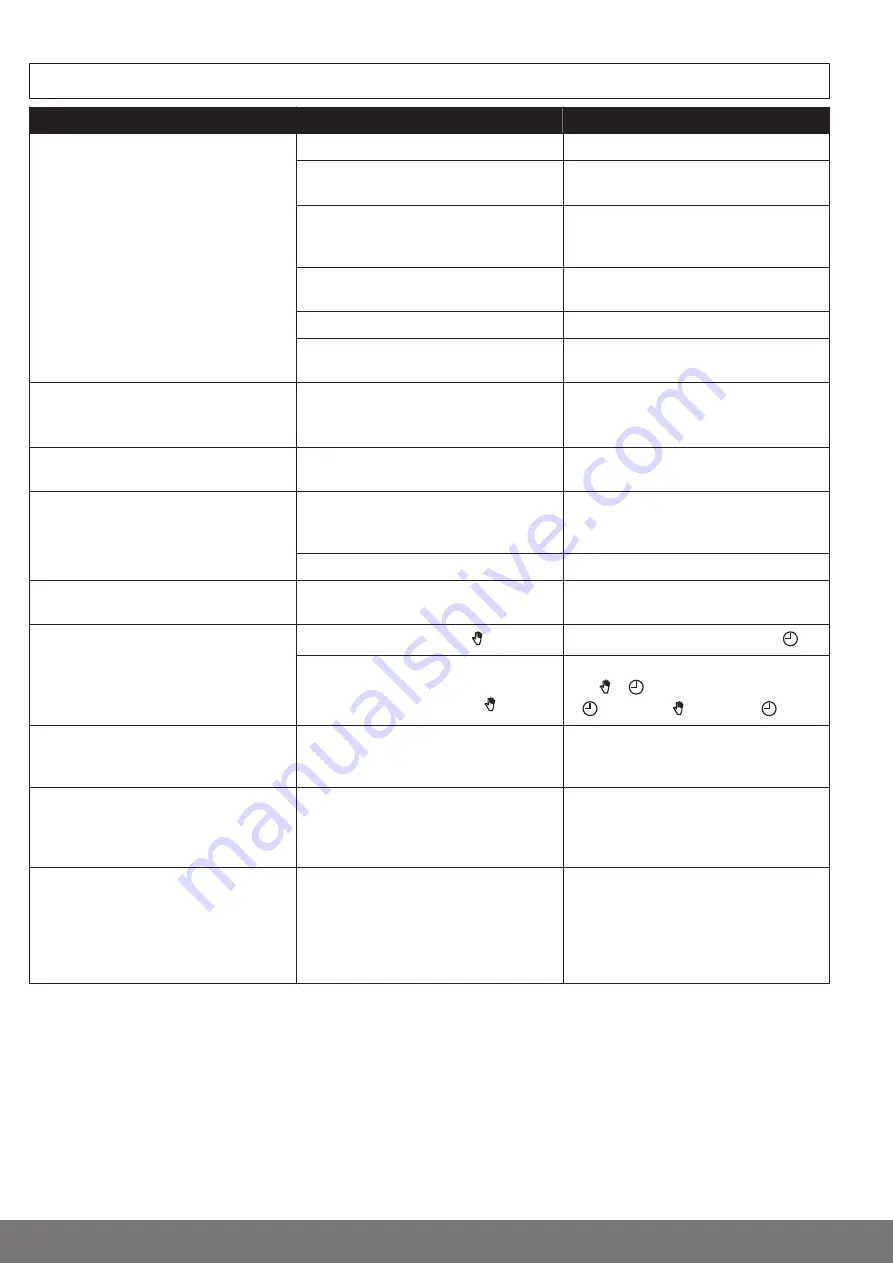
What to do if...?
Problem
Cause
Remedy
Tubular drive is not functioning.
No transmitter programmed.
Programme new transmitter.
Transmitter is out of range of the tubular
drive.
Bring transmitter within range of the tubu‐
lar drive.
Transmitter was operated out of range
several times.
Press drive or stop button on transmitter
at least 5 times in the immediate vicinity
of the tubular drive.
Batteries in transmitter not inserted/ in‐
serted incorrectly or dead.
Insert batteries correctly or insert new
batteries.
Electrical connection is faulty.
Check electrical connection.
Thermal protection switch in tubular drive
has tripped.
Wait until the thermal protection switch in
the tubular drive is reactivated.
Shutter direction on tubular drive cannot
be set.
Limit positions are stored in the tubular
drive.
Delete limit positions (see
) and reset the direc‐
tion switch.
Incorrect shutter direction after deleting
limit positions.
Direction switch is in the wrong position.
Switch the direction switch to the oppo‐
site position.
Tubular drive stops arbitrarily; cannot be
restarted in the same direction.
Tubular drive has detected an increase in
load.
Briefly run the curtain in the opposite di‐
rection, then continue in the desired di‐
rection.
Tubular drive is overloaded.
Use a higher-torque tubular drive.
Switching times cannot be set on tubular
drive.
Programmed transmitter has no manual/
auto slide switch.
Use transmitter with manual/auto slide
switch.
Tubular drive does not operate at the set
switching time.
Manual/auto slide switch at .
Switch manual/auto slide switch to .
More than one slide switch transmitter is
programmed on the tubular drive. One
manual/auto slide switch is at .
Switch the slide switch on one transmitter
from to . If the slide switch is already
at , switch it to and back to .
Set switching times change.
Frequent 230 V AC power cuts.
Fluctuations in the 50 Hz mains frequen‐
cy.
During the programming run, the drive
stops short of the limit position to be pro‐
grammed.
For safety reasons, the drive reacts sensi‐
tively to unsmooth running during the
programming run, in order to prevent
damage.
Briefly run curtain DOWN and subse‐
quently UP until you reach the upper limit
position.
Ventilation slots of the roller shutter do
not close fully.
Unsmooth running of the roller shutter
near the lower stop and setting of the
“lower stop” limit position.
Delete the limit positions (see
) and set the limit po‐
sitions as per "to lower point" (Setting the
limit positions); to this end, first pro‐
gramme the lower limit position (lower
point) and then the upper limit position.
22
Summary of Contents for R12/17C
Page 23: ...Sample wiring diagram N L PE Electronics Black Brown Blue Green yellow 23...
Page 24: ...Declaration of conformity 24...
Page 25: ...25...
Page 26: ...26...
Page 27: ...27...
Page 28: ...2010 300 570 0a 06 03 2013...