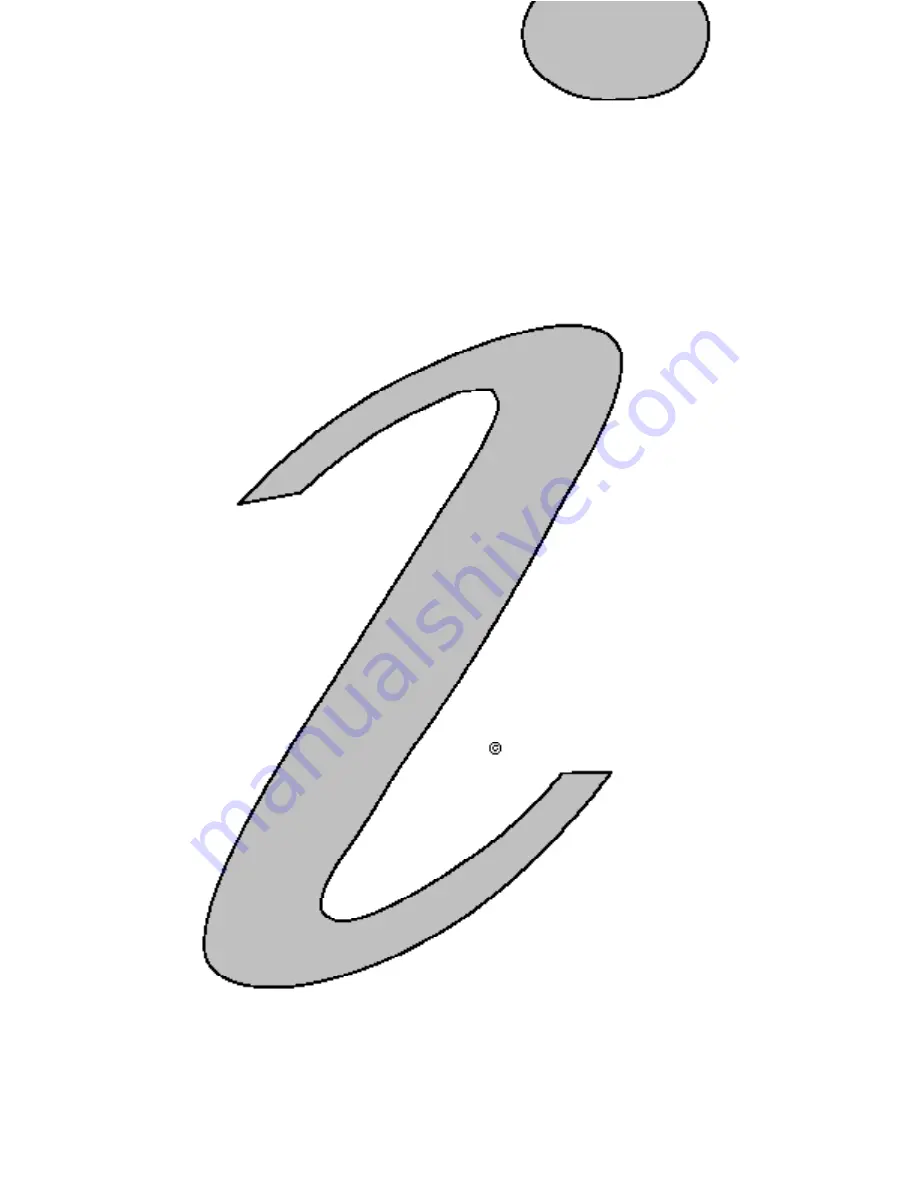
ATP
INDEX
COPYRIGHT 2003
COPYRIGHT IS NOT CLAIMED AS TO ANY PART OF AN ORIGINAL WORK
PREPARED BY A UNITED STATES GOVERNMENT OFFICER OR EMPLOYEE AS
PART OF THAT PERSONS OFFICIAL DUTIES OR BY ANY OTHER THIRD PARTY
OFFICER OR EMPLOYEE AS PART OF THAT PERSONS DUTIES.
"ATP" is a registered trademark of Aircraft Technical Publishers. All original
authorship of ATP is protected under U.S. and foreign copyrights and is subject
to written license agreements between ATP and its Subscribers.
ALL RIGHTS RESERVED. NO PART OF THIS PUBLICATION MAY BE
REPRODUCED, STORED IN A RETRIEVAL SYSTEM, OR TRANSMITTED IN ANY
FORM BY ANY MEANS, ELECTRONIC, MECHANICAL, PHOTOCOPYING,
RECORDING OR OTHERWISE, WITHOUT PRIOR WRITTEN PERMISSION OF THE
PUBLISHER.
Summary of Contents for Bonanza 33 Series
Page 7: ...33 SERIES SHOP IVIANUAL ...
Page 14: ...SECTION INTRODUCTION ...
Page 15: ...r SECTION 1 Introduction ...
Page 30: ...SECTION GENERAL INFORMATION ...
Page 31: ...trl SECTION 2 General Information ...
Page 60: ...SECTION SYSTEMS DESCRIPTION AND NIAINTENANCE ...
Page 61: ...IE SECTION 3 System Description and Maintenance ...
Page 143: ...SECTION NIAJOR DISASSEIVIBLY ...
Page 144: ...C SECTION Major Disassembly ...
Page 177: ...SECTION NIAJ O R NIAINTENANCE AND OVERHAUL ...
Page 178: ...IF SECTION 5 Major Maintenance and Overhaul ...
Page 181: ...SECTION ELECTRICAL VVIRING DIRAGRAIVIS ...
Page 182: ...SECTION 6 Electrical Wiring Diagrams ...
Page 314: ...33 590011 10 12 BLANK PAGE Issued September 1971 6 78A ...
Page 321: ...SECTION R E P LACEIVI E NT SCHEDULE ...
Page 322: ...SECTION 7 II Replacement Schedule ...
Page 329: ...SECTION PERIODIC INSPECTIONS ...
Page 330: ...SECTION 8 Periodic Inspections ...
Page 348: ...35 SERIES SHOP NIANUAL ...
Page 364: ...SECTION INTRODUCTION ...
Page 365: ...Il SECTION 1 Introduction ...
Page 387: ...SECTION GENERAL IN FORNIATION SERVICING ...
Page 388: ...SECTION 2 General Information Servicing ...
Page 428: ...SECTION SYSTEM DESCRIPTION AND NIAINTENANCE ...
Page 429: ...6 SECTION 3 System Description and Maintenance ...
Page 573: ...SECTION IVIAJ O R DISASSEMBLY ...
Page 574: ...L SECTION 4 Major Disassembly ...
Page 629: ...SECTION NIAJ OR MAINTENANCE AND OVERHAUL ...
Page 630: ...SECTION 5 Major Maintenance and Overhaul ...
Page 650: ...SECTION ELECTRICAL VVIRING DIRAGRANIS ...
Page 651: ...SE TION 6 I Electrical Wiring Diagrams ...
Page 808: ...SECTION PERIODIC INSPECTION SCHEDULE ...
Page 809: ...SECTION 7 Periodic Inspection Schedule I ...
Page 840: ...SECTION ACCESSORY AND CO NIPONENT REPLACEMENT SCHEDULE ...
Page 841: ...SECTION 8 Accessory and Component Replacement Schedule I ...