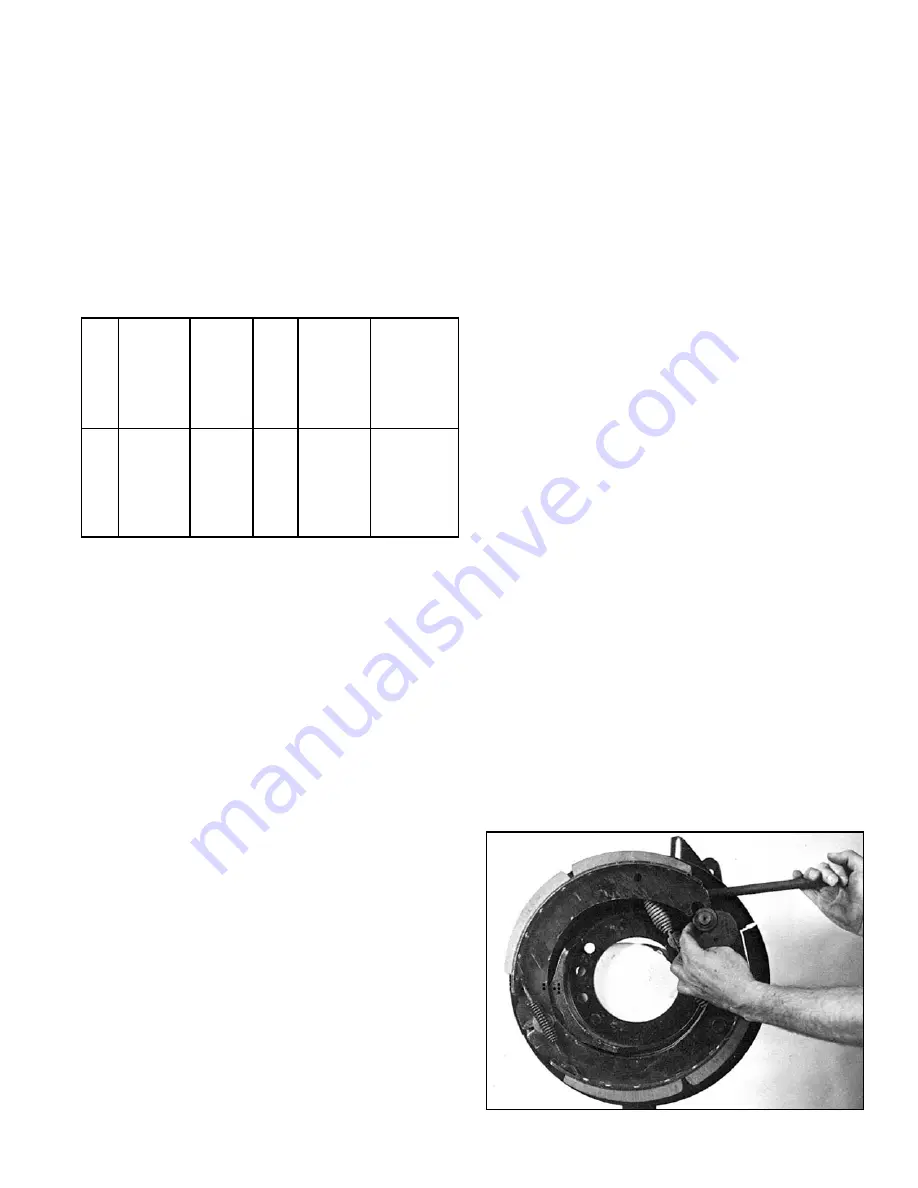
3
PREVENTIVE MAINTENANCE
Important:
Review the warranty policy before performing
any intrusive maintenance procedures. An extended warranty
may be voided if intrusive maintenance is performed during
this period.
Because no two vehicles operate under identical conditions,
maintenance intervals will vary. Experience is a valuable guide
in determining the best maintenance interval for a vehicle.
1. BRAKE ADJUSTMENT
Weekly, or whenever push rod stroke exceeds maximum
distance listed on the following chart. For complete
adjustment information, see Bendix Service Data sheet
SD-05-1.
Full Pressure
Ser-
Service
Max.
Max. Stroke
vice Diaphragm
Stroke
at which
Act-
Effective
With
Brakes
uator
Area
Outside
Max.
Brakes
Should Be
Type
(Sq. In.)
Diameter Stroke Adjusted
Readjusted
12
12
5-11/16 1-3/4
short as
1-3/8
16
16
6-3/8
2-1/4 possible
1-3/4
20
20
6-25/32 2-1/4
without
1-3/4
24
24
7-7/32
2-1/4
brakes
1-3/4
dragging
2. BRAKE LUBRICATION
Grease camshaft bracket with vehicle manufacturer’s
recommended chassis lube. Lube once every six months
or at each chassis lubrication.
3. BRAKE RELINE
The life of the brake lining is dependent on many factors
such as the material of the lining, type of operation the
vehicle is used for, and the driver of the vehicle. If driving
conditions require frequent braking, lining replacement
will be required more often. Reline when lining thickness
at center of shoe is 5/16”. Refer to section “Reline
Procedure”.
4. BRAKE OVERHAUL
As often as necessary to maintain adequate brake
performance. NOTE: When overhauling brake system,
provide equal service to all drive axle brakes on the
vehicle.
WARNING! PLEASE READ AND FOLLOW
THESE INSTRUCTIONS TO AVOID
PERSONAL INJURY OR DEATH:
When working on or around a vehicle, the following
general precautions should be observed at all times.
1. Park the vehicle on a level surface, apply the
parking brakes, and always block the wheels.
Always wear safety glasses.
2. Stop the engine and remove ignition key when
working under or around the vehicle. When
working in the engine compartment, the engine
should be shut off and the ignition key should be
removed. Where circumstances require that the
engine be in operation, EXTREME CAUTION should
be used to prevent personal injury resulting from
contact with moving, rotating, leaking, heated or
electrically charged components.
3. Do not attempt to install, remove, disassemble or
assemble a component until you have read and
thoroughly understand the recommended
procedures. Use only the proper tools and observe
all precautions pertaining to use of those tools.
4. If the work is being performed on the vehicle’s air
brake system, or any auxiliary pressurized air
systems, make certain to drain the air pressure
from all reservoirs before beginning ANY work on
the vehicle. If the vehicle is equipped with an AD-
IS
™
air dryer system or a dryer reservoir module,
be sure to drain the purge reservoir.
5. Following the vehicle manufacturer’s
recommended procedures, deactivate the electrical
system in a manner that safely removes all electrical
power from the vehicle.
6. Never exceed manufacturer’s recommended
pressures.
7. Never connect or disconnect a hose or line
containing pressure; it may whip. Never remove a
component or plug unless you are certain all
system pressure has been depleted.
8. Use only genuine Bendix
®
replacement parts,
components and kits. Replacement hardware,
tubing, hose, fittings, etc. must be of equivalent
size, type and strength as original equipment and
be designed specifically for such applications and
systems.
9. Components with stripped threads or damaged
parts should be replaced rather than repaired. Do
not attempt repairs requiring machining or welding
unless specifically stated and approved by the
vehicle and component manufacturer.
FIGURE 3 -
REMOVING CAM ROLLERS
Summary of Contents for SINGLE ANCHOR PIN CAM BRAKE
Page 11: ...11...