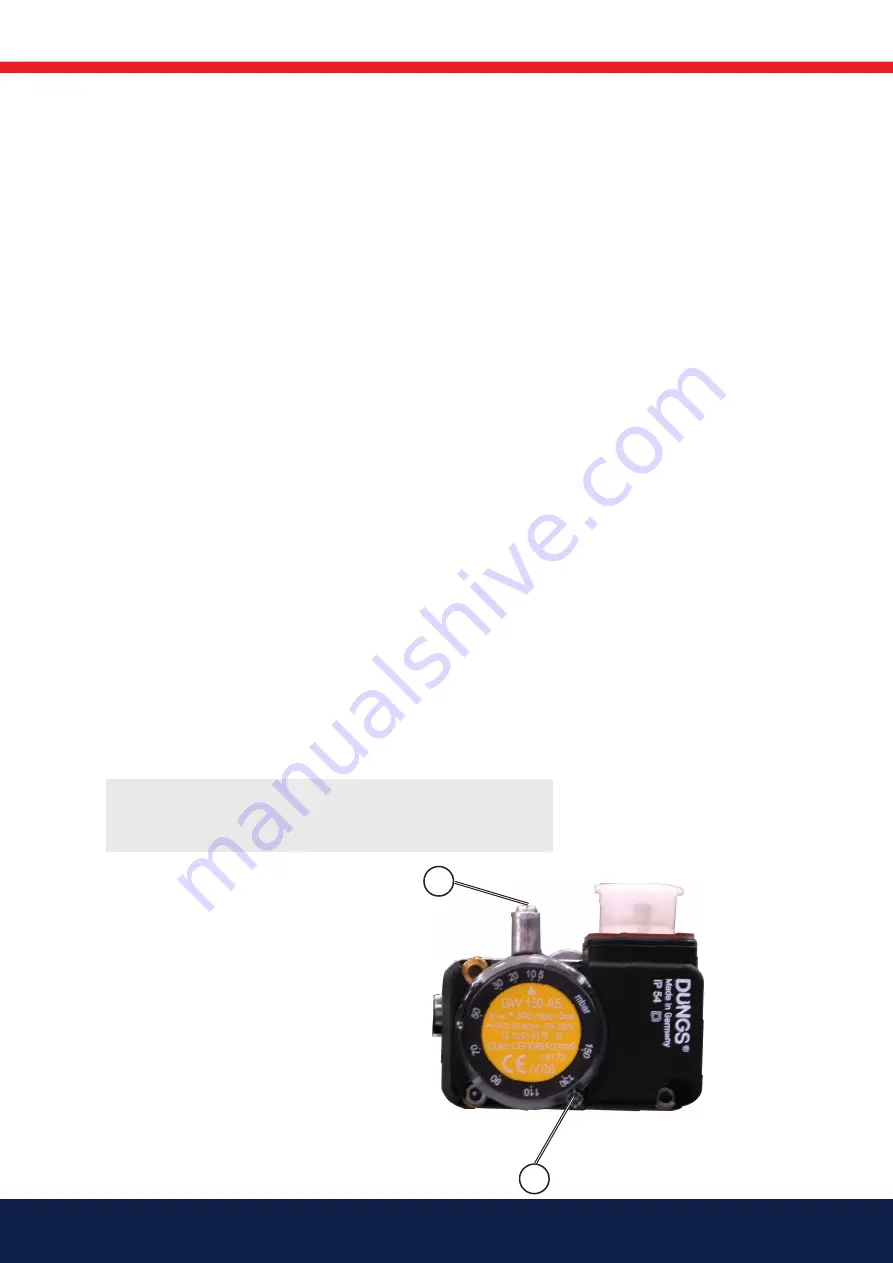
20
Bentone
5.4 Setting the min. gas pressure
switch
The min. gas pressure switch should react to a burner connection pressure
that is too low and in such cases prevent the burner from starting. If the
connection pressure to the burner is too low during operation, the min. gas
pressure switch should stop the burner. The burner can start again once
the connection pressure has risen above the pressure set for the min. gas
pressure switch.
Setting for min. gas pressure switch
1.
Remove the protective cover, screw (Y).
2.
Open the pressure outlet (X) and connect a manometer to measure the
connection pressure.
3.
Start the burner.
4.
Measure and make a note of the connection pressure to the burner
during normal operation at the highest input power.
5.
Based on the desired connection pressure set, determine the
connection pressure at which the gas pressure switch should stop the
burner. Set the connection pressure at which the burner is stopped at
a level where the burner is stopped before poor combustion occurs.
6.
Set the min. gas pressure switch to this value by turning the scale.
7.
Check the setting by carefully closing the ball valve while measuring the
connection pressure.
8.
When the min. gas pressure switch stops the burner, the value
measured should then approximately correspond to the setting on the
min. gas pressure switch. The tolerance on the scale for the min. gas
pressure switch is approx. ±15%.
9.
Open the ball valve.
10. Remove the pressure gauge and close the pressure outlet (X).
11. Fit the protective cover, screw (Y).
!
Check the gas tightness.
X
Y
Summary of Contents for BG400M
Page 15: ...15 Bentone 172 515 08 2018 01 02 4 8 Gas nozzle Natural gas Propan Biogas UV detector 2 5 8 0 ...
Page 35: ...35 Bentone 10 2 Wiring diagram LME ...
Page 44: ......
Page 45: ......
Page 46: ......
Page 47: ......
Page 48: ...Enertech AB P O Box 309 SE 341 26 Ljungby www bentone com ...