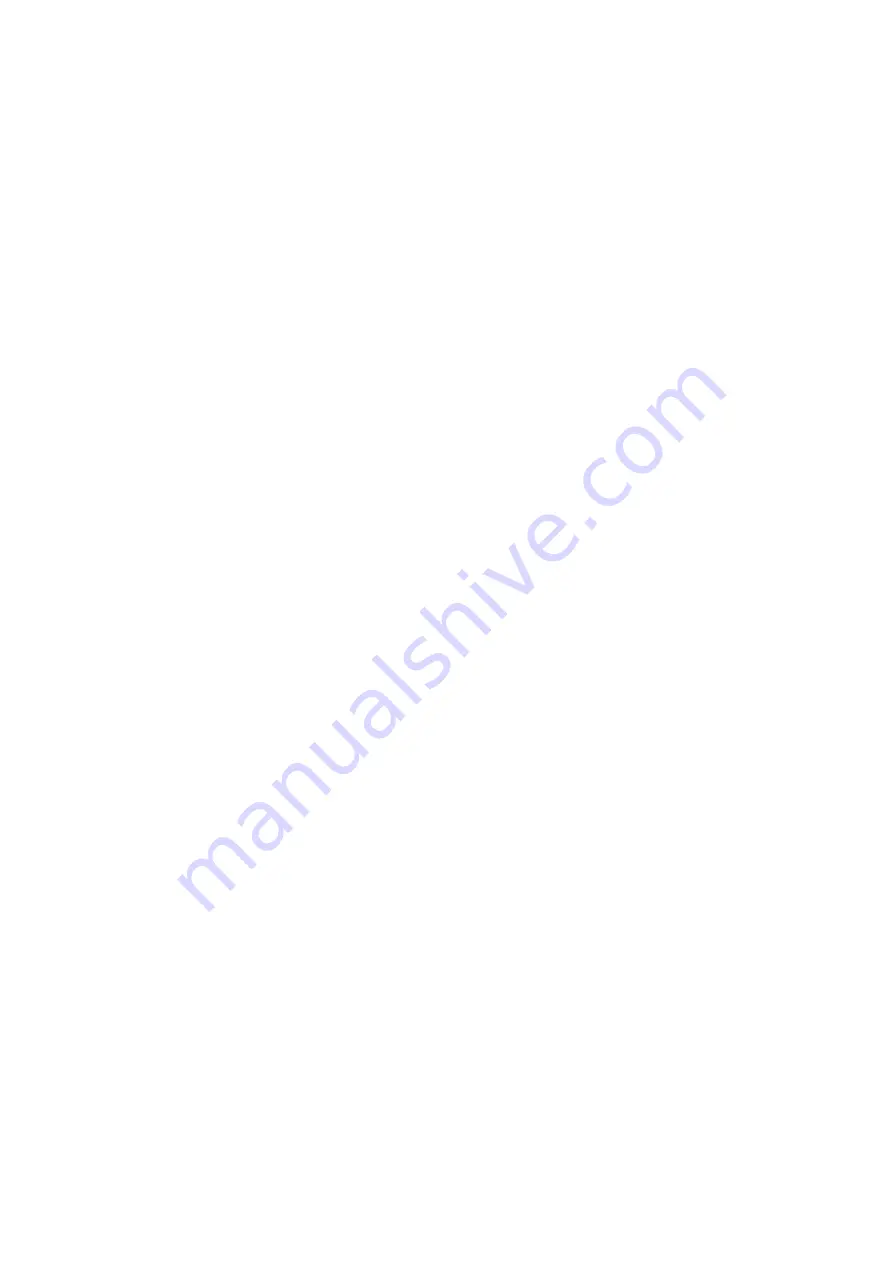
14
Step 5
Define function of P push-button
Select 'C--P' from the main menu and
press
P
to reveal the function of the
P
button in the display mode. Select
percentage 'PC' and return to the main
menu by pressing
E
Note: Because an input current display
in milliamps is not required, it is not
necessary to calibrate the two internal
references.
Step 6
Position dummy decimal point
Scroll though the main menu until 'd.P.'
is displayed and then press
P
. Using
the
Up
and
Down
push-buttons position
the dummy decimal point in front of the
least significant digit.
Press
E
to return to the main menu.
Step 7
Calibrate the display
Scroll through the main menu until
'CAL' is displayed. Press
P
and the
indicator will request a 4mA input by
displaying 'ZErO'. Set the input current
to 4.0000 ± 0.0004mA and press
P
again which will reveal the existing zero
display. Using the
Up
,
Down
and
P
push-buttons enter the required zero
display of -50.0 Press
E
to return to
the 'ZErO' prompt.
Press the
Up
push-button
and the
indicator will request a 20mA input by
displaying 'SPAn'. Set the input
current to 20.0000 ± 0.0004mA and
again press
P
which will reveal the
existing display at 20mA. Using the
Up
,
Down
and
P
push-buttons enter the
required display of 1050.0
Press
E
twice to return to the main
menu.
Step 8
Return to the display mode
Following completion of calibration
return to the display mode by pressing
'E
'.
7.2 Using the internal references
As in 7.1 the BA324D is required to display:
-50.0
with a 4mA input
1050.0
with a 20mA input
from a linear transducer. Maximum display
resolution is required, the frequency of the mains
supply is 50Hz and the existing security code is
1209. In the operating mode the indicator is
required to display the input current in milliamps
when the
P
push-button is operated.
This example assumes that the internal references
have been routinely calibrated.
Step1
Enter the programming mode
With an input current between 4 and
20mA put the indicator in the
programming mode by simultaneously
pressing
P
and
E.
The indicator will
respond by displaying 'COdE'. Press
P
to clear this prompt and set the display
to the security code 1209 using the
Up
,
Down
and
P
push-buttons. Pressing
E
will enter the code, and after a few
seconds during which the decimal
points will be scrolled, the first
parameter 'root' in the main menu will
be displayed.
Step 2
Square root extractor
With 'root' displayed, press
P
which
will reveal the root extractor status.
The root extractor can be turned on or
off by the
Up
or
Down
buttons. Select
'OFF', and press
E
to return to the main
menu.
Step 3 Select frequency of max mains (line)
rejection
Scroll though the main menu until
'Cond' is displayed. Enter the sub-
menu by pressing
P
twice
and select
the 'FrE' function. Using the
Up
or
Down
buttons select '50', and then
press
E
twice to return to the main
menu.
Step 4
Define function of
P
push-button
Select 'C--P' from the main menu and
press
P
to reveal the function of the
P
button in the display mode. Select '4-
20' and return to the main menu by
pressing
E
.
Step 5
Position dummy decimal point
Select 'd.P' from the main menu and
then press
P
. Using the
Up
and
Down
push-buttons position the dummy
decimal point in front of the least
significant digit.
Press
E
to return to the main menu.
Step 6
Calibrate display
With any input current between 4 and
20mA select 'SEt' from the main menu
and press
P.
The indicator will display
'ZErO' in the sub-menu; press
P
to
reveal the existing zero display.