procedure
6.7.1 If the machine has them fitted,
CLOSE THE GUARDS.
6.7.2 Start the reel drive motor and check for smooth, easy running.
6.7.3 Start the grinding wheel motor.
6.7.4 Start the traverse motor, first ensuring that the traverse engagement screw is unwound
and not connected to the traverse chain.
6.7.5 Now repeat the adjustment process with the left hand on the control wheel and the right
hand on the traverse knob, moving the grinding wheel along the reel by hand using the
traverse engagement screw, winding up the left hand control wheel until the grinding wheel
strikes and sparks gently against the reel.
Repeat this process on the right hand side of the reel, raising the shaft with your right hand
and moving the grinding wheel along with your left hand. Repeat this process until the
contact along the reel is even and parallel.
6.7.6 Screw in traverse knob to engage power traverse.
NOTE
Check auto traverse is changing direction at correct point at each end of its movement.
6. In-frame Grinding
(Continued)
Summary of Contents for ED3000
Page 29: ...29 EXPRESS DUAL ED3000 Bernhard and Company Limited MAINSHAFT MOUNTING AND MAIN MOTOR DRIVE...
Page 31: ...31 EXPRESS DUAL ED3000 Bernhard and Company Limited TRAVERSE ASSEMBLY...
Page 35: ...35 EXPRESS DUAL ED3000 Bernhard and Company Limited CLAMP ASSEMBLY...
Page 37: ...37 EXPRESS DUAL ED3000 Bernhard and Company Limited MULTI FIX BRACKET ASSEMBLY...
Page 41: ...41 EXPRESS DUAL ED3000 Bernhard and Company Limited GUARD 9 Parts List Continued...
Page 43: ...43 EXPRESS DUAL ED3000 Bernhard and Company Limited LIFT TABLE 9 Parts List Continued...