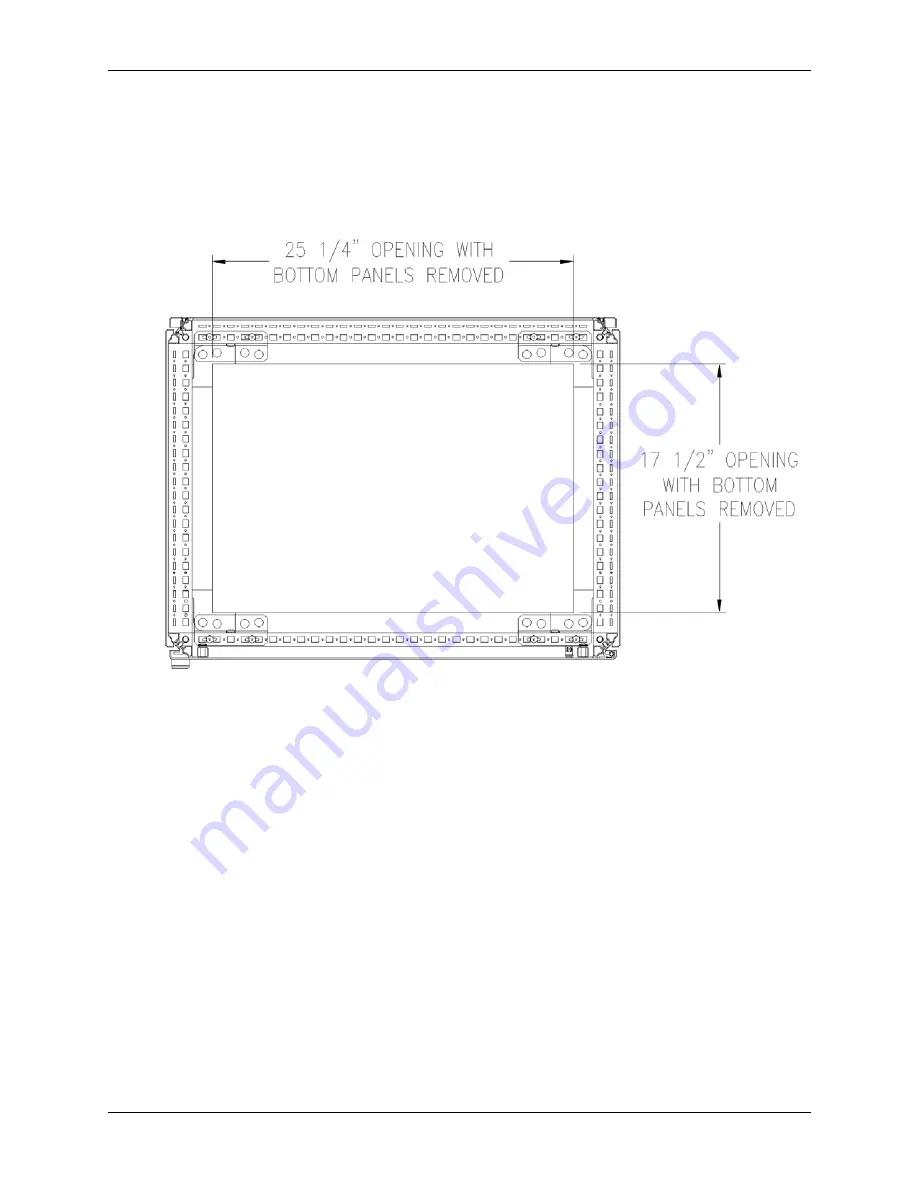
Multiple Disconnect Safety System Installation and Operating Instructions
950-001568-000 Rev A
22
Chapter 3: Installation Procedure
shows the bottom of the enclosure for double-stacked and dual-column
models. The gland plates have been removed. The recommended opening for
cables is through the bottom with one or more of the gland plates removed.
Figure 9
Bottom view of the enclosure for double-stacked and dual-column
models, showing panels removed
The single-column model has a 1-5/8 x 13/16-inch strut across the bottom. The
gland plate beneath the strut can be removed by removing the screws and
angling the panel to slide it out. The following four views of the single column
model show the measurements depending on the size of the disconnect and the
presence or absence of a dead front.