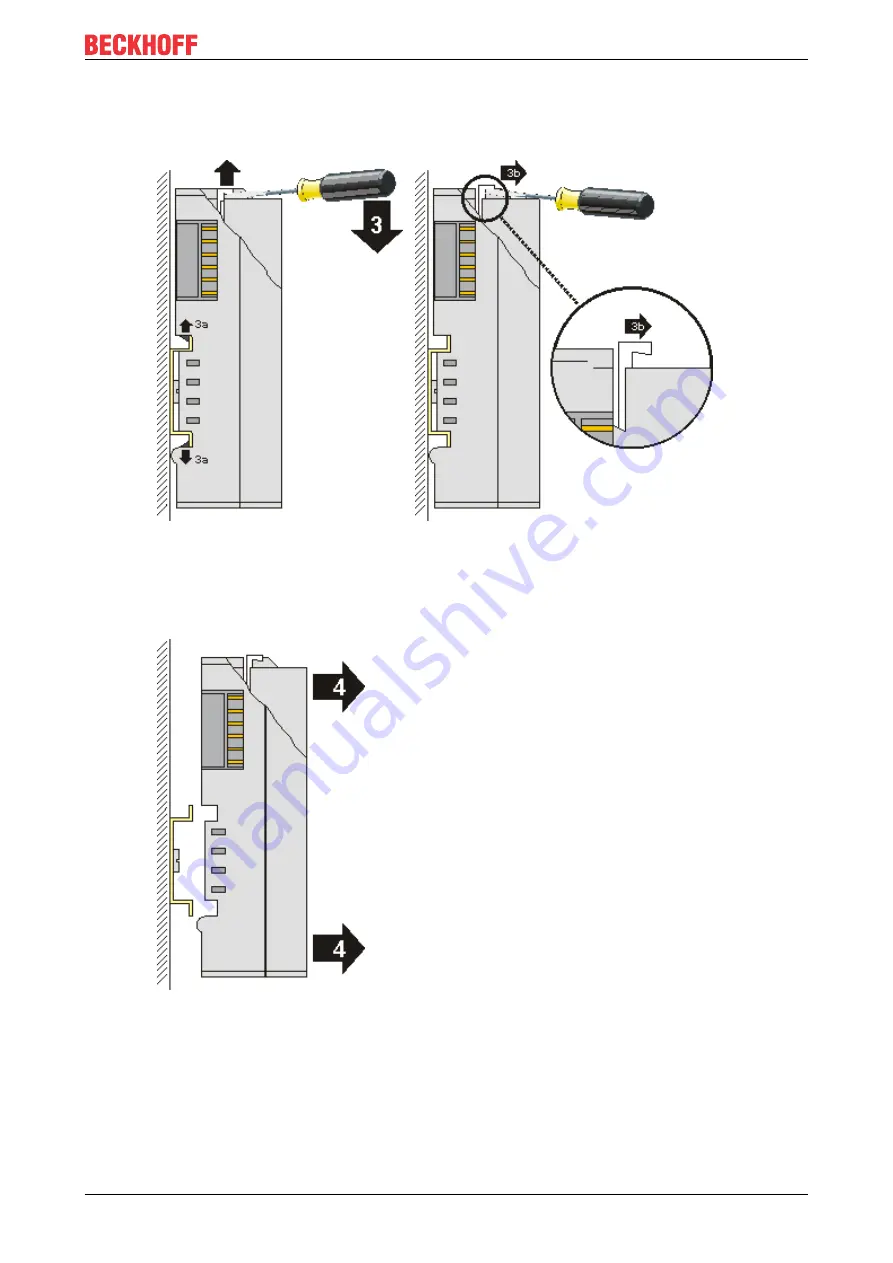
Mounting and wiring
KM2774
11
Version: 2.0.0
◦ an internal mechanism pulls the two latching lugs (3a) from the top hat rail back into the terminal
module,
◦ the unlatching hook moves forwards (3b) and engages
• In the case 32 and 64 channel terminal modules (KMxxx4 and KMxxx8 or EMxxx4 and EMxxx8) you
now lever the second unlatching hook on the right-hand side of the terminal module upwards in the
same way.
• Pull (4) the terminal module away from the mounting surface.
3.2
Recommended mounting rails
Terminal Modules und EtherCAT Modules of KMxxxx and EMxxxx series, same as the terminals of the
EL66xx and EL67xx series can be snapped onto the following recommended mounting rails:
• DIN Rail TH 35-7.5 with 1 mm material thickness (according to EN 60715)
• DIN Rail TH 35-15 with 1,5 mm material thickness