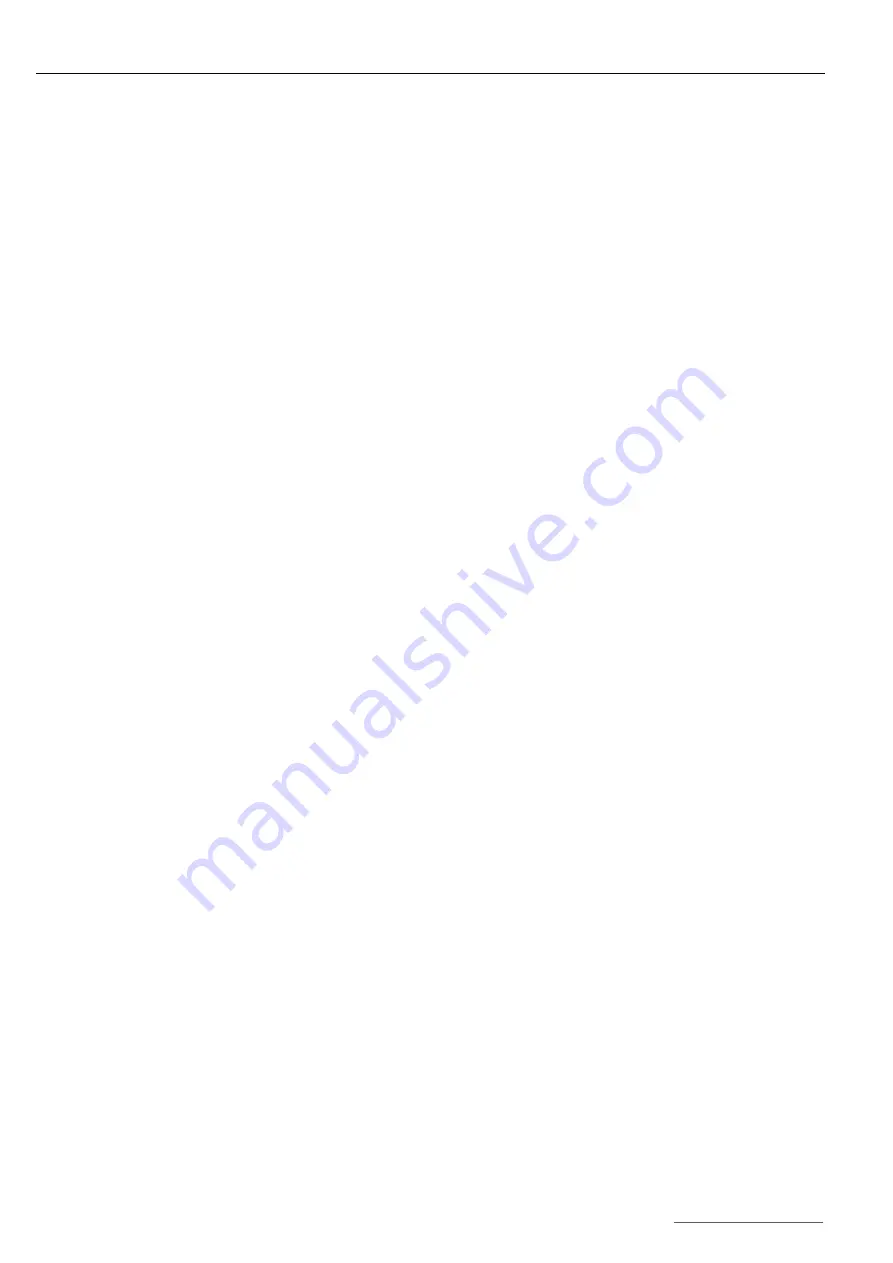
USER MANUAL 1.2 | B-FORTIS CC-PRIME SERIES
Berghof Automation GmbH | Arbachtalstrasse 26 | 72800 Eningen |
72
13.
Appendix
13.1. Notes on copyright and licence of the software
The firmware of the devices contains free software. Parts of this software are under the following
and other OpenSource licenses:
→
GNU General Public License (GPL)
→
GNU Lesser General Public License (LGPL)
→
Mozilla Public License (MPL)
→
FreeType License (FTL)
The source code of the free software can be requested from Berghof customer service at cost
price within three years of delivery of the device.
13.2. Table of figures
Fig. 12: analogue inputs a.outputs plugs X4, X5 a.X6 (Weidmüller SC-SMT 3.81/14/180 LF 3.2) 31