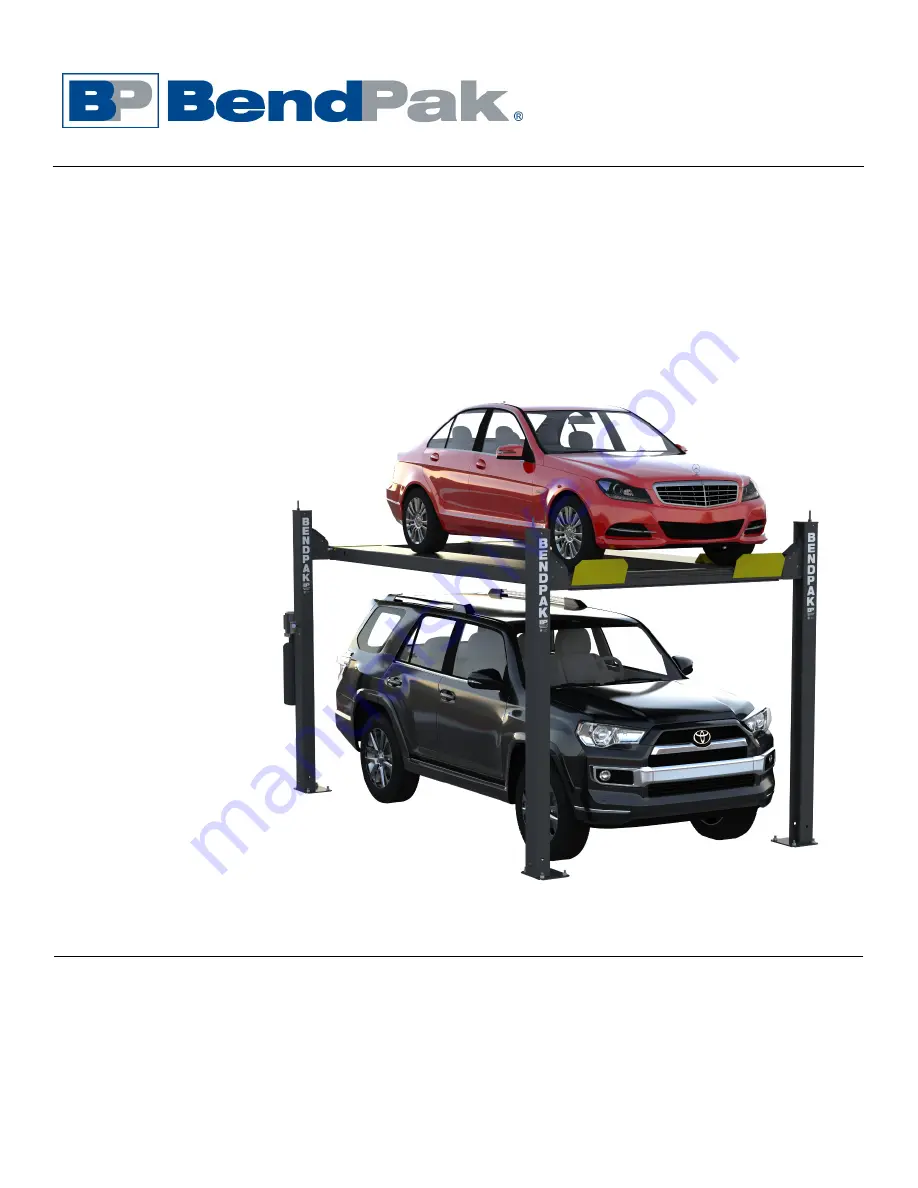
1645 Lemonwood Dr.
Santa Paula, CA 93060 USA
Toll Free: (800) 253-2363
Telephone: (805) 933-9970
Four-Post Lifts
Installation and Operation Manual
Manual P/N 5900041 — Manual Revision M — July 2019
Models:
•
HD-7P
•
HD-7W
Designed and engineered by BendPak Inc. in Southern California, USA. Made in China.
⚠
DANGER
Read the
entire contents
of this manual
before
using this
product. Failure to follow the instructions and safety precautions in
this manual can result in serious injury or death. Make sure all other
operators also read this manual. Keep the manual near the product
for future reference. By proceeding with installation and operation,
you agree that you fully understand the contents of this manual.
Summary of Contents for HD-7P
Page 8: ...HD 7P HD 7W Four Post Lifts 8 P N 5900041 Rev M July 2019 Specifications ...
Page 78: ...HD 7P HD 7W Four Post Lifts 78 P N 5900041 Rev M July 2019 5585182 5585247 ...
Page 79: ...HD 7P HD 7W Four Post Lifts 79 P N 5900041 Rev M July 2019 Labels ...
Page 80: ...HD 7P HD 7W Four Post Lifts 80 P N 5900041 Rev M July 2019 ...
Page 81: ...HD 7P HD 7W Four Post Lifts 81 P N 5900041 Rev M July 2019 ...
Page 82: ...HD 7P HD 7W Four Post Lifts 82 P N 5900041 Rev M July 2019 Parts Drawings ...
Page 83: ...HD 7P HD 7W Four Post Lifts 83 P N 5900041 Rev M July 2019 ...
Page 84: ...HD 7P HD 7W Four Post Lifts 84 P N 5900041 Rev M July 2019 ...
Page 85: ...HD 7P HD 7W Four Post Lifts 85 P N 5900041 Rev M July 2019 ...
Page 86: ...HD 7P HD 7W Four Post Lifts 86 P N 5900041 Rev M July 2019 ...
Page 87: ...HD 7P HD 7W Four Post Lifts 87 P N 5900041 Rev M July 2019 ...
Page 88: ...HD 7P HD 7W Four Post Lifts 88 P N 5900041 Rev M July 2019 ...
Page 89: ...HD 7P HD 7W Four Post Lifts 89 P N 5900041 Rev M July 2019 ...
Page 91: ...HD 7P HD 7W Four Post Lifts 91 P N 5900041 Rev M July 2019 Maintenance Log ...