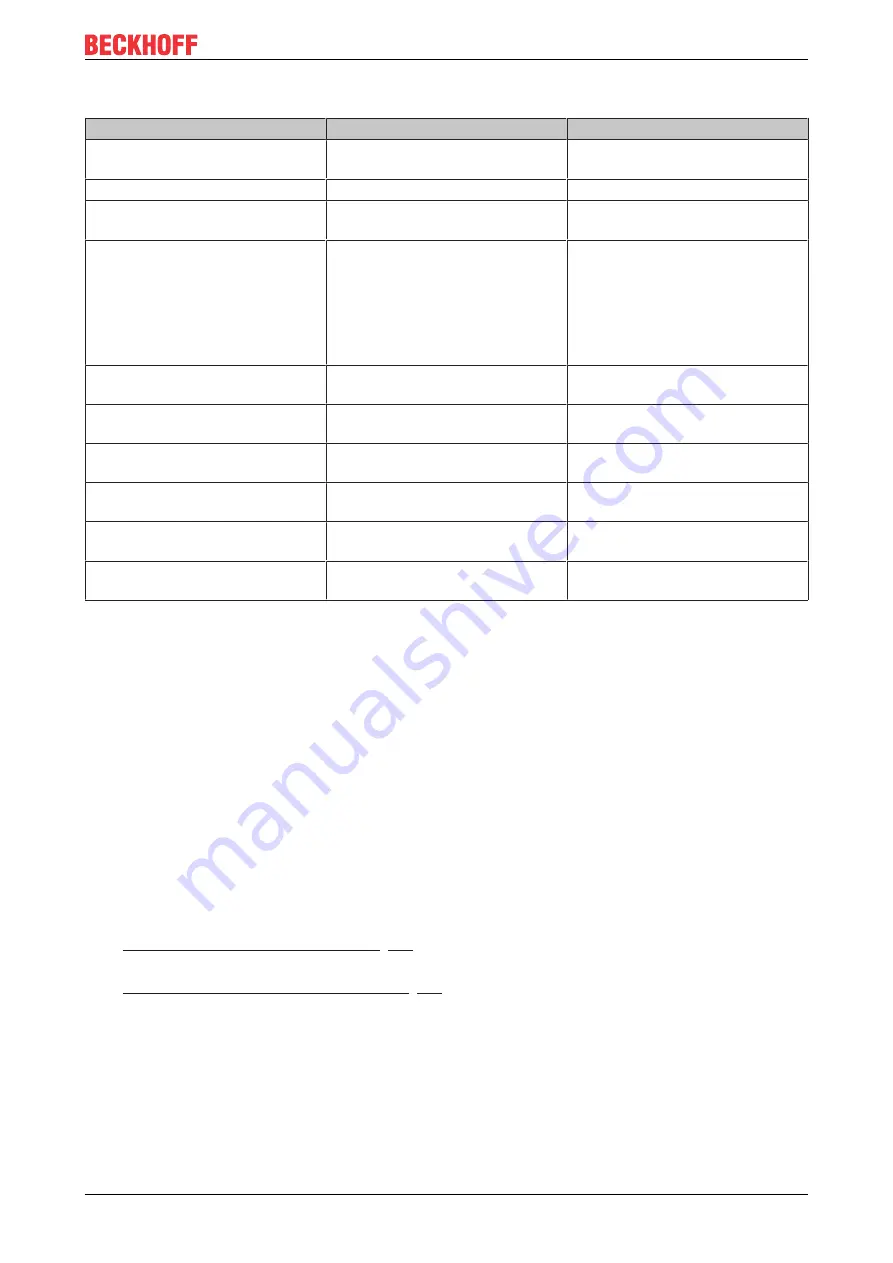
Configuration
TF6120
33
Version: 1.1
Conversion-Parameters
Type
Req./Opt.
Description
ConversionID
Req
unique ID-number which identifies
this conversion
ConversionDesc
Optional
ConversionType
Req
0 : NoConversion
1 : LinearConversion
Clamping
Optional
0 : No clamping 1 : Clamp on EU
2 : Clamp as specifiedIf clamping is
active, the data value will be limited
to its High clamp/EU value, when it
exceeds the upper limit, and
similarly with Low clamp
parameter.
HighClamp
Optional, depends on
<ConversionType>/<Clamping>
1.0 (Default)
LowClamp
Optional, depends on
<ConversionType>/<Clamping>
0.0 (Default)
HighEU
Optional, depends on
<ConversionType>/<Clamping>
engineering unit (client scale) 1.0
(Default)
LowEU
Optional, depends on
<ConversionType>/<Clamping>
engineering unit (client scale) 0.0
(Default)
HighIR
Optional, depends on
<ConversionType>/<Clamping>
instrument range (device scale)
10000 (Default)
LowIR
Optional, depends on
<ConversionType>/<Clamping>
instrument range (device scale) 0
(Default)
4.1.3
Data Access
4.1.3.1
Overview
An OPC server represents a standardised interface for the management of process data. The process data
available in the TwinCAT system must therefore be known to the OPC server, or must be made known to it
at the time of configuration. To represent this "hierarchical process space" clearly, the "Devices" are
subdivided into subsidiary items. The OPC client can browse through this representation and use it for the
server's actual configuration. The TwinCAT OPC server supports the optional browser OPC interface.
Please note:
This hierarchical display is not to be confused with the configuration of the OPC server that
exists at run-time. The run-time configuration of the OPC server, i.e. the creation of groups, specification of
the refresh time, the insertion of tags etc. is performed dynamically by the OPC client.
Configuration TwinCAT OPC Server
•
Receiving data from the TwinCAT PLC [
: Configuration by variable import from TwinCAT PLC
control
•
Receiving Data from the TwinCAT I/O task [
: Configuration by variable upload from the TwinCAT
I/O Task
4.1.3.2
Receiving data from TwinCAT PLC
As mentioned bfore, the OPC-Server gives the possibility to read/write process values from ADS devices and
therefore also from the TwinCAT PLC.
Summary of Contents for TF6120
Page 1: ...Manual EN TF6120 TwinCAT 3 OPC DA 2022 02 28 Version 1 1 ...
Page 2: ......
Page 4: ...Table of contents TF6120 4 Version 1 1 ...
Page 74: ...Appendix TF6120 74 Version 1 1 ...
Page 75: ......