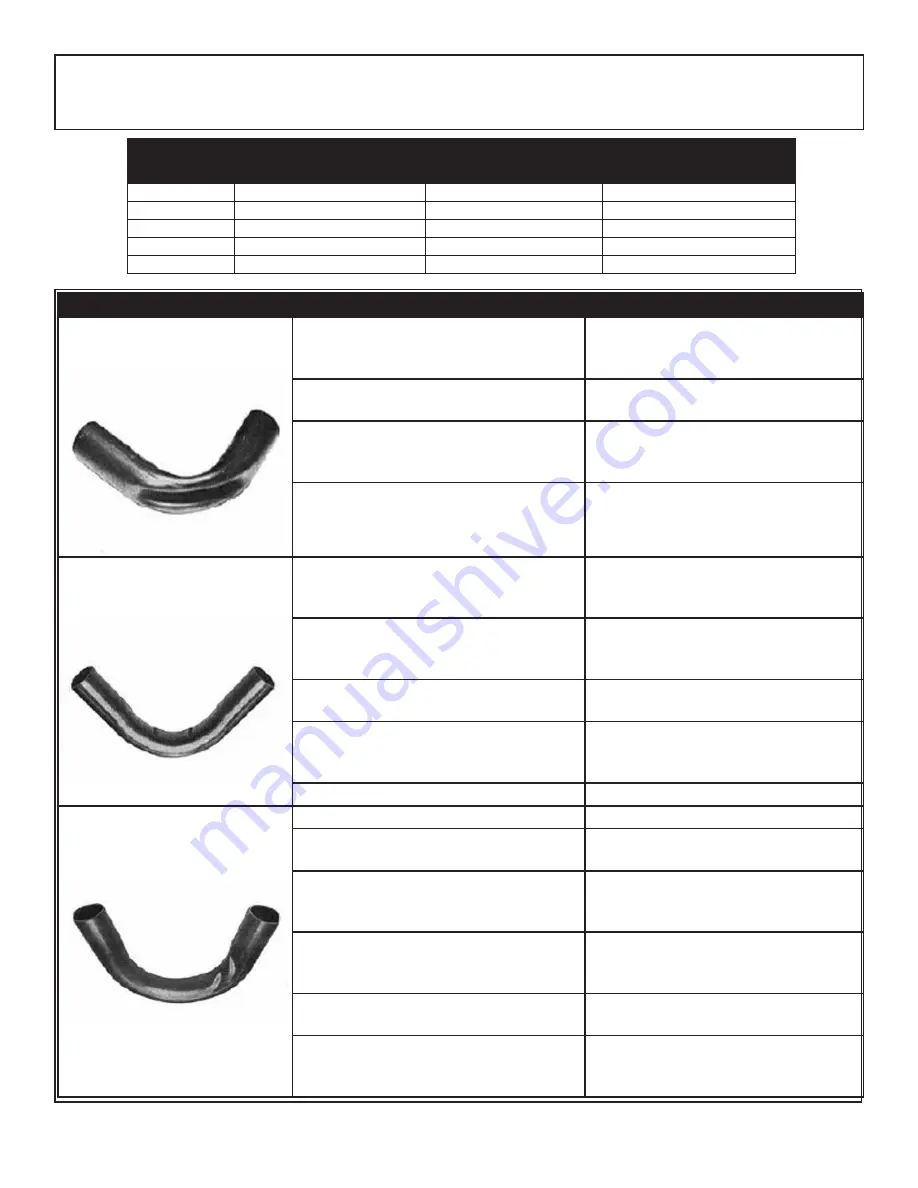
Bender Operation Manual 45
BENDING PROBLEMS
Bending complications can be usually attributed to tubing thickness, tubing quality or improper radius
selection. The bigger the tubing diameter, the bigger the radius and wall thickness should be. See the chart
below for minimum tubing thickness and proper radius selection.
SYMPTOM / CONDITION
POSSIBLE CAUSE
CORRECTIVE ACTION
Flattening or collapsing of pipe on
outside of bend.
Incorrect back pressure. Usually a low
pressure problem.
Adjust back pressure as shown on page
33. For 3”diameter tube see bending
instructions found on page 21
Bending dies are not properly matched to
the tubing diameter.
Select proper bending dies for the
particular tubing diameter.
Tubing diameter is actually less or more
than what it is labeled.
Check the actual tubing diameter using
a micrometer or similar measuring
device.
Gauge thickness is less than the
recommended requirement. See chart
above for minimum tubing thickness.
Check tubing for proper wall thickness.
See chart above.
Dimpling of pipe on inside of
bend.
Incorrect back pressure.
Adjust back pressure as shown on page
33. For 3” diameter tube see bending
instructions found on page 21
Gauge thickness is less than the
recommended requirement. See chart
above for minimum tubing thickness.
Check tubing for proper wall thickness.
See chart above.
Bending dies are not properly matched to
the tubing diameter.
Select proper bending dies for
the particular tubing diameter.
Tubing diameter is actually less or more
than what it is labeled.
Check the actual tubing diameter using
a micrometer or similar measuring
devise.
Improper chain adjustment.
Adjust chains as described on page 34.
Crimping or wrinkling of pipe.
Improper die alignment.
Check the following.
Bronze barrel bushings may be worn.
Remove and replace the bushings as
described on page 36.
Guide plate may be mis-aligned. Check
proper alignment as described on page
35.
Adjust and shim guide plate as described
on page 35.
Pusher block may be worn. Check for
proper tolerance as described on page
38.
Remove and replace pusher block as
required.
Bending dies are not properly matched to
the tubing diameter.
Select proper bending dies for
the particular tubing diameter.
Tubing diameter is actually less or more
than what it is labeled.
Check the actual tubing diameter using
a micrometer or similar measuring
device.
Tubing Diameter Minimum Tubing Thickness
5" Radius
Minimum Tubing Thickness
4" Radius
Minimum Tubing Thickness
3 1/2" Radius
1”- 1-3/4”
18 Gauge / .049
16 Gauge / .065
16 Gauge / .065
1-7/8” - 2”
16 Gauge / .065
16 Gauge / .065
16 Gauge / .065
2-1/4”
16 Gauge / .065
14 Gauge / .083
14 Gauge / .083
2-1/2”
14 Gauge / .083
14 Gauge / .083
N/A
3”
13 Gauge / .095
N/A
N/A
Summary of Contents for Blue Bullet 1302-BAS
Page 46: ...46 Bender Operation Manual ...
Page 51: ...Bender Operation Manual 51 ...
Page 52: ...52 Bender Operation Manual ...
Page 53: ...Bender Operation Manual 53 ...
Page 54: ...54 Bender Operation Manual ...
Page 55: ...Bender Operation Manual 55 ...
Page 56: ...56 Bender Operation Manual ...
Page 57: ...Bender Operation Manual 57 ...
Page 63: ...Bender Operation Manual 63 ...
Page 64: ...64 Bender Operation Manual ...