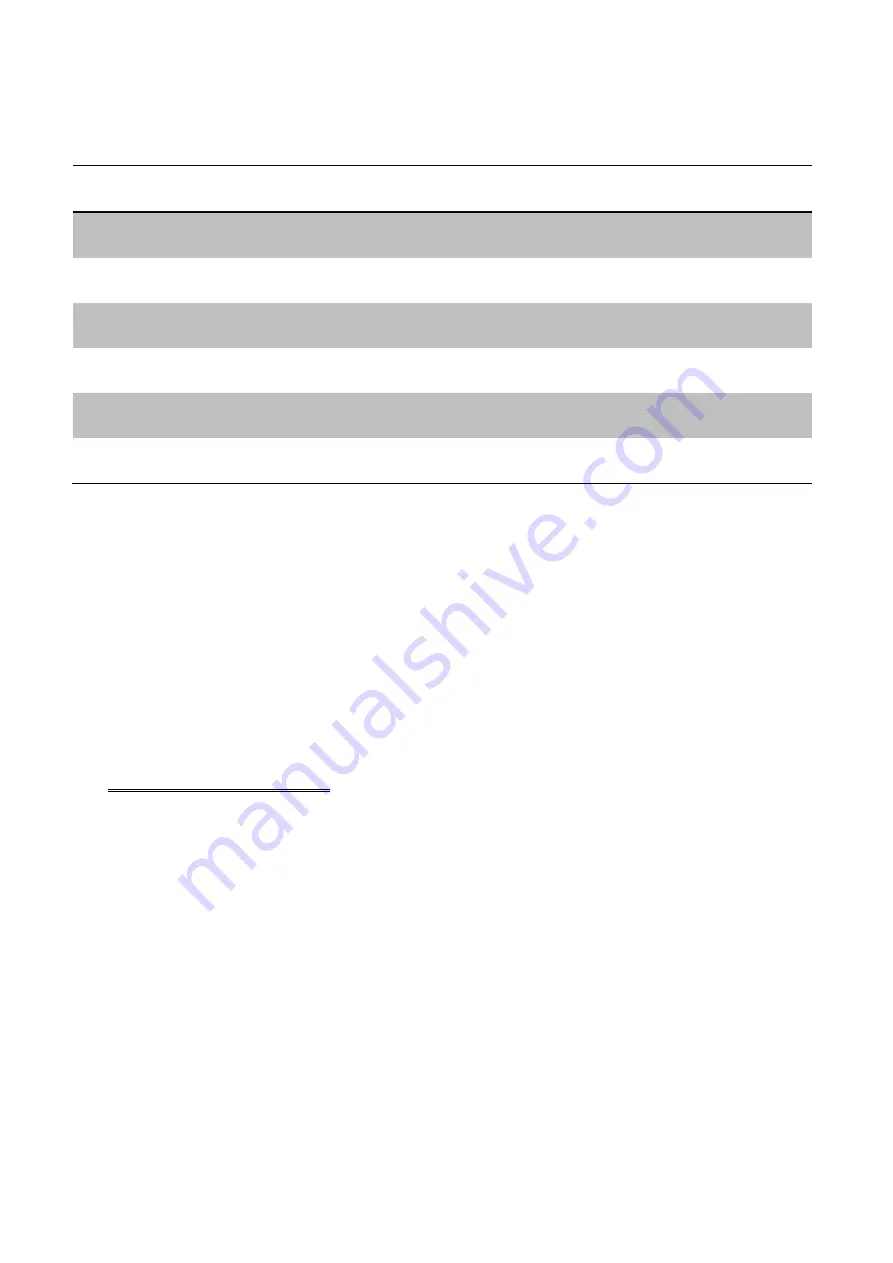
5
Technical data
Motor HP
3hp
Motor KW Rating
2.2kw
Motor RPM
1410rpm
Unit weight
67KG
Plate type
Standard 250mm plate or Cub Shoe
Plate Bolt Types
M12x25 Countersunk socket head
Main Construction
Powder Coated Steel
Ensure all re-tipped and new grinding plates are properly balanced.
Operation Instructions
The floor grinder is designed to be used either wet or dry. If the floor is being
ground dry, ensure a suitable industrial vacuum is connected and that
operator is wearing suitable breathing respiratory equipment. Contact your
local work place health authority to ensure that their requirements regarding
respiratory equipment are being met.
Starting the Grinder
Check the grinding plate being used is suitable for the material being ground
AND THAT THEY ARE CORRECTLY BALANCED.
Check that the grinding plates being used are in good order and properly
attached, with all countersunk bolts firmly in place. Check this occasionally
during use, as they can work loose during operation.
Check that the grinding plate is adjusted so that it sits level on the ground.
Check that all nuts and bolts on the folding handle latch are tight and firm.
Raise the grinding plates from the floor.
Summary of Contents for SPE DG250-II
Page 13: ...12 Exploded View...