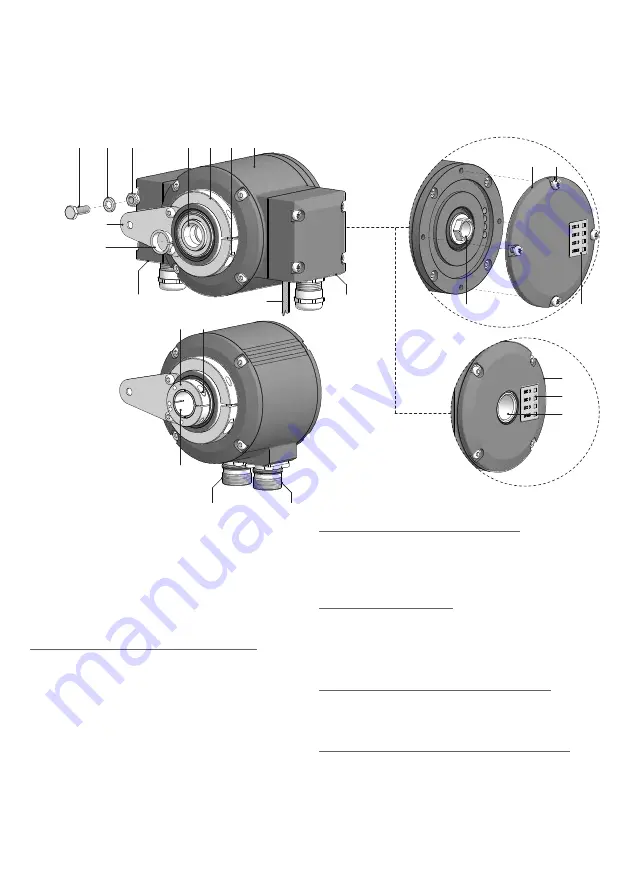
6d
6e 6f
1
7a 6a 6b
8c
8b
8a
6c
7b
5
[B]
[A]
7a
4
2
4
8a
3
2
[C]
[D]
PREPARATION
MB244EN - 11171691, 16A3, Baumer_HMG10-SSI_II_EN
5/32
3.
PREPARATION
3.1
Scope of delivery
1
Housing
2
Cover
3
Torx and slotted screw - DIN 7964,
M4x10 mm
4
LED function indicators
5
Earthing strap, length ~230 mm
Equipment for mounting a torque arm:
6a
Clamping ring adjustable through 360°
6b
Torx and slotted screw - ISO 7045,
M4x20 mm
6c
Torque plate
6d
Hexagon screw - ISO 4017,
M6x18 mm
6e
Washer - ISO 7090, B6�4
6f
Self-locking nut - ISO 10511, M6
Blind hollow shaft* or cone shaft*:
7a
Blind hollow shaft or cone shaft with
spanner lat 17 a/f
7b
Clamping element, not for cone shaft
Through hollow shaft*:
8a
Through hollow shaft
8b
Clamping ring
8c
Torx screw - ISO 7045, M3x12 mm
Radial terminal boxes* (see
[A]
SSI + additional output 1
[B]
Speed additional output 2
Radial lange connectors* (see
[C]
SSI + additional output 1
[D]
Speed additional output 2
* Depending on version