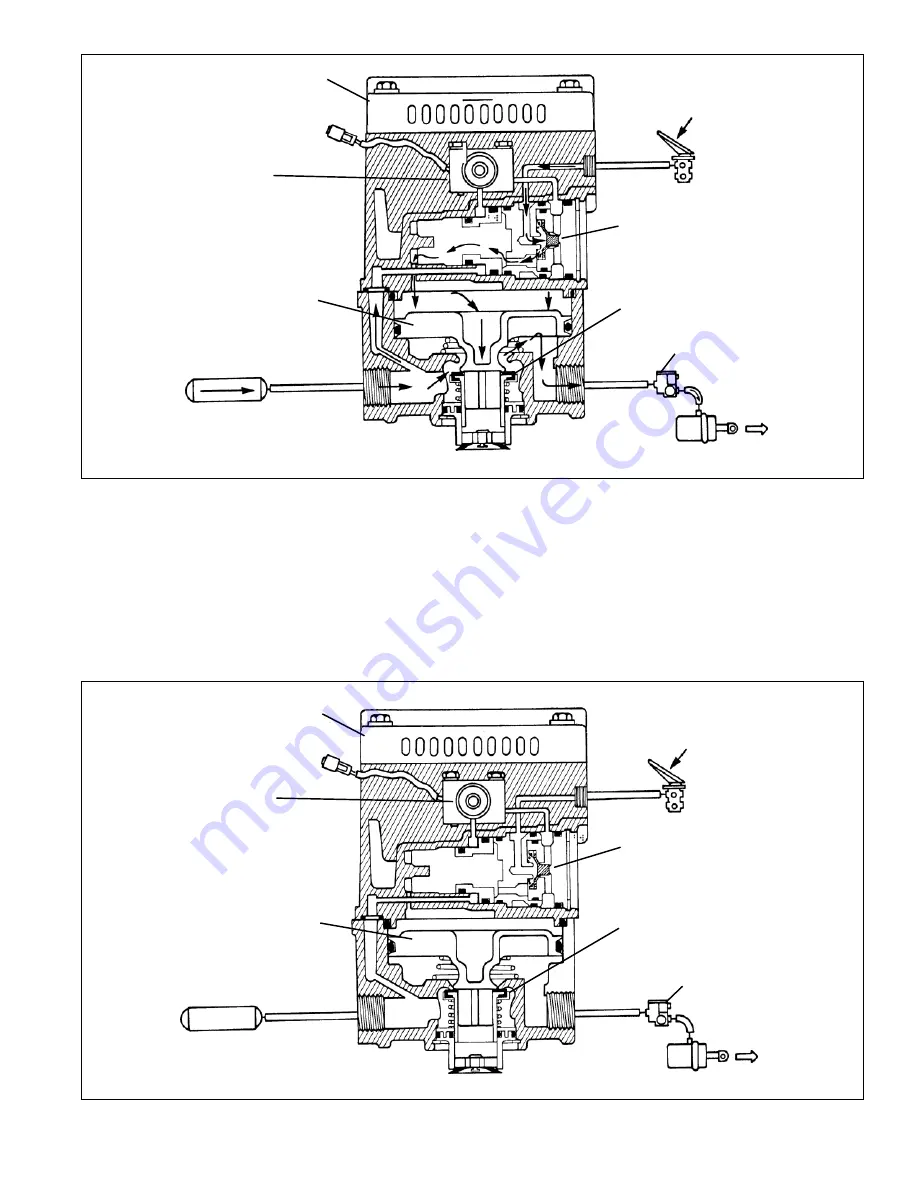
3
FIGURE 4 -
SERVICE BRAKE APPLICATION
FIGURE 5 -
SERVICE BRAKES HOLDING
SERVICE BRAKES HOLDING (FIGURE 5)
The air pressure being delivered to the brake chambers is
also present beneath the relay piston.
When the air pressure above and below relay piston is equal,
the piston moves slightly allowing the inlet valve to return to
its seat. The exhaust valve remains closed. With both the
inlet and exhaust valves closed, air pressure in the brake
chambers is held stable and neither increases nor decreases.
BRAKE
VALVE
SPRING BRAKE
REAR AXLE
RESERVOIR
RELAY PISTON
TRACTION
SOLENOID
MODULATOR
INLET EXHAUST
CHECK VALVE
CONTROLLER
BRAKE
VALVE
RELAY PISTON
TRACTION
SOLENOID
MODULATOR
INLET EXHAUST
CHECK VALVE
CONTROLLER
REAR AXLE
RESERVOIR
SPRING BRAKE
Summary of Contents for ATR-1 ANTILOCK TRACTION RELAY
Page 11: ...11 NOTES...