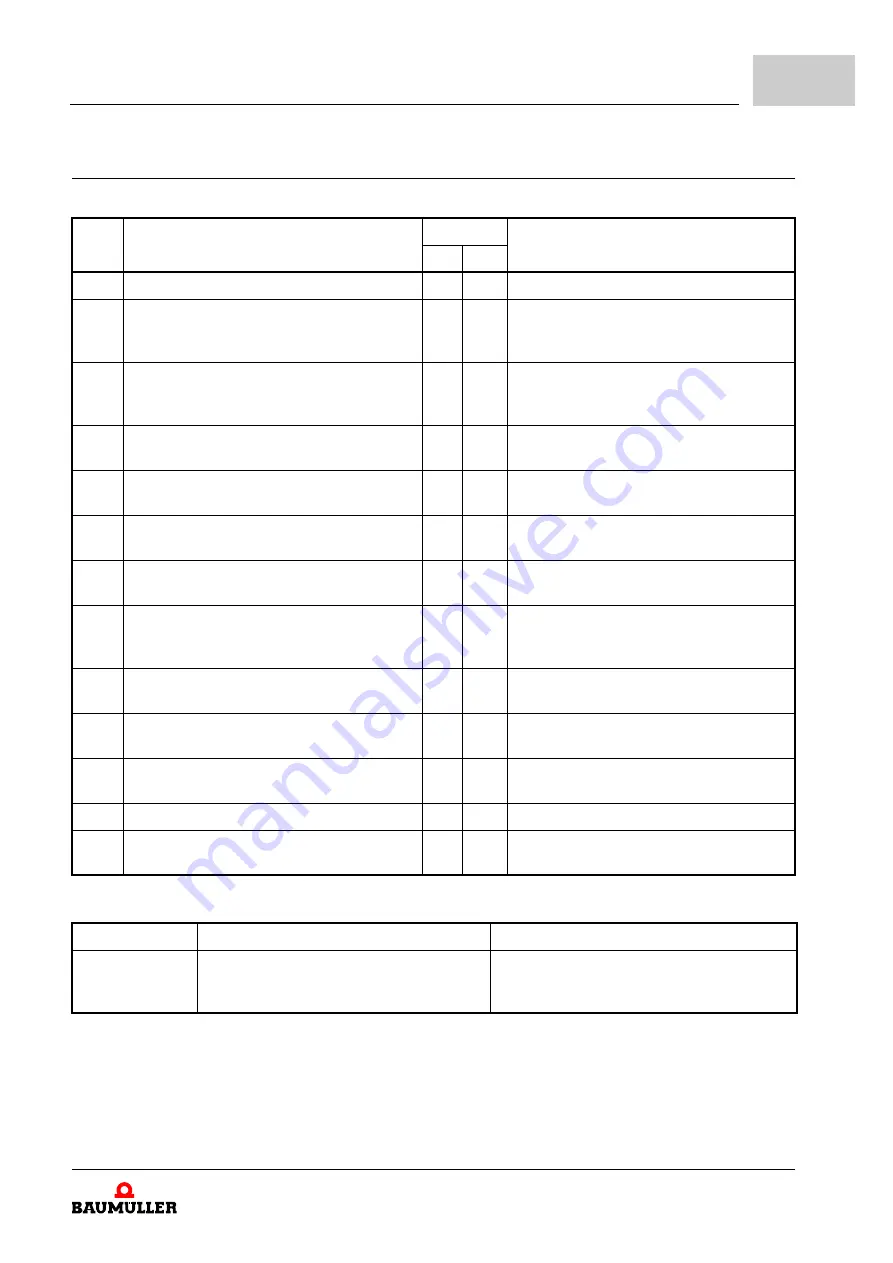
Checklists
Instruction handbook
Safe STO logic
BM5-SSL
Document No. 5.18007.02
71
B
B.2
Installation checklist
Serial
no.
Requirement
Fulfilled
Remarks
Yes No
2
Installation
2.1
Has it been ensured that there are no short
circuits from the wiring of the input and
output terminals?
2.2
Has it been ensured that the safety switch
devices have not been bypassed as a result
of wiring errors?
2.3
Has a wiring inspection in accordance with
the installation plan been conducted?
2.4
Are all connection plugs labeled according
to their allocation?
2.5
Are the connection terminals loaded with
the specified clamping torque?
2.6
Has it been ensured that the insulation of
the lines is not causing any faulty contacts?
2.7
Has the reliability of all terminal connections
been tested through mechanical tensile
loading?
2.8
Has a visual inspection of the installed
components been conducted?
2.10
Do the components meet the environmental
conditions prevailing in the application?
2.11
Does the system fulfill the required type of
protection?
2.12
Is degree of pollution 2 complied with?
2.13
Is the system protected from corrosive
substances?
Date
Name
Signature
Summary of Contents for BM5-SSL
Page 79: ......