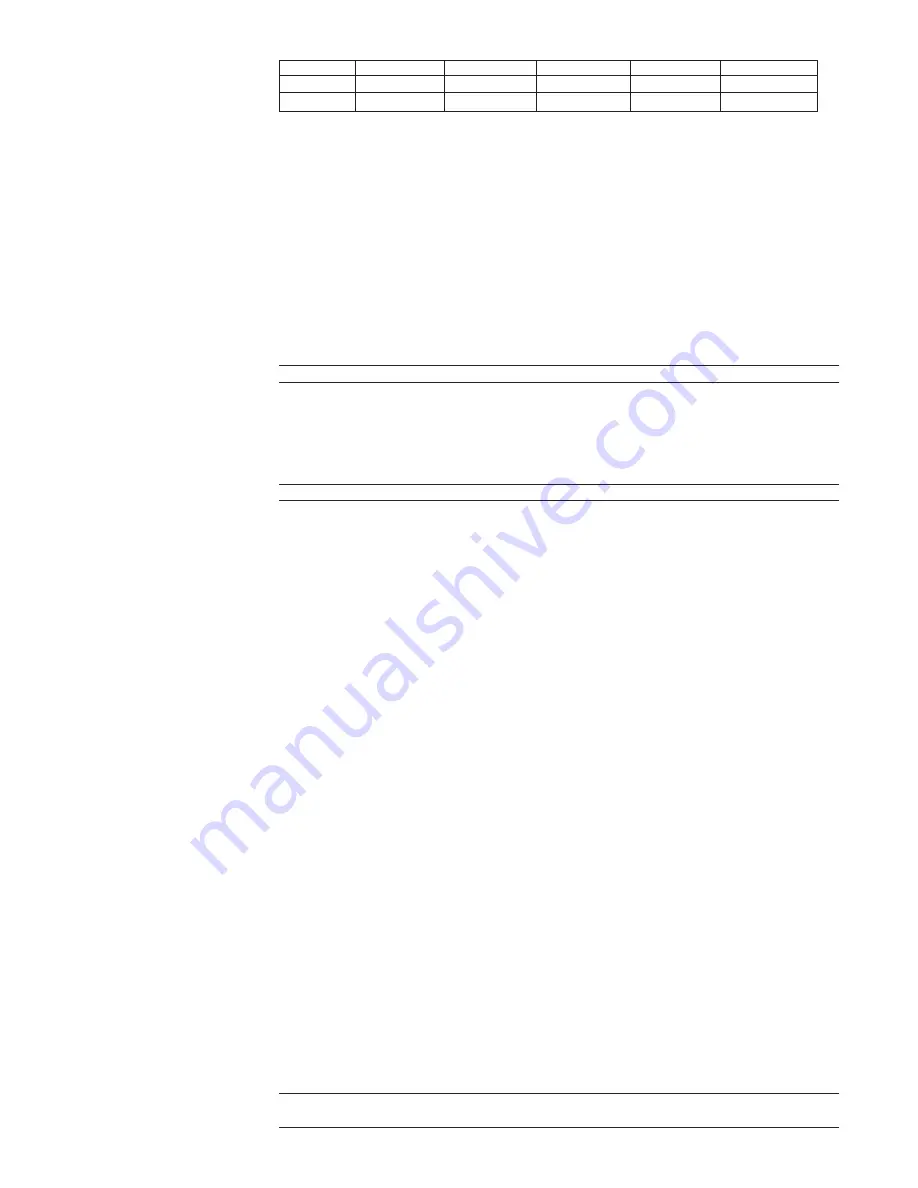
28
The boiler has been designed in full compliance with European reference standards and in particular
is equipped with the following
• Overheat thermostat
Thanks to a sensor placed on the heating flow, this thermostat interrupts the gas flow to the main
burner in case the water contained in the primary system has overheated. Under these conditions
the boiler locks out and you can only repeat the ignition procedure by pressing the reset button on
the boiler after you have remedied the cause of the trip.
It is forbidden to disenable this safety device
• Flue thermostat
This device, positioned on the flue inside the boiler, interrupts the flow of gas to the burner if the
temperature exceeds 90 °C. After verifying the cause of the trip, press the reset button positioned
on the thermostat itself, then press the release button on the boiler.
It is forbidden to disenable this safety device
• Flame ionization detector
The flame sensing electrode guarantees safety of operation in case of gas failure or incomplete
interlighting of the main burner.
Under such conditions the boiler is blocked.
You must press the reset button on the boiler to restore the normal operating conditions.
• Hydraulic differential pressure sensor
This pressure sensor, fitted on the hydraulic assembly, allows the main burner to light provided
the pump head is as required and protects the flue-water exchanger from possible lacks of water
or blockings of the pump.
• Supplementary running of the pump
The electronically-controlled supplementary running of the pump lasts 3 minutes, when the boiler
is in the central heating mode, after the burner has switched off due to a room thermostat inter-
vention.
• Frost protection device
Boilers electronic management includes a “frost protection” function in the central heating system
which operates the burner to reach a heating flow temperature of 30°C when the system heating
flow temperature drops below 5 °C.
This function is enabled as long as the boiler is connected to the a.c. power and gas supplies and
the pressure in the system is as specified.
• Pump-blocking prevention
In case there is no call for heat either from the central heating system or from the DHW system
for 24 hours on end the pump will automatically switch on for 10 seconds.
• 3-way antiblocking valve
If there is no heat demand for a period of 24 hours the 3-way valve switches completely.
This function is enabled if the electrical supply to the boiler is on.
• Hydraulic safety valve (heating circuit)
This device is set to 3 bar and is used for the heating circuit
The safety valve should be connected to a siphoned drain. Use as a means of draining the heating
circuit is strictly prohibited.
18. Control and
operation devices
Parameter N LUNA HT 280 LUNA HT 330 LUNA HT 1.120 LUNA HT 1.240 LUNA HT 1.280
H536
4900
4550
5850
5900
4550
H552
38
38
35
35
35
If the electronic circuit board is replaced, make sure that the parameters set are those specific to the
boiler model, as indicated in the documentation available from the authorised Service Centre.
Table 4