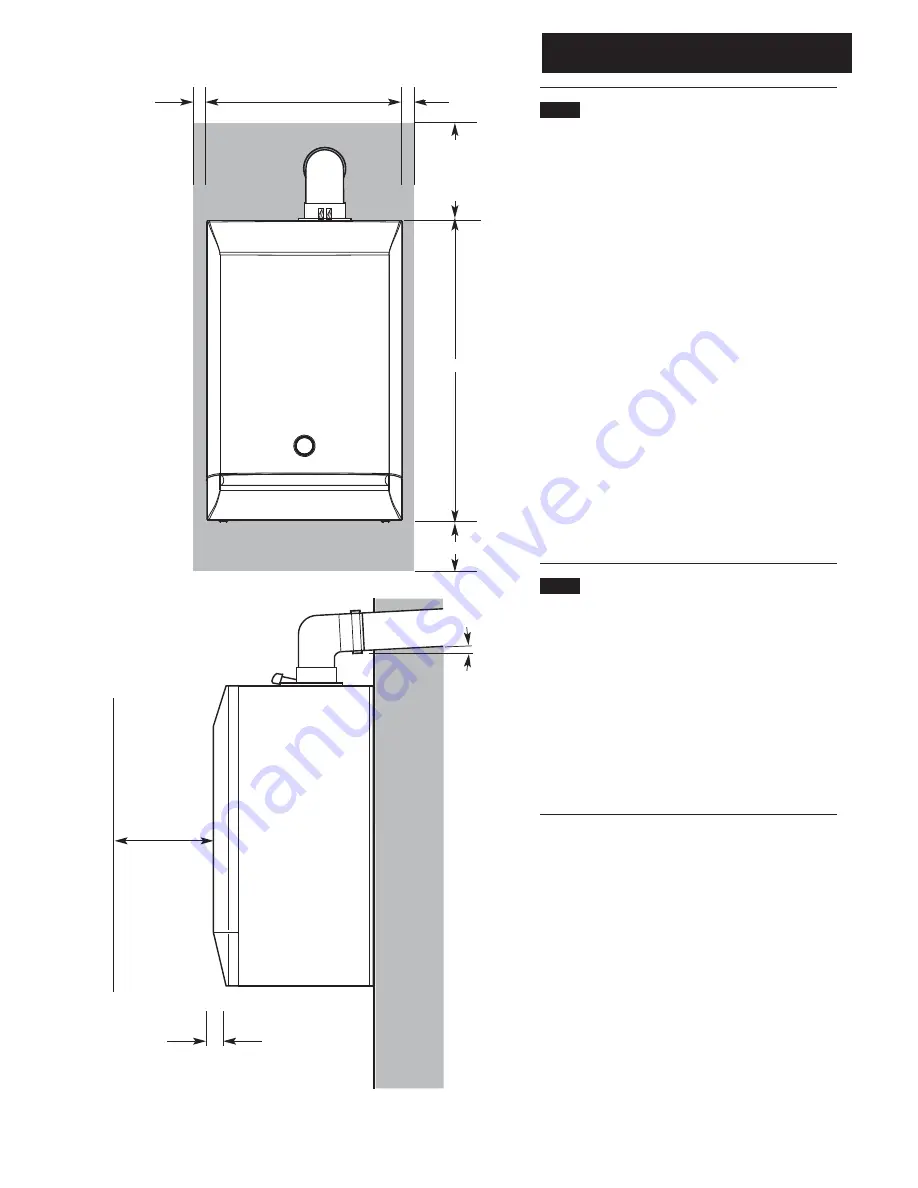
14
7.0 Site Requirements
© Baxi Heating UK Ltd 2013
7.1
Location
1. The boiler may be fitted to any suitable wall with the flue
passing through an outside wall or roof and discharging to
atmosphere in a position permitting satisfactory removal of
combustion products and providing an adequate air supply.
The boiler should be fitted within the building unless
otherwise protected by a suitable enclosure i.e. garage or
outhouse. (The boiler may be fitted inside a cupboard-see
Section 7.3).
2. If the boiler is sited in an unheated enclosure then it is
recommended to leave the ON/OFF Selector Switch in the
On position.
3. If the boiler is fitted in a room containing a bath or shower
reference must be made to the relevant requirements.
In GB this is the current I.E.E. Wiring Regulations and Building
Regulations.
In IE reference should be made to the current edition of I.S.
813 “Domestic Gas Installations” and the current ETCI rules.
4. If the boiler is to be fitted into a building of timber frame
construction then reference must be made to the current
edition of Institute of Gas Engineers Publication IGE/UP/7
(Gas Installations in Timber Framed Housing).
7.2
Clearances (Figs. 5 & 6)
1. A flat vertical area is required for the installation of the
boiler.
2. These dimensions include the necessary clearances around
the boiler for case removal, spanner access and air
movement. Additional clearances may be required for the
passage of pipes around local obstructions such as joists
running parallel to the front face of the boiler.
*This is the MINIMUM recommended dimension. Greater
clearance will aid installation and maintenance.
150mm Min*
780mm
450mm
200mm Min
(300mm Min if
using 80/125mm
flueing system)
5mm Min
5mm Min
450mm Min
For Servicing
Purposes
Fig. 5
Fig. 6
In Operation
5mm Min
At least 1.5°