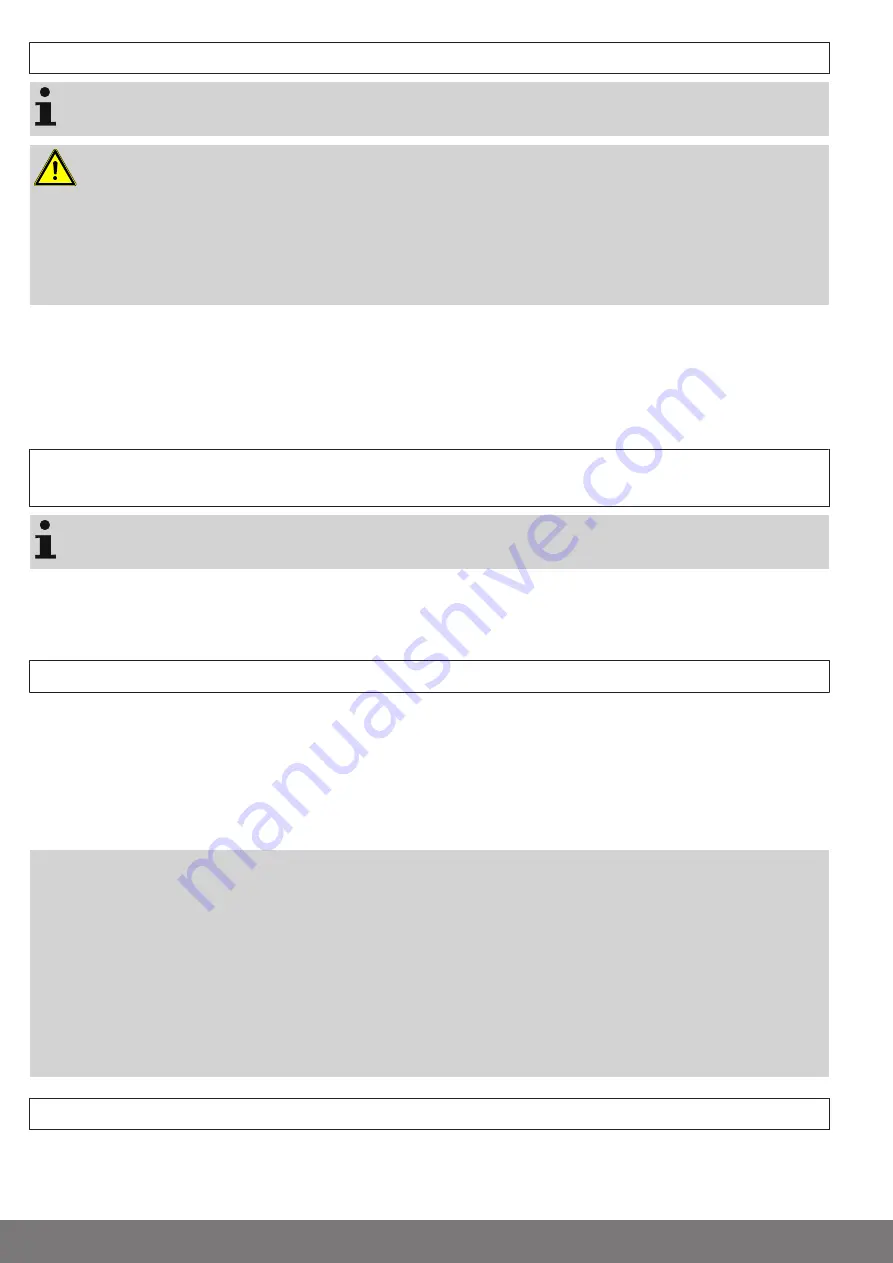
Obstacle detection (for vertical sun protection applications with heavy end strip)
The functions and presettings of the model versions are different. Please find further in-
formation in the "Version summary" chapter.
Caution
Obstacle detection is only active in conjunction with the "drive adapter for obstacle detec-
tion".
In addition, please note that the drive must be pushed in to the shaft as far as the band of
the thrust ring.
Use of the drive’s obstacle detection system as personal protection is not permitted. It has
been designed exclusively to protect the sun protection system from being damaged.
If the drive is correctly installed, it switches off when it detects obstructions or fabric faults and tries to run past the obstruction a
second time. If this fails, the drive switches off after the third attempt. Approx. 360° from the lower limit position, the drive interrupts
operation immediately following the first detection of an obstacle and makes no further attempt to continue.
The total number of attempts to complete a travel that has been started to the respective limit position is limited to 10 (distributed
over several obstruction locations).
If reversing is interrupted, a further drive command is only possible in the direction of reversing. Move the fabric without interrup-
tion until the tubular drive stops automatically. It is now possible to travel in both directions again.
Activating/deactivating the additional fabric untensioning function with the
programming unit
The functions and presettings of the model versions are different. Please find further in-
formation in the "Version summary" chapter.
On delivery, the fabric untensioning function is deactivated. To activate it, move to the upper limit position. Press the programming
button for approx. 5 seconds. The drive moves a short distance out of the limit position and back again. The fabric untensioning
function is now active.
Repeat the procedure to deactivate it.
Information for the electrician
Tubular drives with electronic limit switching can be connected in parallel. The maximum switching contact load of the switching
equipment (timer, relay control, switch, etc.) must be observed. To operate drives with electronic limit switching, only use switch-
ing elements (timers) that are
not
earthed via the drive. The outputs of the switching element must be potential-free in the neutral
position.
Use external conductor L1 to control the up and down direction. Other devices or consumers (lamps, relays, etc.) must not be dir-
ectly connected to the drive connecting cables. For this purpose, the drives and additional devices must be decoupled by relay
controls.
When installing the drive, all-pole disconnection from the mains with a contact gap of at least 3 mm per pole must be provided.
Attention
Only use mechanically or electrically locked switching elements with a marked zero posi-
tion! This also applies when drives with electronic and mechanical limit switching are used
in the same system. The changeover time for switching the running direction must be at
least 0.5 s. The switch and control must not execute simultaneous UP and DOWN com-
mands. Protect the electrical connections from damp.
Once you have finished wiring everything to the control, ALWAYS check the right direction
assignment of the drive to the control buttons UP and DOWN, EXTEND and RETRACT.
If the drive is to be operated with devices which contain sources of interference, the elec-
trician must ensure suitable interference suppression for the relevant devices.
Disposal
This product is made of various materials which must be disposed of properly. Find out about the applicable regulations on recyc-
ling or disposal for this product in your country.
The packaging material must be disposed of properly.
16
Summary of Contents for E16-V1
Page 20: ...Declaration of conformity 20 ...
Page 21: ...21 ...
Page 22: ...22 ...
Page 23: ...23 ...
Page 24: ......