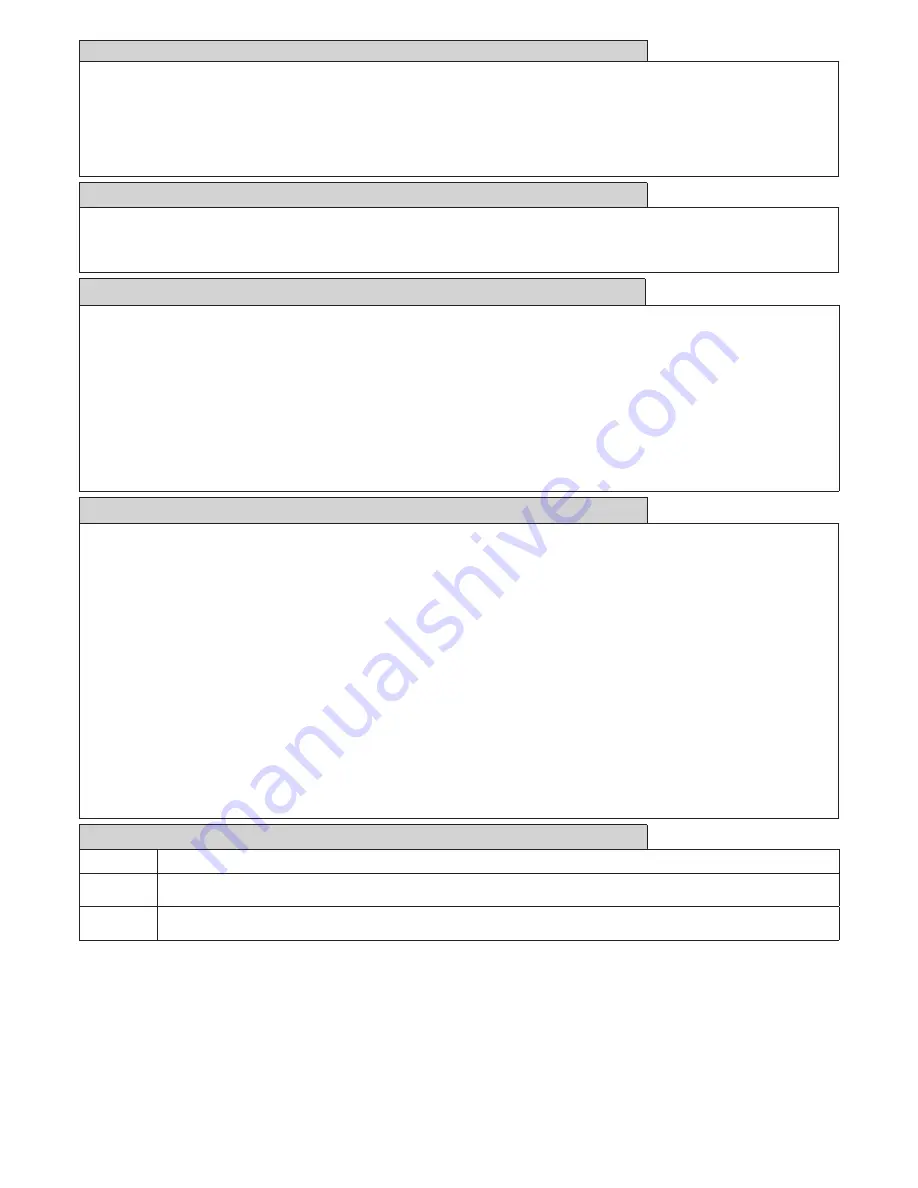
26
13.3.6) MAINTENANCE CYCLES (
MACI
)
This function enables to activate the maintenance request notice after a number of manoeuvres determined by the installer.
To activate and select the number of manoeuvres, proceed as follows:
Press button <PG>, the display will show OFF, which indicated that the function is disabled (default value).
With the buttons <+> and <-> select one of the numeric values proposed (from OFF to 100). The values are intended as hundreds of cycles of ma-
noeuvres (for example: the value 50 indicates 5000 manoeuvres).
Press the OK button to activate the function. The display will show the message
PROG
.
The maintenance request is indicated to the user by keeping the indicator lamp lit up for other 10 sec after the conclusion of the opening or closing
operation.
13.3.7) RESET (
RES
)
RESET of the control unit. ATTENTION!: Returns the control unit to the default values.
Pressing the <PG> button for the first time causes blinking of the letters
RES
, pressing the <PG> button again resets the control unit. Note: The trans-
mitters are not erased from the receiver nor is the access password.
All the logics and all the parameters are brought back to default values, it is therefore necessary to repeat the autoset procedure.
13.3.8) AUTOSET (
AUTO
)
This function sets the optimal functioning values of the installation, at the end of the procedure, it sets the average values of torque (PMO/PMC and PSO/PSC).
To carry out the AUTOSET, proceed as follow:
a) Make sure that during the autoset there is no obstacle is in the maneuver area, if necessary, fence off the area so that persons, animals, cars, etc.,
cannot interrupt the procedure.
During the AUTOSET procedure, the anti crushing feature is not enabled.
b) select the function AUTO and press PG.
c) the control unit waits the confirmation to start the procedure “PUSH”
c) press PG to start the AUTOSET procedure.
The control unit performs few maneuvers for the stroke learning and the configuration of the parameters.
In case that the procedure is not successful the message ERR will be shown. Repeat the procedure after checking the wirings and the possible pres-
ence of obstacles.
The control unit recognizes automatically the presence of the absolute encoder, electromechanical limit switches or mechanical stops during the
AUTOSET procedure. In case of use with encoder or mechanical stops do not link the inputs SWO-SWC to the common.
13.3.9) PASSWORD (
CODE
)
It allows to type in an access protection code to the programming of the control unit.
A four-character alphanumeric code can be typed in by using the numbers from 0 to 9 and the letters A-B-C-D-E-F.
The default value is 0000 (four zeros) and shows the absence of a protection code.
While typing in the code, this operation can be cancelled at any moment by pressing keys + and – simultaneously. Once the password is typed in,
it is possible to act on the control unit by entering and exiting the programming mode for around 10 minutes in order to allow adjustments and tests
on functions.
By replacing the 0000 code with any other code, the protection of the control unit is enabled, thus preventing the access to any other menu. If a
protection code is to be typed in, proceed as follows:
- select the Code menu and press OK.
- the code 0000 is shown, also in the case a protection code has been previously typed in.
- the value of the flashing character can be changed with keys + and -.
- press OK to confirm the flashing character, then confirm the following one.
- after typing in the 4 characters, a confirmation message “CONF” appears.
- after a few seconds, the code 0000 appears again
- the previously stored protection code must be reconfirmed in order to avoid any accidental typing in.
If the code corresponds to the previous one, a confirmation message “
OK
” appears.
The control unit automatically exits the programming phase. To gain access to the Menus again, the stored protection code must be typed in.
IMPORTANT: TAKE NOTE of the protection code and KEEP IT IN A SAFE PLACE for future maintenance operations.
To remove a code from a protected control unit it is necessary to enter into programming with the password and bring the code back to
the 0000 default value.
IF YOU LOOSE THE CODE, PLEASE CONTACT THE AUTHORISED SERVICE CENTER FOR THE TOTAL RESET OF THE CONTROL UNIT.
13.3.10) SYNCHRONIZATION (
BUS
)
MENU
FUNZIONE
id
Sets the synchronizing number. It is possible to set a numeric value from 0 to 16.
If the ID parameter is to 0 the control unit is set as MASTER, all the other values set the barrier as SLAVE.
loc
Allows a barrier set as SLAVE to receive local commands.
See paragraph 12.4 “SYNCHRONIZATION OF TWO OPPOSED BARRIERS”
13.4) SYNCHRONIZATION OF TWO OPPOSED BARRIERS
It is possible to manage a system composed of two barriers by using for each CP.EVA2 the specific optional control unit SIS, which must be plugged
into the appropriate connector as shown in Fig. 14.
Each SIS unit must be connected to the other one by means of 3 wires by 0,5 sq.mm each, as shown in Fig.15.
One of the control unit must be set as MASTER (ID=0) and the other one as SLAVE (ID>0).
All the commands (commands given by transmitters, push buttons or safety devices) received by the MASTER barrier are sent to the SLAVE barrier,
which will replicate instantaneously the behavior of the MASTER.
The logic LOC can be set in two ways:
ON: the SLAVE barrier can accept a local command and execute an opening/closing maneuver with no effect on the MASTER barrier.
OFF: the SLAVE barrier do not accept any local command and so it will replicate exclusively the behavior of the MASTER barrier.
A SLAVE barrier with LOC set to ON can be useful in case it is occasionally necessary the partial opening of a passage which is usually managed by two
synchronized barriers, since that a step by step command (or OPEN/CLOSE) given to the SLAVE will have effect only on this last one, while all the other
commands given to the MASTER will be replicated by the SLAVE.
The connection of the safety devices (photocells, safety edges, etc.) can be done indifferently to the MASTER unit or to the SLAVE.