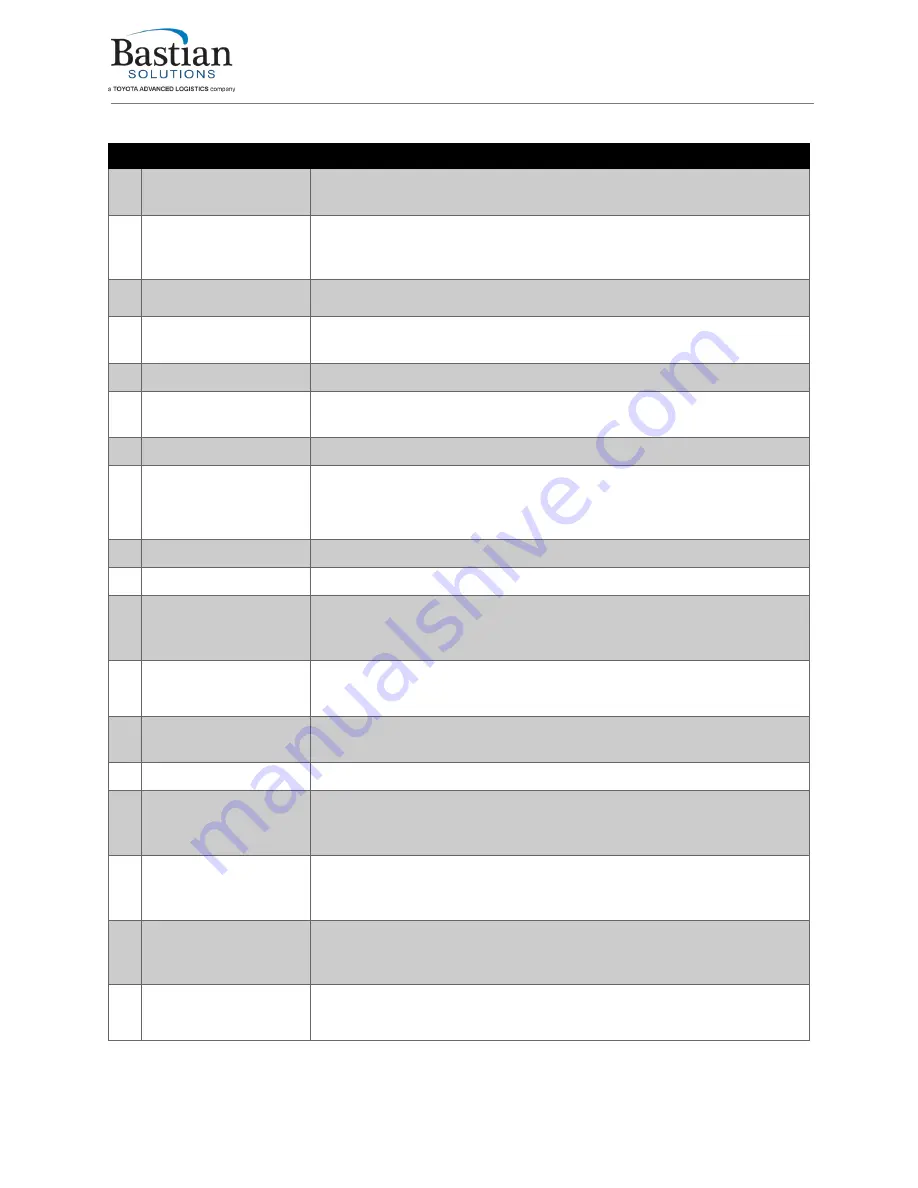
Installation and Maintenance Manual: RLVAC
Published February 2022
43
Table 6: Recommended Preventative Maintenance Schedule
✓
INTERVAL
DESCRIPTION OF CHECK
Before each startup
Make sure the conveyor is clear of foreign objects and all personnel are safely
away from moving parts.
Once per shift
Visual and auditory inspection to check for oil or air leakages, hardware
security, or any unusual noise that may indicate there is a problem with the
equipment.
Once per shift (or more
frequently as needed)
Drain water from all pneumatic filter bowls (if pneumatic takeup is used).
Daily
Inspect photoeyes, reflectors, and proximity switches, if present, to make sure
they are secure and properly aligned.
Weekly
Check for debris build-up on belt or conveying rollers. Clean if necessary.
Weekly
Check for accumulations of belt dust which may indicate a tracking problem.
Adjust tracking if needed.
Weekly
Visually inspect O-ring bands. Replace any that are damaged or slipping.
After first 4 hours
following each new belt
install, and monthly or
300 hours thereafter
Check proper belt tension and tracking. Re-tension or adjust as needed.
Monthly or 300 hours
Check for loose bolts, nuts, and fittings. Tighten if necessary.
Monthly or 300 hours
Remove any accumulated debris on the gearbox or motor housing.
Monthly or 300 hours
Check the proper functioning of all proximity switches and photoeyes, if
present. Secure all mounting brackets, clean the lenses and reflectors, and
replace any that are defective or damaged.
After first 24 hours, and
every 2 months or 500
hours thereafter
Check torque of all set screws (see ABB Instruction Manual for DODGE®
Bearings for appropriate torque values).
3 months or 1,000 hours
Regrease all bearings with No. 2 lithium complex base grease (see ABB
Instruction Manual for DODGE® Bearings for detailed lubrication instructions).
3 months or 1,000 hours Verify correct pressure setpoint of air regulators (if pneumatic takeup is used).
3 months or 1,000 hours
Inspect the drive belt and splices or lacing for wear or damage. Schedule a belt
replacement if severely worn (fabric layer beginning to show through the
facing). Schedule a belt repair if any damaged areas are found.
3 months or 1,000 hours
Walk the conveyor during operation and verify rotation of all conveying rollers.
Replace any damaged rollers or rollers that do not rotate smoothly. Listen for
unusual noises that may indicate a failing bearing.
3 months or 1,000 hours
For conveyors with PTO: Remove the PTO cover and inspect the PTO belt.
Check belt tension and adjust if necessary. Adjust timing pulley alignment if
the belt has signs of tracking problems. Replace the belt if damaged.
6 months or 2,000 hours
For conveyors with pneumatic drives: Clean and lubricate the takeup chains
with SAE 30/ISO 100 gear or chain oil. Inspect the condition of the chain
sprockets. Replace or swap the sprockets if the teeth are severely worn into a