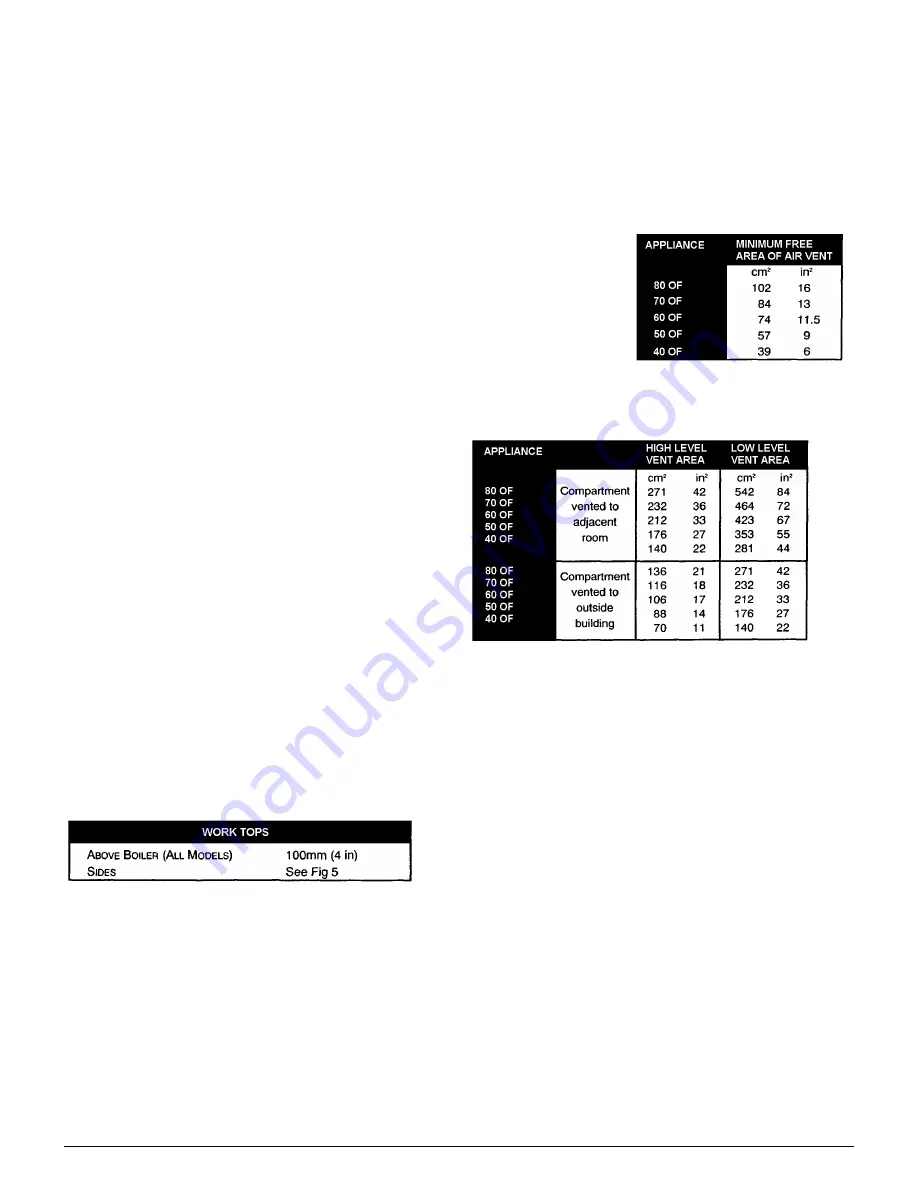
Installation Requirements - Page 3
GENERAL
The installation must be carried out by a Corgi Registered
Installer or other competent person and be in accordance
with relevant BS Codes of Practice, I.E.E. Regulations, Gas
Safety Regulations, Building Regulations and by-laws of the
Local Water Undertaking. References should be made to BS
6891, BS 6798, BS 5440 Pt 1 & 2, BS 5449, BS 5546 and
BS 1363.
IMPORTANT INFORMATION
VENTILATION
Detailed recommendations for air supply are given in BS
5440:2.
The following notes are intended to give general guidance.
The room in which the open flue unit is situated requires an
air vent which should be direct to outside or to a room which
itself has an air vent direct to outside. Where the boiler is in
a compartment with air vents direct to outside, the room
containing the compartment does not require the provisions
This product contains Refractory Ceramic Fibres (R.C.F.)
which are man-made vitreous silicate fibres. Excessive
exposure to these materials may cause temporary irritation
to eyes, skin and respiratory tract. Care must be taken when
handling these articles to ensure the release of dust or fibres
is kept to a minimum. To ensure that the release of fibres
from these articles is kept to a minimum, during installation
and servicing it is recommended that a H.E.P.A. filtered
vacuum is used to remove any dust, soot or other debris
accumulated in and around the appliance. This should be
of additional ventilation.
The actual minimum
effective area
requirements of
cupboard/compartment
air vents are based
upon the rated input of
the appliance.
performed before and after working on the installation. It is
recommended that any replaced item(s) are not broken up
but sealed within heavy duty polythene bags and clearly
labelled “R.C.F. waste”. This is not classified as “hazardous
waste” and may be disposed of at a tipping site licensed for
the disposal of industrial waste. Protective clothing is not
required when handling these articles but it is recommended
that gloves are worn and the normal hygiene rules of not
smoking, eating or drinking in the work area are followed and
always wash hands before eating or drinking.
SITING
The boiler must be fitted on a suitable outside or inside wall
with due considerations of the open flue requirements.
It should not be installed in a bathroom, bedroom or bed
sitting room.
A new or existing cupboard or compartment used to enclose
the boiler must be constructed specifically for this purpose.
Details of essential features of Cupboard / compartment
design are given in BS 5440:2.
CLEARANCES
The minimum vertical areas required for the appliances
depend on the appliance rating and its application. The
details are given in Fig 5.
We recommend the use of the Stadium BM729 “Black Hole”
ventilator which is available from your local merchant.
Ventilation areas required:
FLUE ARRANGEMENT
The 80, 70 OF are intended for connection with 125mm (5
in) flue tube. The 60, 50 and 40 OF are intended for
connection with 100mm (4 in) flue tube.
For full information on flues refer to BS 5440, but the general
requirements are as follows:
1)
The flue should be kept as short and as warm as
possible.
2)
Give maximum possible vertical rise from the appliance
before using any bends (preferably at least 600mm (24
in)). Avoid the use of right angled bends.
3)
Terminate in an approved terminal preferably above
ridge height but at least above the eaves of a pitched
roof.
4)
If Twin-wall type flue tubing is to be used the inner
tubing of the boiler adaptor must not project into the
draught diverter of the boiler. A boiler adaptor which
meets this requirement is obtainable.
5)
An existing brick chimney should be lined with acid and
moisture resistant materials such as stainless steel
flexible flue pipe. This is particularly important if the flue
is above 6.5 metres (20 ft) in height and not wholly
internal.
WHETHER OR NOT THE CHIMNEY IS TO BE LINED
IT MUST BE SWEPT THOROUGHLY BEFORE THE
INSTALLATION.
6)
Whatever type of flue is used it must be properly
supported and not simply supported on the boiler.