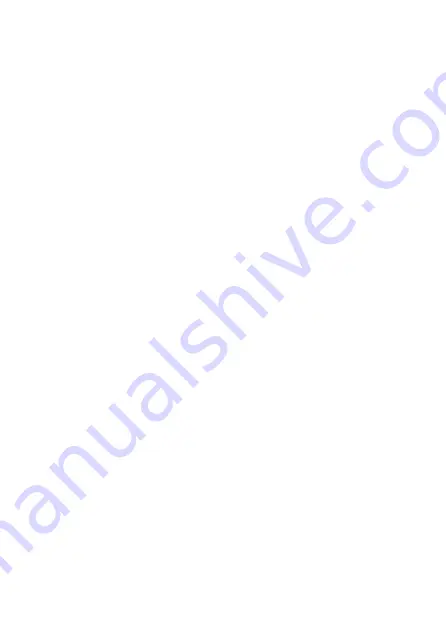
30
2.3 Welding process
•
Insert the paddle welding plate into the slot between the belts.
•
Slightly press the belt ends against the paddle welding plate.
•
Melt and weld the material for about 5-10 seconds, depending on the
profile thickness. The material has to be bubble free and spring up as a
3-4 mm wide bulge along the belt ends. The whole belt end must show
the bulge.
•
Slightly open the guiding clamp to remove the paddle welding plate.
•
Press the belt ends against each other quickly and tighten the lock
screw.
•
Cool down the belts inside of the guide clamp for 5-10 minutes.
•
Use the SE02 edge cutter to cut off or remove the bulge.
•
If necessary use a cotton cloth to remove adhering plastics from the
paddle welding plate. In no case use peaked or sharp-edged objects for
cleaning as the Teflon coating might be damaged.
•
The exact melting- and cooling times are depending on the belt profile
used as well as the environmental conditions. We suggest to practice
the welding process and to do testing in advance.
2.4 Recovery from error modes
•
If both of the LEDs are blinking (green or red), alternating or
simultaneously, the EErgo has entered one of the error modes.
•
It is possible to try to recover an error mode by pressing one of the
keys, according to desired working temperatur, TPE or PU.
•
In case of repeatedly entering an error mode, the number of the recov-
ery attempts is limited to four.
•
However, in case of an error mode, a user is advised to immediately
contact the service, since operating in an error mode can lead to over-
heating of the unit.