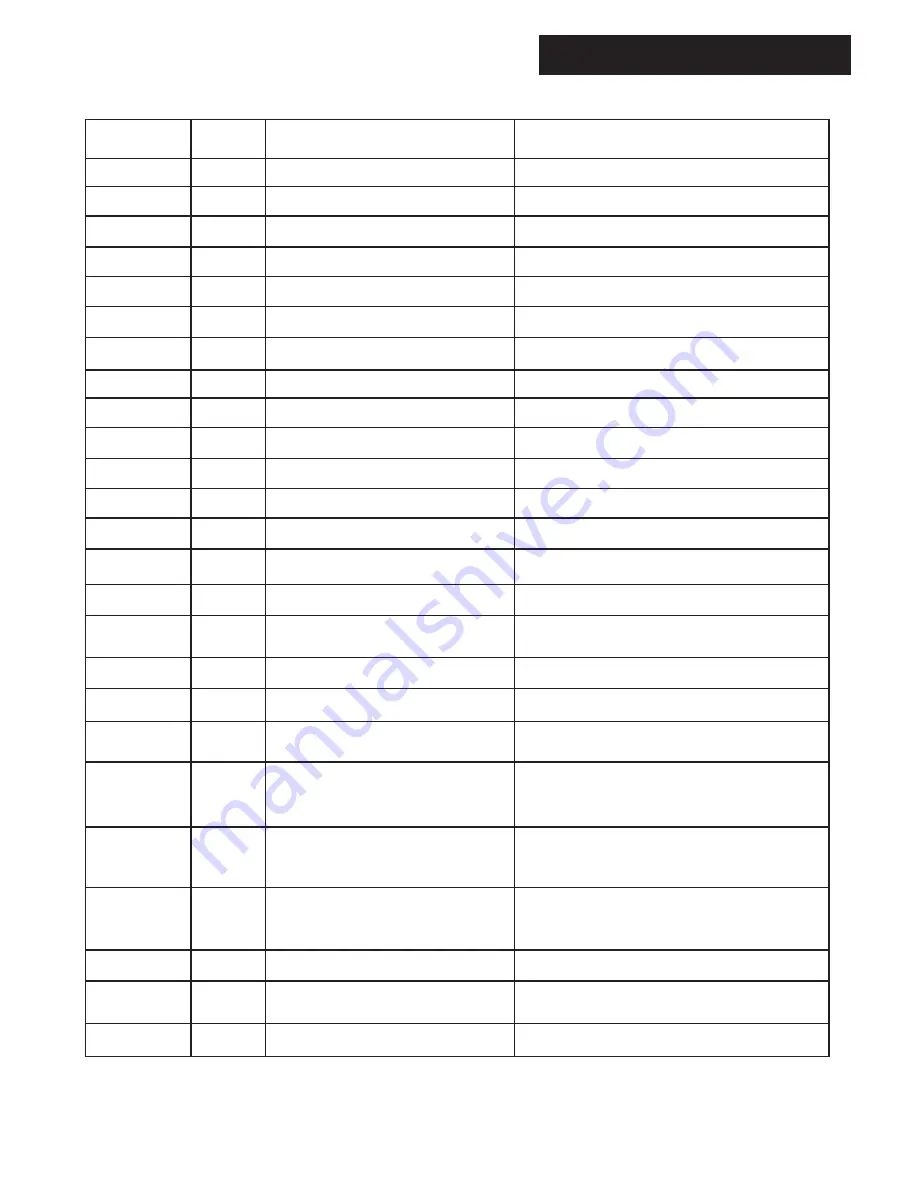
19
© Baxi Heating UK Ltd 2012
List of Errors & Sub-codes
12.0 Errors & Sub-codes
Gas valve connection fault
External probe fault
Differential water flow switch fault (still open)
Differential water flow switch fault (still closed)
Gas valve comand fault
Water refill activated
Maximum time of water refill
Central heating NTC sensor fault (s.c.)
Central heating NTC sensor fault (o.c.)
Return central heating NTC sensor fault (s.c.)
Return central heating NTC sensor fault (o.c.)
Flue NTC sensor fault (s.c.)
Flue NTC sensor fault (o.c.)
DHW NTC sensor fault (tank boiler) (s.c.)
DHW NTC sensor fault (tank boiler) (o.c.)
Incorrect calibration or obstruction in flue pipe
PCB to be set by the “Calibration Function”
Fan parameter out of range in autocalibration
Combustion test out of range in
autocalibration
Current out of range
Minimum gas valve current
Maximum gas valve current
No communication
Combustion test alarm during auto-setting
Precirculation alarm
Check the cable P.C.B./gas valve and gas valve plug
Check the sensor
Check the water flow switch
Check the water flow switch
Check the cable P.C.B./gas valve. Replace P.C.B. if necessary
Auto-Refill activated – motor energized
Auto-Refill open too long to fill – check system
Check the sensor
Check the sensor
Check the sensor
Check the sensor
Check the sensor
Check the sensor
Check the sensor
Check the sensor
Enable the Calibration Function and check flue for
obstruction
Enable the Calibration Function
Check the fan speed
Check the correct position and integrity of the sensing
electrode and cable
Check the correct position and integrity of the sensing
electrode and for flue recirculation. Enable the automatic
calibration function before replacing components.
Check the correct position and integrity of the sensing
electrode and for flue recirculation. Enable the automatic
calibration function before replacing components.
Check the correct position and integrity of the sensing
electrode and for flue recirculation. Enable the automatic
calibration function before replacing components.
Check cable between room unit and P.C.B. or R.F. link.
Failed the self check test during Calibration Function. Check
for re-circulation before changing Gas Valve
Check for correct circulation of water and pump
1
2
1
2
539
540
1
2
E09
E10
E12
E13
E15
E18
E19
E20
E20
E40
E40
E28
E28
E50
E50
E53
E55
E71
E72
E77
E78
E79
E83/84/85/86/87
E92
E109
Anomaly
Code
Internal
Code
Anomaly
Action
Note: (s.c.) = Short Circuit
(o.c.) = Open Circuit