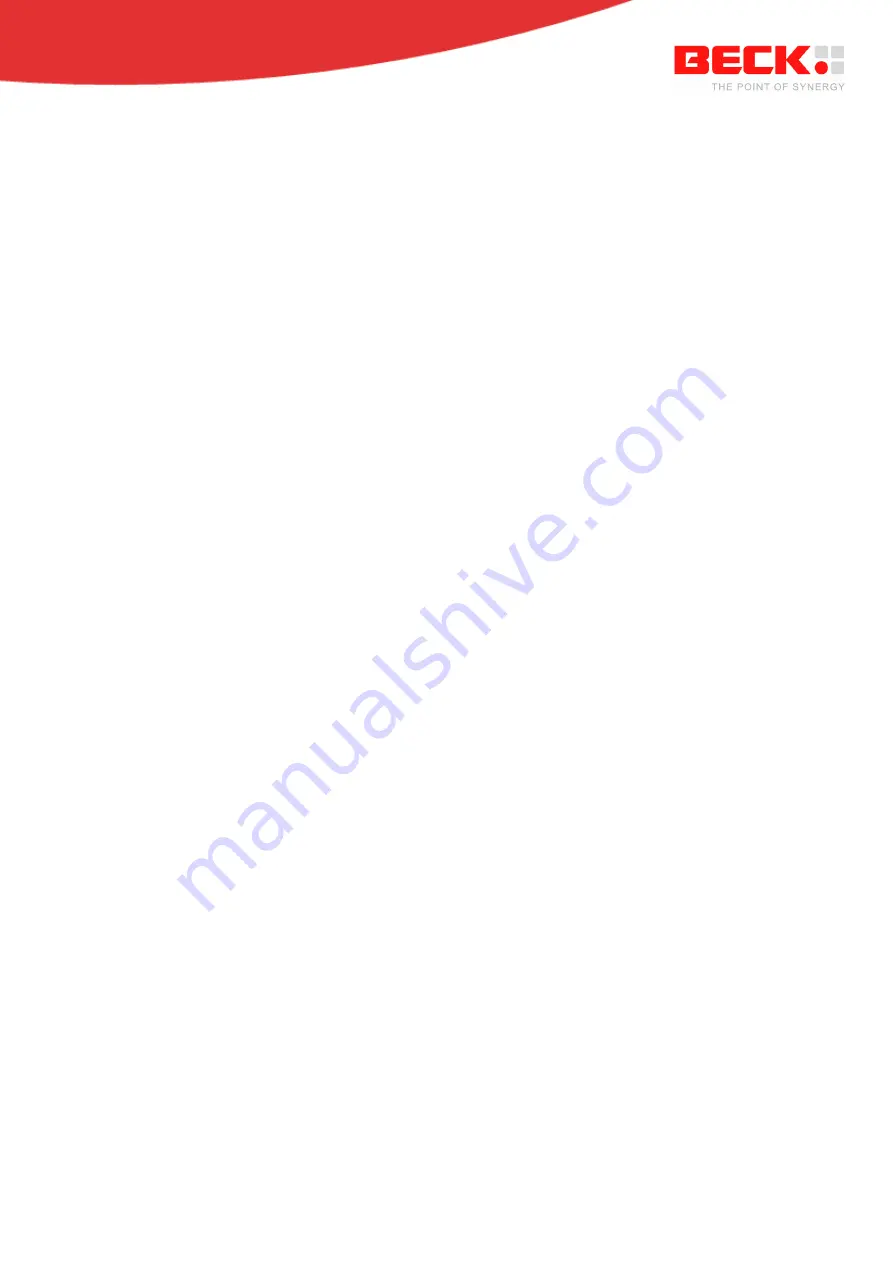
AN_SC1x3_Design_Guide_V10.PDF
© Beck IPC GmbH
E-Mail: [email protected]
www.beck-ipc.com
A member of the Festo group
Beck IPC GmbH
Grüninger Weg 24
35415 Pohlheim-Garbenteich
Start-up / Troubleshooting of new SC1x3-Designs
Step 1.
Check input current of your design. The current of the SC1x3 should not
exceed 0.6A. Hint: Most electronic parts work only so long as the smoke is
still inside
Æ
If the smoke is out, they are defect.
Step 2.
Connect a serial cable to COM1 and check the boot message.
Problem:
No bootmessage comes out. Input current is very low.
Solution:
Check crystal frequency. The frequency should have 25MHz. If lower
frequency than 25MHz, check route of XIN and XOUT to CPULCK.
Check UCSIN#/UCSOUT# with an oscilloscope. After power on you should
see the signals toggling. This indicates the reading of the RTOS from the
internal flash. Check CPUCLK. At the begin of the boot process it should
have 24MHz, then the RTOS sets the frequency to 96MHz by default. If
reading from internal flash fails, the freuency of CPUCLK remains at 24MHz.
Check RESETOUT#. If it is low the SC1x3 is in reset state. If RESETOUT# is
shortened with GND, the SC1x3 is in reset state too.
Step 3.
Problem:
Bootmessage prints RAM ERROR.
Periphery connected to address-/databus is not working
Solution:
Check the periphery connected to the address-/databus. If to many parts are
connected to the buses of the SC1x3, it will prevent it from booting. All
signals from the external address-/databus are used internal too. If the
external load is to heavy or the routing too long, the internal RAM test will fail
and it won’t boot.
Check the chip selects and other control signals. Is the right configuration
used for Chip Select Byte Enable through A12 ?
Step 4.
Problem:
System reboots when USB driver gets started.
Solution:
Check the INT3 input of the SC1x3. The USB driver enables external INT3,
because INT3 is shared with internal USB. If the input is high or floating the
system can get too much interrupts.
30.10.2007 M.Nesseldreher