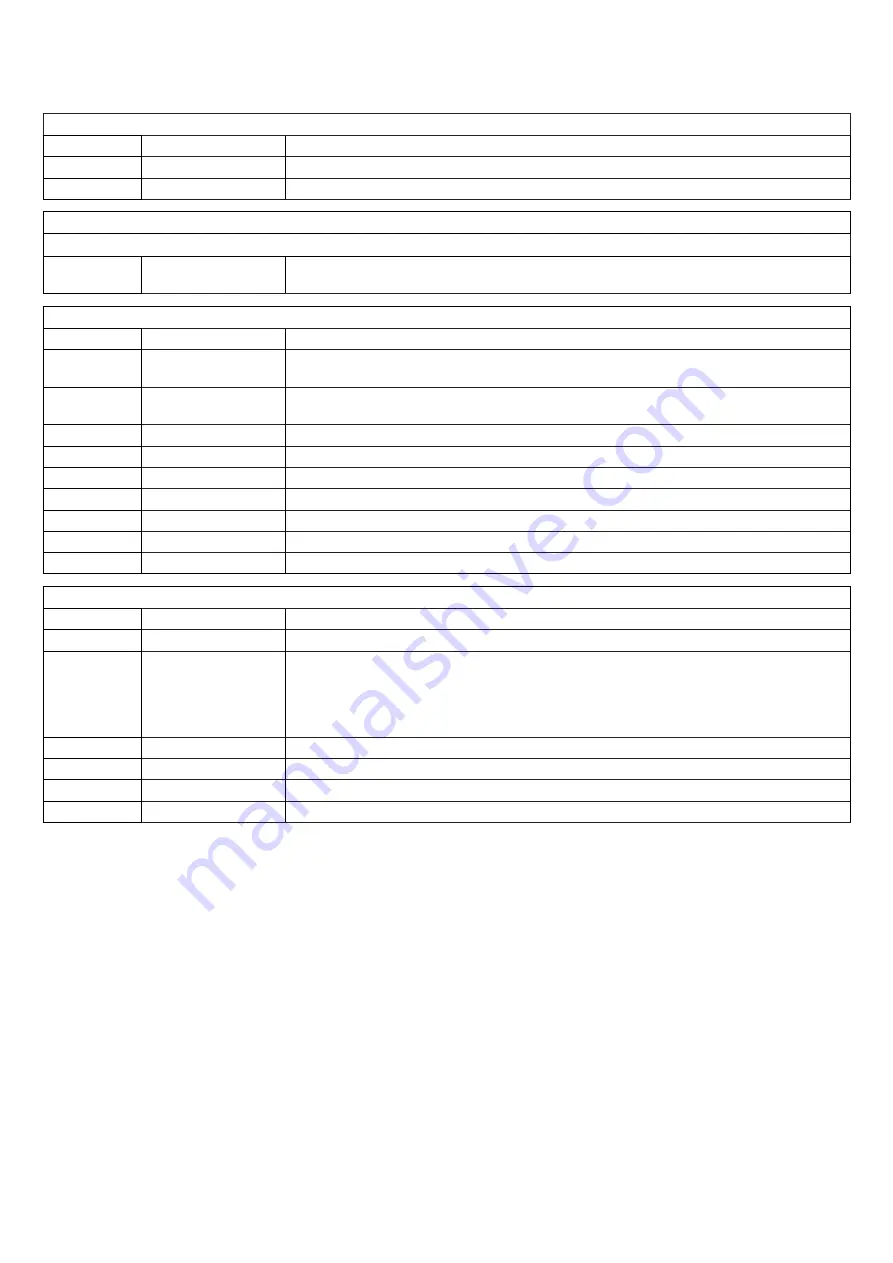
24
8) CP.B1524 CONTROL UNIT
8.1) WIRE DIAGRAM
Wire connections shown in Fig. 16 are described hereunder:
SA.24V
L-N-GND
Power supply
Mains input 100÷250Vac 50/60Hz
+ -
Output 24Vdc
Controller CP.1524 power supply output 24 Vdc
BAT-BAT
Batteries
Clamp input for connection of back-up batteries (accessory).
CP.B 1524
TERMINAL BLOCK M1
+ -
24Vdc INPUT
24Vdc input for powering the CP.B1524.In case of use of the SUN SYSTEM it is necessary to connect
the 24Vdc output of the SUN.SY to M1 (see the KSUN instructions)
TERMINAL BLOCK M2
P.P.
Step by step
Input for step by step command (N.O. contact) or OPEN (Log OPCL) .
PED
Pedestrial
Input, pedestrian push-button (N.O. contact). It controls the partial opening. Configuration is through pa-
rameter PED. When TCA time has elapsed (if activated) a closure control signal is sent or close (Log OPCL).
PHOTO
Photocell opening/
closing
Input, photocell activated in both opening and closing phases
PHOTC
Photocell closing
Input, photocell activated in closing phase only (Normally closed contact)
STOP
STOP
Input for STOP command (N.C. contact).
SWC
Closing limit switc
h
Input for closing limit switch (N.C. contact).
SWO
Opening limit switch
Input for opening limit switch (N.C. contact).
COM
Common
Common for all the input commands and the limit switches .
AUX2
Output 24Vdc/1A
Output max. 24Vdc/1A settable via AUX2 operating logic.
BLINK
Blinker
Output 24Vdc 15W max. for flashing light connection.
TERMINAL BLOCK M3
TERMINALS
Function
Description
ANT-SHIELD
Antenna
Connection for the antenna of the built in receiver (ANT-signal/SHIELD-shield).
BAR
Safety edge
Input, safety edge
Resistive edge: “DAS” Jumper closed
Mechanical edge: “DAS” Jumper open
When the edge is activated, the gate movement is stopped and reversed for about 3s.
If the edge is not in use: “DAS” Jumper open, BAR terminals are short-circuited.
AUX 1
Auxiliary output AUX 1
Output with N.O. contact configurable by means of the logic AUX 1
24V
24 Vdc
Accessory power supply 24Vdc 500 mA maximum
MOT
Motor
Motor connection: 24Vdc.
N/A
Not used
8.2) PROGRAMMING
The programming of the various functions of the control unit is carried out using the LCD display on the control unit and setting the desired values in
the programming menus described below.
The parameters menu allows you to assign a numerical value to a function, in the same way as a regulating trimmer.
The logic menu allows you to activate or deactivate a function, in the same way as setting a dip-switch.
8.2.1) TO ACCESS PROGRAMMING
1 -Press the <PG> button to enter the first Installation menu “INST”.
2 -Choose with <+> or <-> button the menu you want to select (see menu at page 10-11)
3 - Press the button <PG>, the display shows the first function available on the menu.
4 - With the <+> or <-> button, select the function you want.
5 - Press the button <PG>, the display shows the value currently set for the function selected.
6 - With the <+> or <-> button, select the value you intend to assign to the function.
7 - Press the button <PG>, the display shows the signal “PRG” which indicates that programming has been completed.
8.2.2) PROGRAMMING NOTES
Simultaneously pressing <+> and <-> from inside a function menu allows you to return to the previous menu without making any changes. Hold down
the <+> key or the <-> key to accelerate the increase/decrease of the values.
Hold down the <+> key or the <-> key to accelerate the increase/decrease of the values.
After waiting 120s the control unit quits programming mode and switches off the display.
When the board is switched on, the software version is displayed for around 5 sec
The pre-set logic functions and parameters are made taking account of a typical installation.
Summary of Contents for BULL 1524
Page 2: ...2 A B 1 200 245 316 340 300 215 340 34mm BULL PI Optional 40 3 1 8 2 0 4 7 0 1 8 0 2 3 ...
Page 3: ...3 V Z R 4 7 B F T MIN 10 mm MAX 20 mm MIN 120 mm MAX 140 mm 5 6 R D R D ...
Page 5: ...5 12 13 14 C L 7 4 1 2 3 POWER 2 x 1 5 RG 58 5 4 x 0 25 4 6 5 2 x 0 25 3 x 0 25 15 ...
Page 9: ...9 22 DA BT6 ...