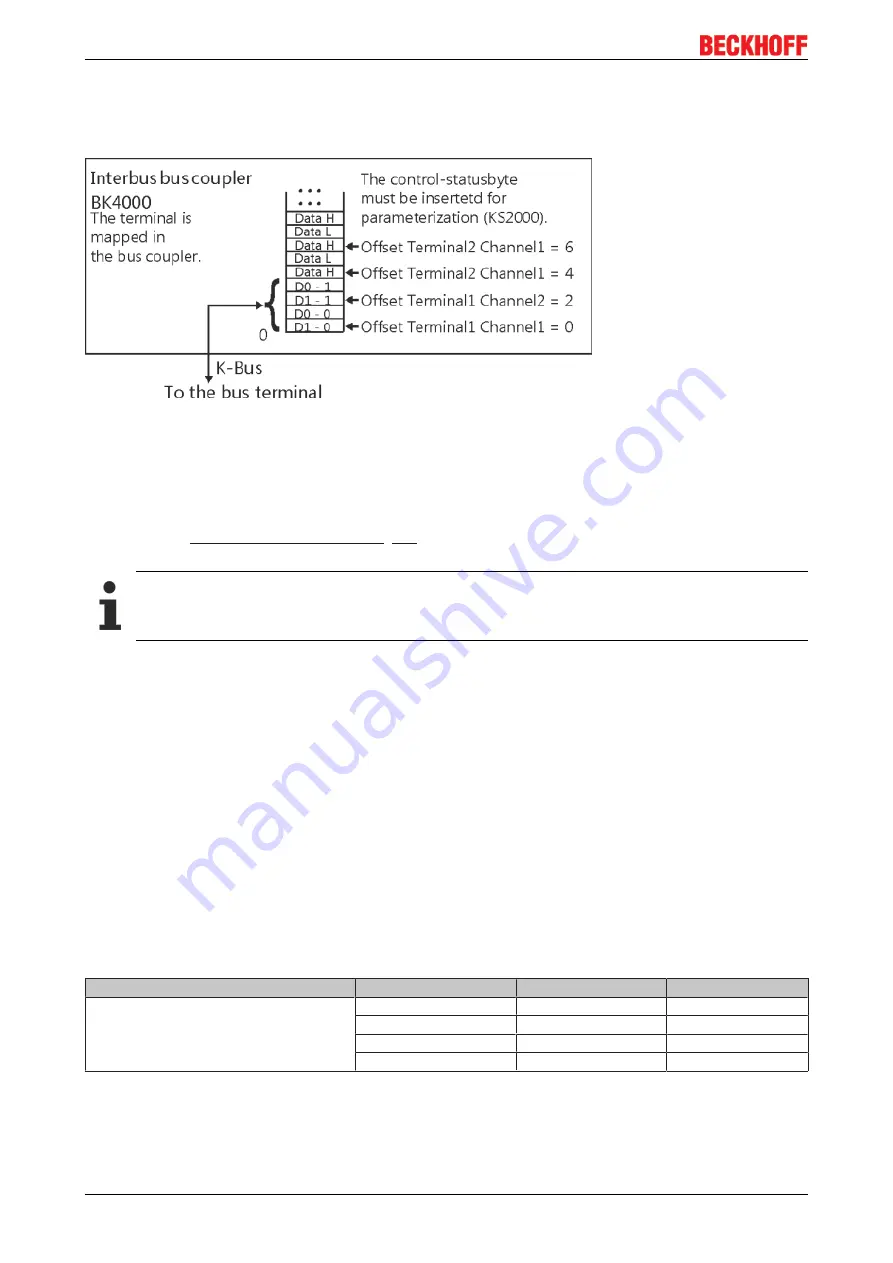
Access from the user program
KL301x, KL302x
32
Version: 4.1
• KL3012 and KL3022: 4 bytes of input data
Parameterization via the fieldbus is not possible. If the control and status byte is to be used, the KS2000
configuration software is required.
Fig. 20: Mapping in the Interbus coupler – example for KL3012 and KL3022
Other Bus Couplers and further information
Further information about the mapping configuration of Bus Couplers can be found in the Appendix of the
respective Bus Coupler manual under
Master configuration
.
contains an overview of possible mapping
configurations, depending on the configurable parameters.
Parameterization with KS2000
The KS2000 configuration software can be used for parameterizations via the serial interface of the
Bus Coupler, independent of the fieldbus system.
5.2
Mapping in the Bus Coupler
As already described in the
Terminal Configuration
section, each Bus Terminal is mapped in the Bus
Coupler. This mapping is usually done with the default setting in the Bus Coupler / Bus Terminal. The
KS2000 configuration software or a master configuration software (e.g. ComProfibus or TwinCAT System
Manager) can be used to change this default setting.
If the terminals are fully evaluated, they occupy memory space in the input and output process image.
The following tables provide information about how the terminals map themselves in the Bus Coupler,
depending on the parameters set.
5.2.1
KL3011 and KL3021
Default mapping for: CANopen, CANCAL, DeviceNet, ControlNet, Modbus, RS232 and RS485 coupler
Conditions
Word offset
High byte
Low byte
Complete evaluation: no
Motorola format: no
Word alignment: any
0
Ch1 D1
Ch1 D0
1
-
-
2
-
-
3
-
-
Summary of Contents for KL301 Series
Page 2: ......