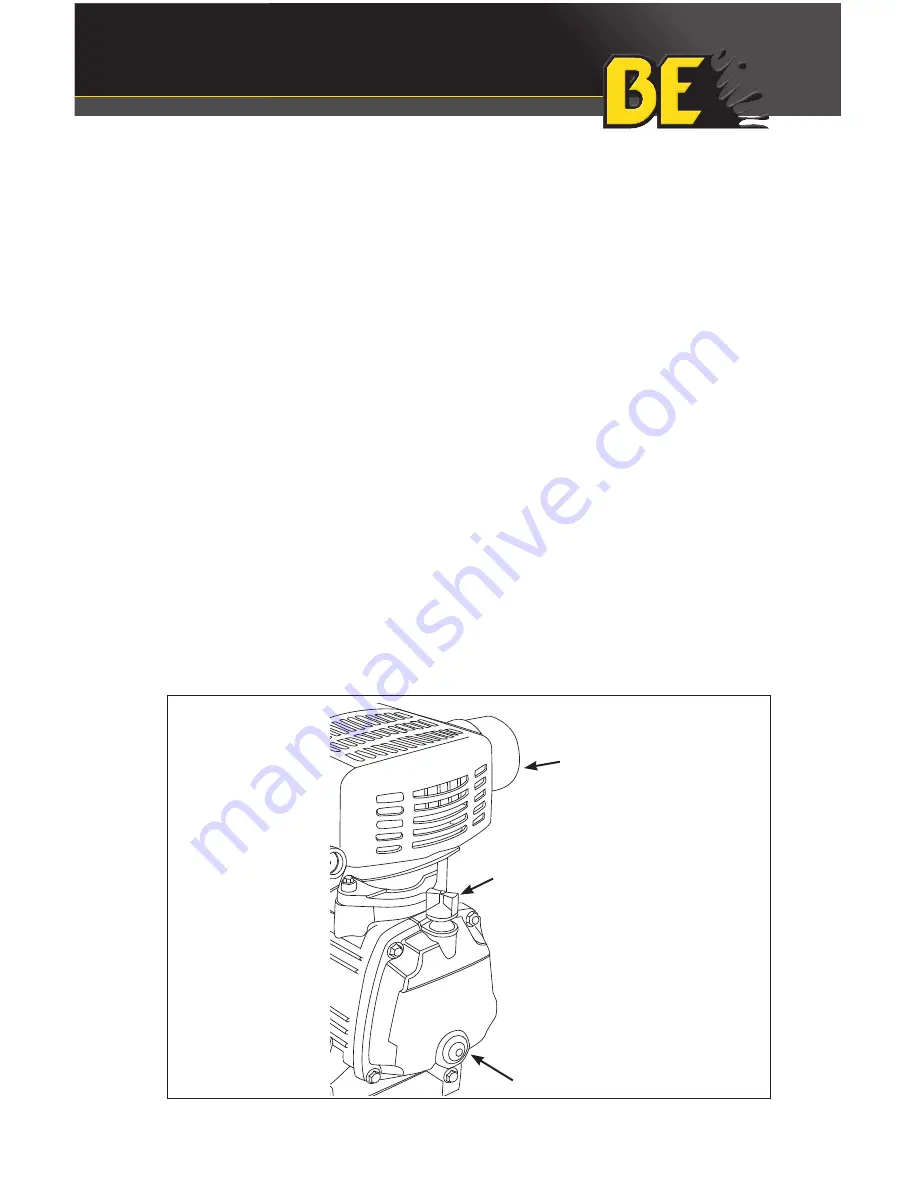
19
maintenance
caution
Caution
Monthly
·· Inspect for air leaks. Squirt soapy water around joints during compressor
operation and watch for bubbles. Tighten fittings if necessary.
·· Clean exterior.
3 months or 120 hours
·· Change petroleum lubricant in pump while crankcase is warm.
12 months or 1000 hours
·· Replace air filter element.
1. Put the cover off first and put on the breath pipe and air filter before the
compressor run (Fig.5).
2. Never unscrew any connecting part when the tank is in pressure condition.
3. Never disassemble any electrical part before disconnecting the plug.
4. Never adjust the safety valve carelessly.
5. Never use the compressor in place where voltage is too low or too high.
6. Never disconnect the plug to stop compressor, set the switch knob in
position off instead.
7. If the release valve doesn’t work as motor stopped, find the cause immedi-
ately so as not to damage motor.
8. Lubricating oil must be clean, oil level should be kept in the score of oil ruler.
9. Disconnect the plug to cut off power supply and open the outlet valve.
FIG. 5
OIL LENS
RESPIRATOR
AIR FILTER
Summary of Contents for AC153
Page 20: ...20 exploded view...