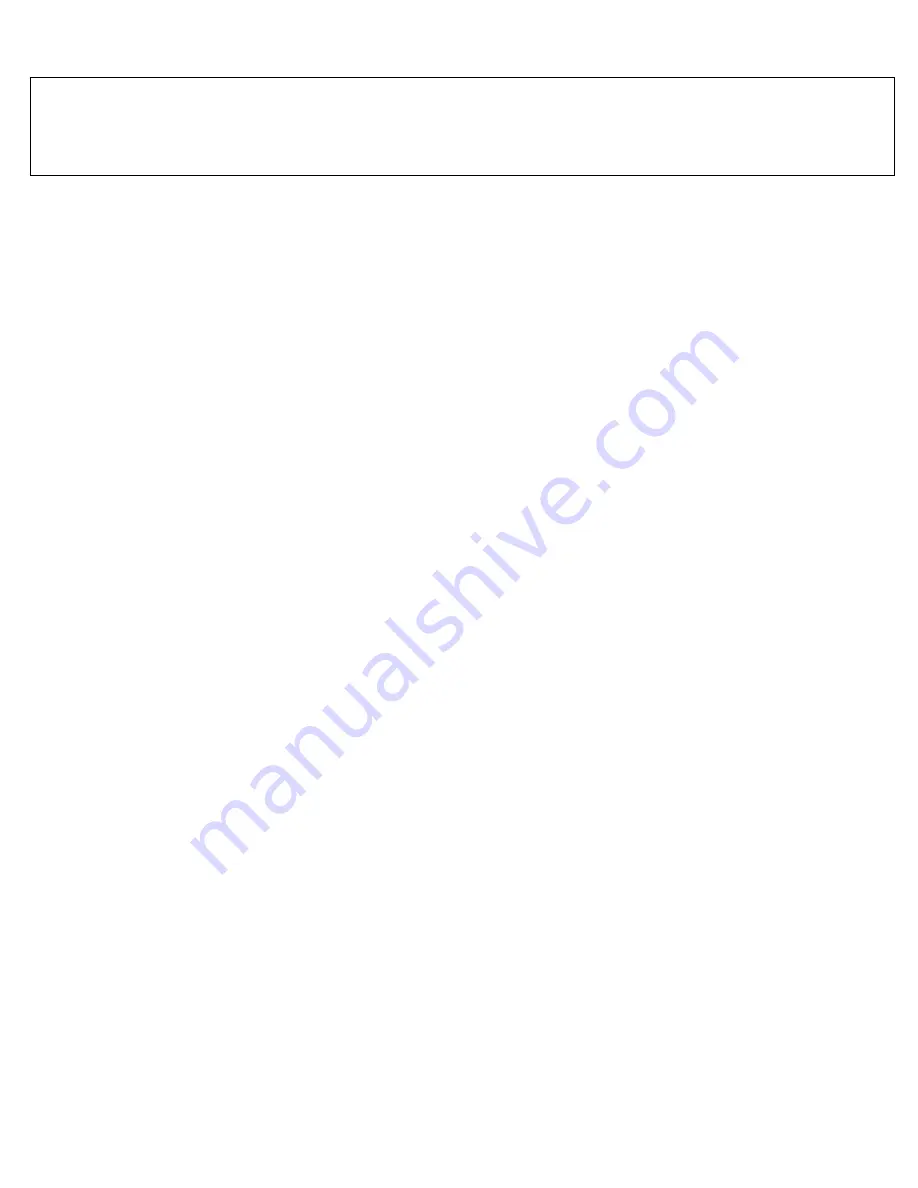
WALK BEHIND POWER TROWEL INSTRUCTION MANUAL
We:
Bartell Morrison Inc.
Bartell Morrison (USA) LLC.
375 Annagem Blvd.
12 Industrial Drive
Mississauga, Ontario, Canada
Keyport, New Jersey, United States of America
L5T 3A7
07735
Tel: 905-364-4200
Fax: 905-364-4201
Tel: 732-566-5400
Fax: 732-566-5444
Declare under our sole responsibility that the product to which this declaration relates is in conformity with the
following standard(s) or other normative documents.
Déclarons sous notre responsabilité que le produit cette déclaration est conforme aux normes suivantes ou d’autres
documents habituels.
Verklaren onder onze verantwoordelijkheid dat het product naar welke de verklaring verwijst conform de volgende
standaards of anders gebruikelijke documenten is.
Declaramos bajo nuestra única responsabilidad que el producto en lo que esta declaración concierne, es conforme
con la siguiente normativa u otros documentos.
Declara sob sua responsabilidade que o produto a quem esta declaração interessar, está em comformidade com
os seguintes documentos legais ou normas directivas.
Dichiariamo sotto la ns. unica responsibilita che il prodotto al quale questa dichiarazione si riferisce, è fabbricato in
conformità ai seguenti standard e documenti di normative.
EN 349:1993
Safety of Machinery - Minimum gaps to avoid crushing of parts of the human body.
EN 418:1993
Safety of Machinery - Emergency stop equipment, functional aspects - Principles for
design
EN 12100-1:2003
Safety of Machinery - Basic Concepts, general principles for design - Part 1: Basic
Terminology, methodology
EN 12100-2:2003
Safety of Machinery - Basic Concepts, general principles for design - Part 2: Technical
Principles
EN ISO 4872:1978
Acoustics - Measurement of Airborne noise emitted by construction equipment intended
for outdoor use - Method for determining compliance with noise limits.
EN ISO 5349-1:2001 Mechanical vibration. Measurement and evaluation of human exposure to hand-
transmitted vibration. General requirements
EN ISO 5349-2:2001 Mechanical vibration. Measurement and assessment of human exposure to hand-
transmitted vibration. Practical guidance for measurement at the workplace.
Following the provisions of Directive(s):
Suivant les directive(s) déterminées:
Volgens de vastgestelde richtlijnen:
Siguiendo las directiva(s):
No sequimento das clausulas da Directiva(s):
Seguendo quanto indicato dalla Direttiva(s):
98/37/EC
Machinery Directive
2000/14/EC
Noise Directive
2001/95/EC
General Product Safety Directive
2002/95/EC
Reduction of Hazardous Waste Directive
Declaration of Conformity / Certificat de conformité / Gelijkvormigheids certificaat
Declaración de Conformidad/Declaração de Conformidade/Dichiarazione Di Conformita
20
375 ANNAGEM BLVD., MISSISSAUGA, ONTARIO, CANADA L5T 3A7, 905-364-4200 FAX 905-364-4201
CREATED: 07/04
REVISED: 05/10
CREATED: 06/12
22