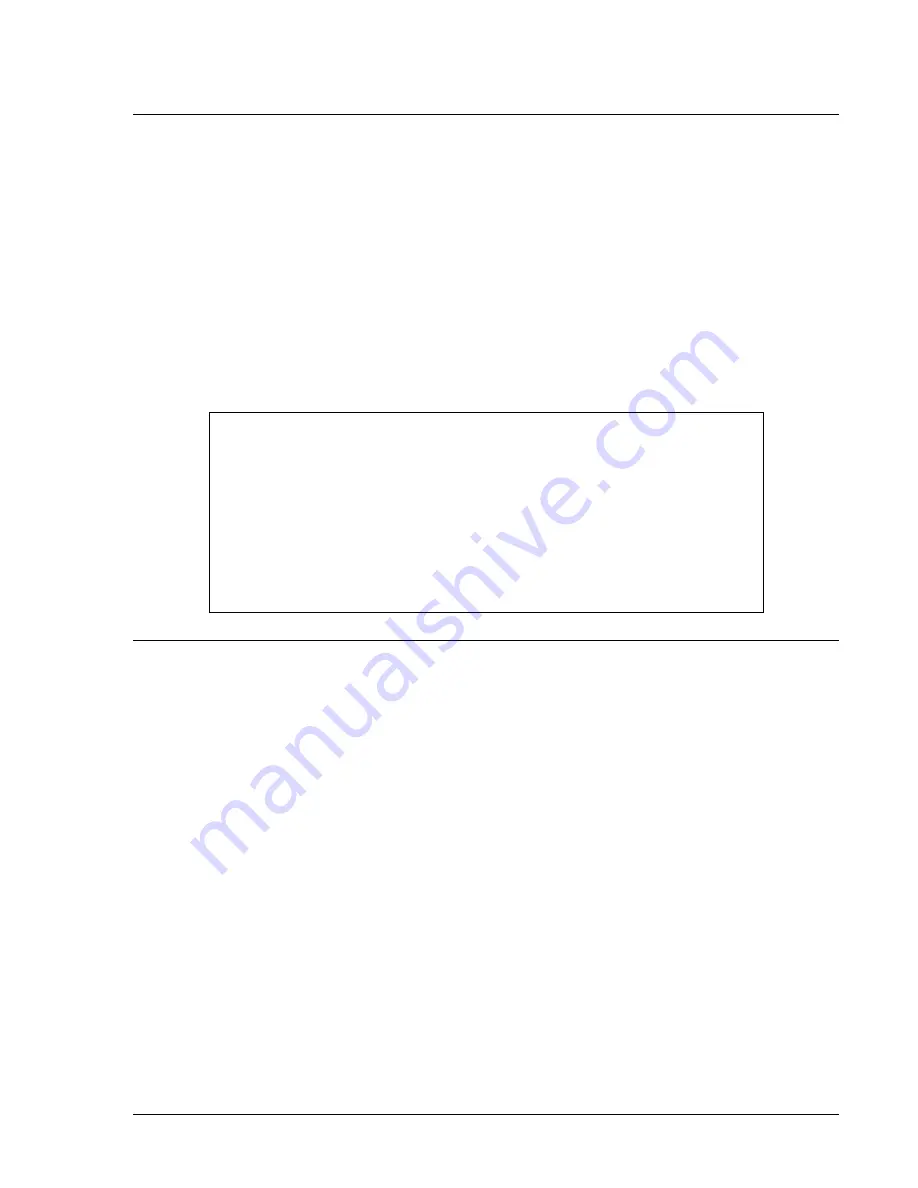
BE1-CDS220 ASCII
Command
Interface
11-1
SECTION 11
•
ASCII COMMAND INTERFACE
INTRODUCTION
Relay and power system information can be retrieved from a remote location using the ASCII command
interface. The ASCII command interface is also used to enter settings, retrieve reports and metering
information, and perform control operations. A communication port on the relay front panel provides a
temporary, local interface for communication. Communication ports on the rear panel provide a
permanent communication interface.
Front and rear panel communication ports can be connected to computers, terminals, serial printers,
modems, and intermediate communication/control interfaces such as RS-232 serial multiplexors. BE1-
CDS220 communication protocols support ASCII and binary data transmissions. ASCII data is used to
send and receive human readable data and commands. Binary data is used for computer communication
and transmission of raw oscillographic fault data if available.
DNP, Modbus
, and other common protocols are also available. Available communication protocol
instruction manuals include 9313900991 for Modbus
and 9313900992 for DNP 3.0. For information
about other protocols, consult your Basler Electric representative.
SERIAL PORT
Communication connections consist of two Data Communication Equipment (DCE) RS-232 ports, one
RS-485 port, and an IRIG port. The BE1-CDS220 communication protocol is compatible with readily
available modem/terminal software. If required, password protection provides security against
unauthorized operation. Detailed information about making communication connections is provided in
Section 12, Installation. Communications port setup is covered in this section. Security settings are
covered in Section 9, Security.
RS-232 Ports
Two female RS-232 (DB-9) connectors are provided. One port is located on the front panel and is
designated COM 0. Another port is located on the rear panel and is designated COM 1. Both ports
support full-duplex operation. Polled operation is possible at the rear port using a simple RS-232 splitter if
a polling address is programmed for COM 1.
RS-485 Port
RS-485 terminal block connections are located on the rear panel and designated COM 2. This port
supports half-duplex, multi-drop operation. Multi-drop operation is possible if a polling address is
programmed for the port.
IRIG-B Input
Connections at the rear panel accept a demodulated (TTL) IRIG-B signal and provide the capability to
time synchronize the BE1-CDS220 internal clock to within one millisecond of the IRIG-B source.
NOTE
HyperTerminal as shipped with Windows
98, either first or second edition,
cannot be used for communications with the relay due to a problem introduced in
the Windows
98 version of HyperTerminal. The software bug is associated with
the carriage return/line feed function when acting as a terminal emulator. An
upgrade to HyperTerminal that fixes the problem is available from the Microsoft's
source of HyperTerminal (Hilgraeve, Inc.) at www.hilgraeve.com. The upgrade is
referred to as "HyperTerminal - Private Edition." Companies that download and
use this software must review the terms and conditions associated with the use
of the software.
Summary of Contents for BE1-CDS220
Page 2: ......
Page 10: ...viii Introduction BE1 CDS220 This page intentionally left blank...
Page 36: ...ii Quick Start BE1 CDS220 This page intentionally left blank...
Page 48: ...ii Input And Output Functions BE1 CDS220 This page intentionally left blank...
Page 66: ...iv Protection and Control BE1 CDS220 This page intentionally left blank...
Page 112: ...ii Metering BE1 CDS220 This page intentionally left blank...
Page 116: ...5 4 Metering BE1 CDS220 This page intentionally left blank...
Page 166: ...ii BESTlogic Programmable Logic BE1 CDS220 This page intentionally left blank...
Page 176: ...7 10 BESTlogic Programmable Logic BE1 CDS220 This page intentionally left blank...
Page 234: ...8 56 Application BE1 CDS220 This page intentionally left blank...
Page 236: ...ii Security BE1 CDS220 This page intentionally left blank...
Page 240: ...9 4 Security BE1 CDS220 This page intentionally left blank...
Page 242: ...ii Human Machine Interface BE1 CDS220 This page intentionally left blank...
Page 256: ...10 14 Human Machine Interface BE1 CDS220 This page intentionally left blank...
Page 258: ...ii ASCII Command Interface BE1 CDS220 This page intentionally left blank...
Page 422: ...14 32 BESTCOMS Software BE1 CDS220 This page intentionally left blank...
Page 424: ...ii Time Current Characteristics BE1 CDS220 This page intentionally left blank...
Page 452: ...ii Terminal Communication BE1 CDS220 This page intentionally left blank...
Page 456: ...C 4 Terminal Communication BE1 CDS220 This page intentionally left blank...
Page 458: ...ii Settings Calculations BE1 CDS220 This page intentionally left blank...
Page 475: ......