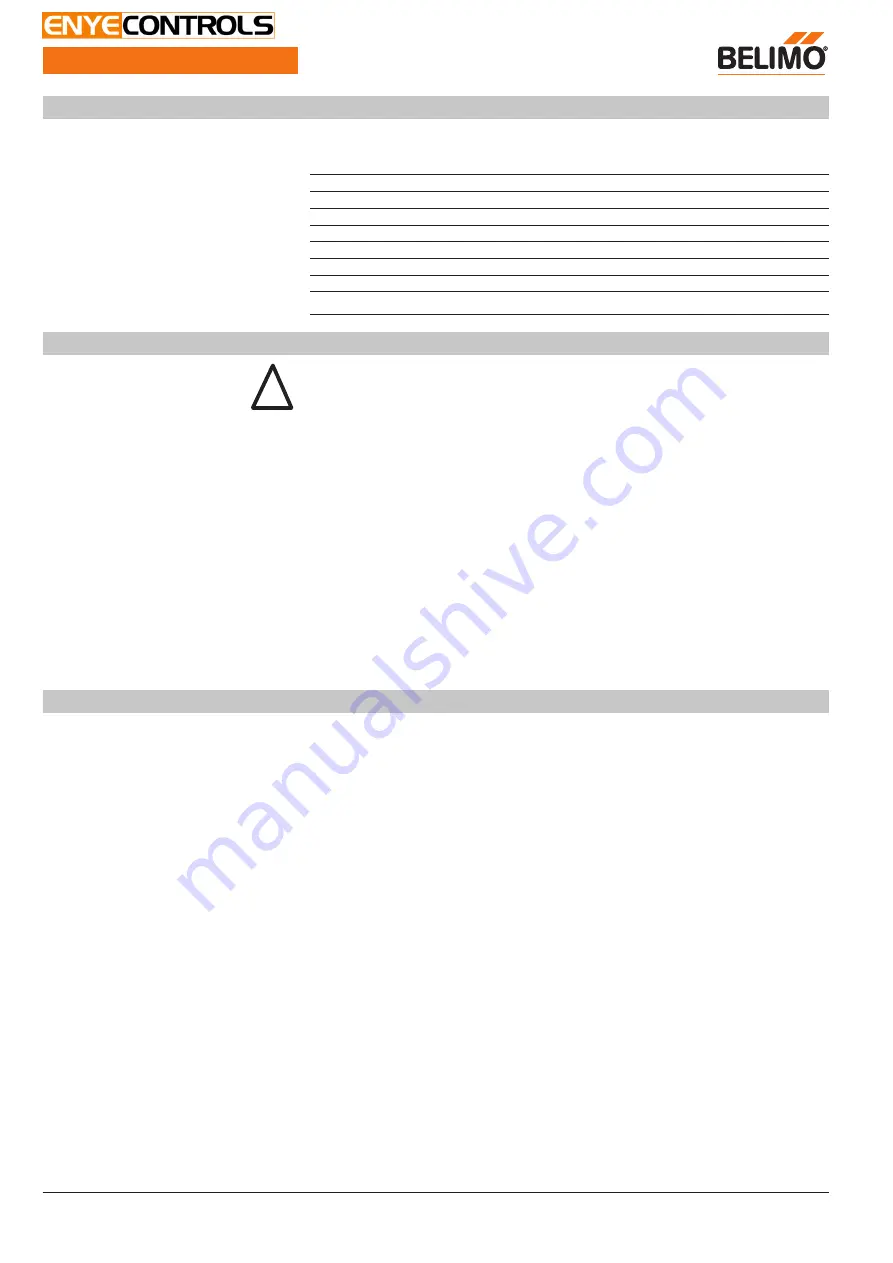
Safety Certification UL note
The UL marking on the actuator depends on the
production site, the device is UL-compliant in
any case
Mode of operation
Type 1
Rated impulse voltage supply / control
0.8 kV
Control pollution degree
3
Ambient temperature
0...50°C
Storage temperature
-40...80°C
Ambient humidity
Max. 95% r.H., non-condensing
Servicing
maintenance-free
Weight Weight
1.2 kg
Safety notes
!
• This device has been designed for use in stationary heating, ventilation and air-
conditioning systems and must not be used outside the specified field of application,
especially in aircraft or in any other airborne means of transport.
• Outdoor application: only possible in case that no (sea) water, snow, ice, insolation
or aggressive gases interfere directly with the actuator and that is ensured that the
ambient conditions remain at any time within the thresholds according to the data
sheet.
• Only authorised specialists may carry out installation. All applicable legal or
institutional installation regulations must be complied during installation.
• The switch for changing the direction of motion and so the closing point may be
adjusted only by authorised specialists. The direction of motion is critical, particularly
in connection with frost protection circuits.
• The device may only be opened at the manufacturer’s site. It does not contain any
parts that can be replaced or repaired by the user.
• The device contains electrical and electronic components and must not be disposed
of as household refuse. All locally valid regulations and requirements must be
observed.
Product features
Mode of operation
Conventional operation:
The actuator is connected with a standard modulating signal of 0...10 V and drives to
the position defined by the positioning signal. The measuring voltage U serves for the
electrical display of the actuator position 0.5...100% and as slave control signal for
other actuators.
Operation on Bus:
The actuator receives its digital positioning signal from the higher level controller via
the MP-Bus and drives to the position defined. Connection U serves as communication
interface and does not supply an analogue measuring voltage.
Converter for sensors
Connection option for a sensor (passive or active sensor or switching contact). The
MP actuator serves as an analogue/digital converter for the transmission of the sensor
signal via MP-Bus to the higher level system.
Parametrisable actuators
The factory settings cover the most common applications. Single parameters can be
modified with the Belimo Service Tools MFT-P or ZTH EU.
Simple direct mounting
Simple direct mounting on the globe valve by means of form-fit hollow clamping jaws.
The actuator can be rotated by 360° on the valve neck.
Manual override
Manual override with push-button possible (the gear is disengaged for as long as the
button is pressed or remains locked).
The stroke can be adjusted by using a hexagon socket screw key (4 mm), which is
inserted into the top of the actuator. The stroke shaft extends when the key is rotated
clockwise.
High functional reliability
The actuator is overload protected, requires no limit switches and automatically stops
when the end stop is reached.
Combination valve/actuator
Refer to the valve documentation for suitable valves, their permitted fluid temperatures
and closing pressures.
NV24A-MP-TPC
Globe valve actuator, modulating, communicative, AC/
DC 24 V, 1000 N
Technical data
NV24A-MP-TPC • en-gb • 2020-01-22 • subject to changes
2