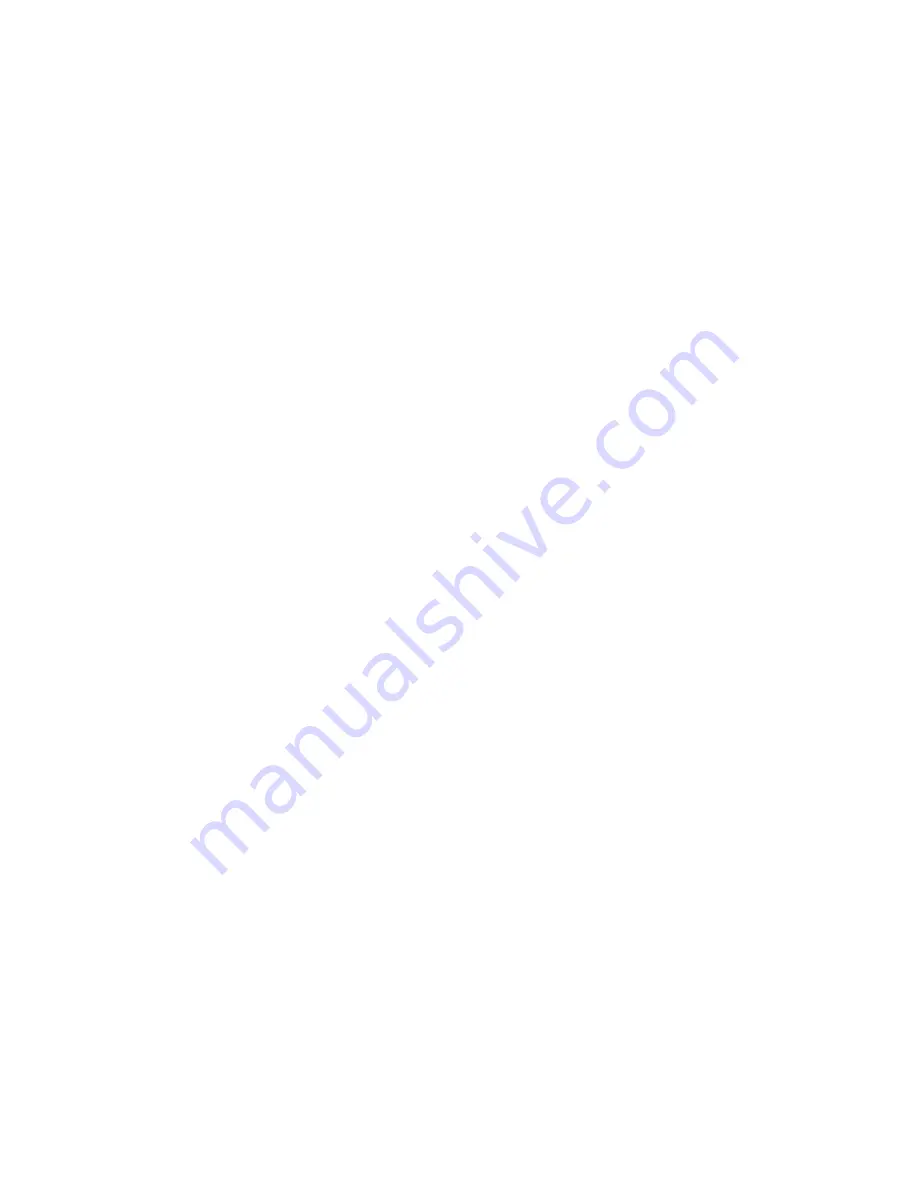
2
BALANCED
The air pressure being delivered by the open inlet valve also
is effective on the bottom area of the relay piston. When this
delivery air pressure beneath the piston equals the service
air pressure above, the piston moves up slightly and the
inlet spring returns the inlet valve to its seat. The exhaust
remains closed as service line pressure balances delivery
pressure.
RELEASING
When air pressure is exhausted from the service port, the
diaphragm in the quick release moves, blocking the service
inlet and opening the exhaust of the quick release allowing
the air that was acting on the relay piston to be exhausted
at the quick release. When the air above the relay piston is
exhausted, the air beneath the piston will lift the piston and
the exhaust seat moves off the exhaust valve exposing the
exhaust passage to atmosphere. With the exhaust passage
open, the air pressure in the emergency or park actuators
exhausts out the exhaust port to atmosphere.
ANTI-COMPOUNDING (SIMULTANEOUS
SERVICE AND PARK APPLICATION)
In those applications where the R-8
™
relay valve is used to
control spring brake chambers, the anti-compound feature
may be utilized. With the anti-compound feature of the R-8
™
valve connected, a service application made while the vehicle
is parked is countered by a release of the parking brakes.
To utilize this feature, the exhaust cover of the quick release
portion of the R-8
™
valve is removed and a line is installed
which is connected to the delivery of the service brake valve
or relay valve. With no air pressure at the service port of the
R-8
™
valve, the parking brakes are applied. If a service brake
application is made, air from the service brake valve enters
the exhaust port of the quick release on the R-8
™
valve and
moves the diaphragm, blocking the service port. Air then
proceeds into the cavity above the relay piston, forces the
piston down, closing the exhaust and opening the inlet to
deliver air to the spring brake cavity as described under the
section of this manual entitled APPLYING.
PREVENTIVE MAINTENANCE
Important:
Review the Bendix Warranty Policy before
performing any intrusive maintenance procedures. A warranty
may be voided if intrusive maintenance is performed during
the warranty period.
No two vehicles operate under identical conditions, as a
result, maintenance intervals may vary. Experience is a
valuable guide in determining the best maintenance interval
for air brake system components. At a minimum, the valve
should be inspected every 6 months or 1500 operating hours,
whichever comes first, for proper operation. Should the valve
not meet the elements of the operational tests noted in this
document, further investigation and service of the valve may
be required.
OPERATING AND LEAKAGE TEST
1. Check the wheels and fully charge the air system.
Adjust the brakes.
2. Apply and release the parking brakes several times and
check for prompt response of the brakes at all
appropriate wheels.
3. With the park control valve in the brakes “applied position”,
coat the exhaust port with a soap solution to check for
inlet valve and o-ring leakage; a 1" bubble in 5 seconds
is permissible.
4. Place the park control valve in the “brakes released”
position and again check at the exhaust port for leakage
of the exhaust valve; a 1" bubble in 3 seconds is
permissible. Apply soap solution around the valve where
the cover joins the body to check for seal ring leakage;
no leakage permitted.
5. With the park control still in the brakes released position,
apply soap solution to the quick release exhaust port to
check the diaphragm exhaust seat; a 1" bubble in 3
seconds is permitted.
(NOTE: If the anti-compound feature is in use, the line
attached to the R-8
™
valve quick release exhaust
must be disconnected to perform this test.)
If the valve does not function as described above, or if
leakage is excessive, it is recommended that the valve
be replaced with a new or remanufactured unit, or
repaired with genuine Bendix parts available at Bendix
outlets.
REMOVING
1. Block or hold the vehicle by means other than the
brakes.
2. Drain all air brake system reservoirs.
3. Identify, mark, and disconnect all air lines from the R-8
™
relay valve.
4. Remove the R-8
™
valve from its mount on the vehicle.
(NOTE: The inlet and exhaust valve assembly, (generally
referred to as the insert) can be easily removed and
replaced. Remove the exhaust cover cap screws
and cover. Normally the insert can be removed
without disturbing the valve mounting or connecting
lines. CAUTION: DRAIN ALL RESERVOIRS
BEFORE ATTEMPTING TO REMOVE THE
INSERT.
DISASSEMBLY
1. Prior to disassembly of the R-8
™
valve, mark the
relationship of the cover and body to facilitate assembly.
2. Remove the four 5/16" hex head cap screws and
lockwashers that secure the cover to the body and
separate the valve halves: remove the piston spring.