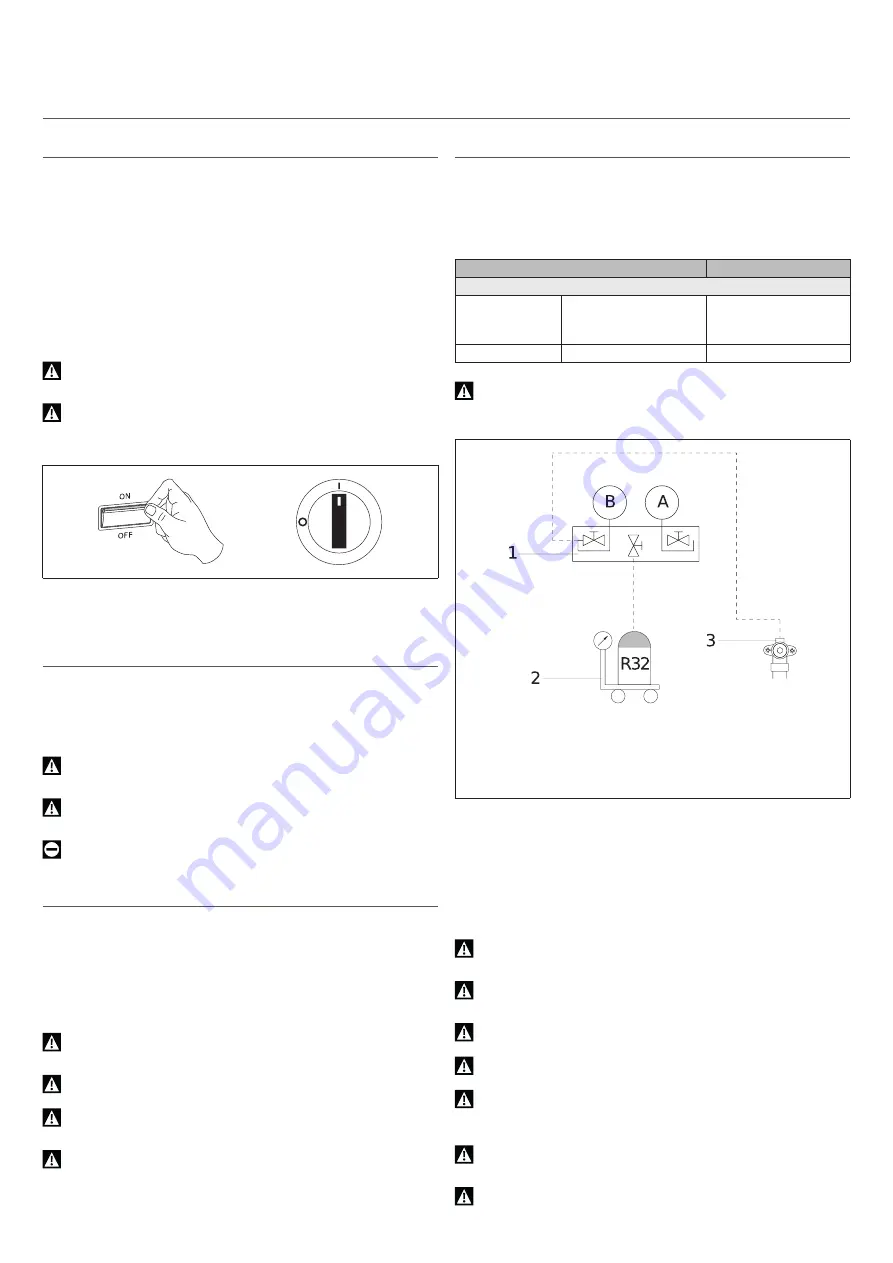
3 | COMMISSIONING AND MAINTENANCE
20
3
COMMISSIONING AND MAINTENANCE
3.1
Preparation for first commissioning
Prior to commissioning, it is necessary to check that:
- all the safety conditions have been met
- installation distances and gaps have been respected
- the indoor units have been connected to the respective
refrig-erant and electric circuit
- the electrical connections have been properly completed
- power supply values are correct.
- the earthing has been carried out correctly
- all the connections have been properly tightened
- the shut-off valves are open
The device must always be powered electrically in order to allow for
the compressor's oil to be properly pre-heated.
If the device is installed in very cold areas, the device should be
under voltage for at least 12 hours before starting it up for the first
time.
- position the system's main switch in the "ON" position.
- carry out the verification procedure of the electrical connections
3.2
Putting into service
After having completed all the operations required to prepare for first
commissioning, do the following to activate the device:
- follow the instructions given in the manual of the indoor unit that
you are installing
Keep the leak finder on and close to the unit so that it signals any
refrigerant leak.
Use an electronic leak finder properly calibrated for the system
refrigerant.
It is forbidden to use leak finders with halogen lamps.
Checks during and after the first commissioning
After starting the device, check that:
- the current consumed by the compressor is less than the
maximum permitted
- the device is operating under the recommended operating
conditions
- the unit is able to stop and start up again
Should any of the above-listed controls have problems: turn the
device off and call the Technical Service immediately.
Do not touch the device pipes to prevent potential burns.
Take anti-static precautions in case of weather conditions where
humidity is less than 40%.
Avoid using mobile phones.
Additional refrigerant charge
The units are supplied with a sufficient amount of refrigerant gas for a
pre-set length of the connection pipes.
An additional refrigerant charge is needed if such length is exceeded.
The pre-set values are detailed in the following table:
Model
18000-2
Connection pipes
Maximum length
with standard
charge
m
20
Additional charge
g/m
20
The device must be earthed before performing the additional charge.
To perform the additional charge:
A
High pressure
B
Low pressure
1
Pressure gauge unit
2
Electronic scale
3
3-way valve service connection
- connect the refrigerant cylinder to the pressure gauge unit
- connect the charging tube to the service connection on the
3-way shut-off valve
- remove the air from the charging tube
- charge the refrigerant with an electronic scale
- disconnect the charging tube from the service valve
- refit the three-way valve closing plug
Carefully check for absence of leakages from the closing point of the
plug.
Do not force beyond the stop point to prevent damaging the shaft
and causing leakage as a consequence.
Use equipment suitable for the system refrigerant.
Use only the system refrigerant.
Any gas leaks indoors can generate toxic gases if they come into
contact with naked flames or high temperature bodies, in case of
leaks, please air the rooms thoroughly.
Take anti-static precautions in case of weather conditions where
humidity is less than 40%.
Avoid using mobile phones.