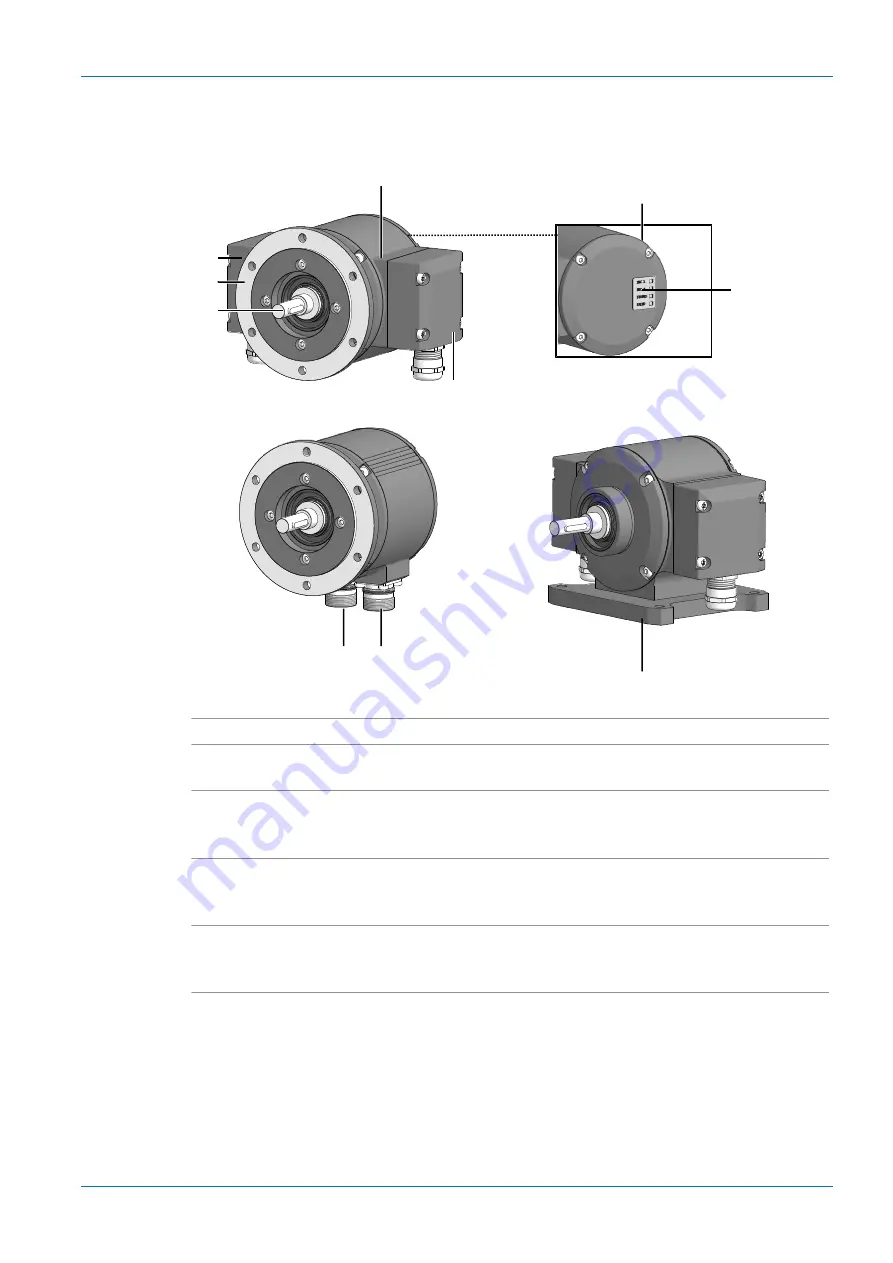
Baumer Hübner
Description
|
4
V1 | PMG10 & PMG10P SSI
Operating Manual
9
4
Description
4.1
Rotary encoder
1
9
8
2
5
3
4
10
7
6
Ill. 1:
Description PMG10
1
Housing
2
Cover
3
LED activity indicator
4
Housing base B3 (according to product
variant)
5
Radial flange connector: SSI, additional
incremental output 1 (optional), program-
ming interface (PMG10P only)
6
Radial flange connector: additional incre-
mental output 2 (option), speed switch
(option)
7
Radial terminal box: SSI, additional incre-
mental output 1 (optional), programming
interface (PMG10P only)
8
Solid shaft with key
9
EURO flange B10 (according to product
variant)
10
Radial terminal box: additional incremen-
tal output 2 (optional), speed switch (op-
tional)