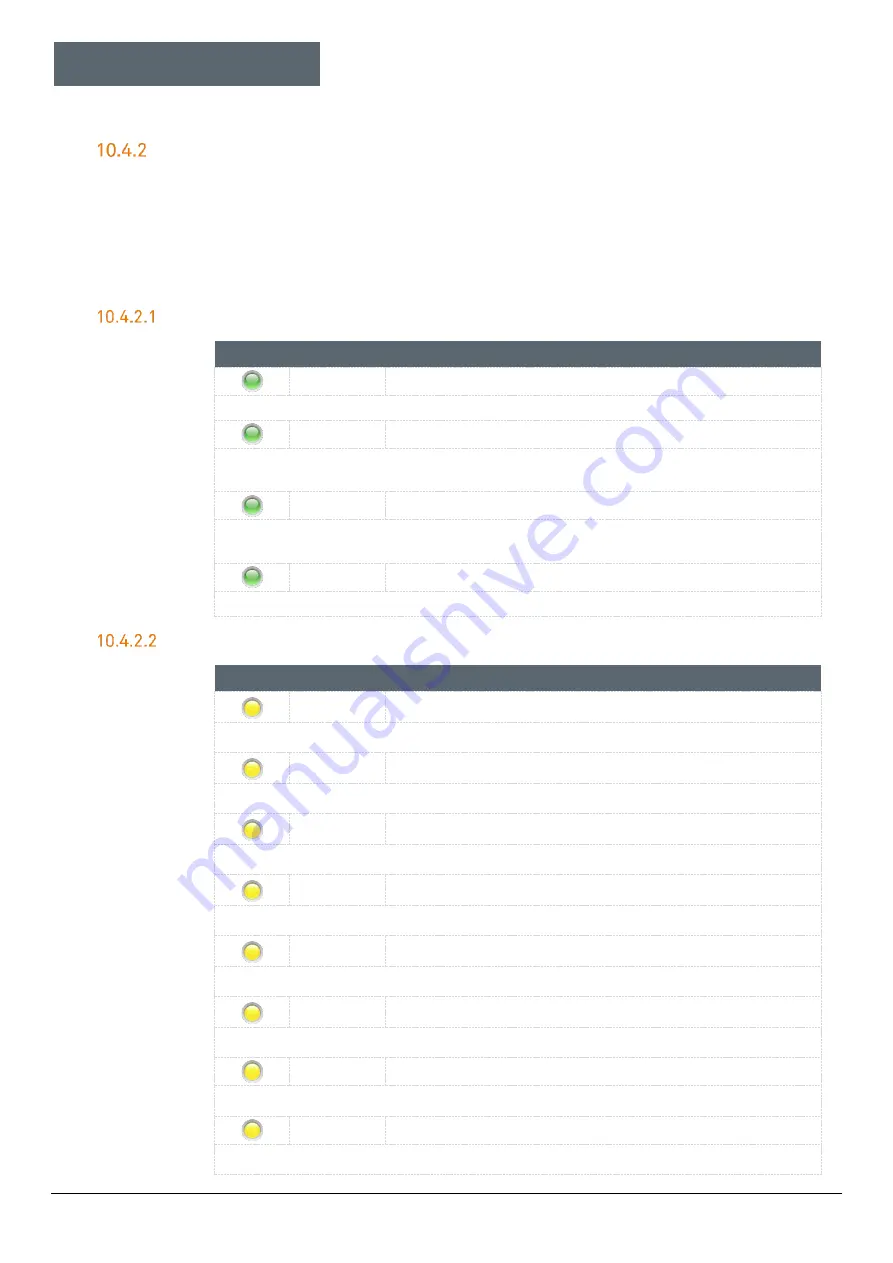
Maintenance and care
Ex p Control unit
APEX
py
Page 88 of 96
01-37A2-7D0006_py_Manual_Exp-Control-Unit_20210923_a_en.docx
Rev. 0
Error messages
The control units give plain text messages which are divided into 3 categories.
Positive messages are notifications that do not affect system availability.
Warning messages are notifications that affect parts of the system.
Alarm messages are notifications that lead to the shutdown of the
protected device.
Positive messages
Status
Code
Plain text
00000001
Purging cycle active
The control unit has started the purging process.
00000002
Ex p ready
The control unit has successfully completed the purging process. The main switch or
bridge HS_IN / HS_OUT is not closed.
00000003
Ex p enabled
The control unit has successfully completed the purging process. The main switch or
bridge HS_IN / HS_OUT is closed and enabled.
00000004
p3 reached
The set point value “p3” purging flow is reached and the purging time counts down.
Warning messages
Status
Code
Plain text
00000005
Bypass active
The bypass is activated on the control unit.
00000006
Door contact / main switch open
The main switch or bridge HS_IN / HS_OUT is not closed.
00000007
p2 not reached
The set point value p2 “pre-alarm” is not reached.
00000008
p4 exceeded
The set point value p4 “Maximum pressure – operation” is exceeded.
00000009
p5 exceeded
The set point value p5 “Maximum pressure – Purging” is exceeded.
0000000A
Temperature sensor 1 exceeded
The set point temperature value at sensor 1 is exceeded.
0000000B
Temperature sensor 2 exceeded
The set point temperature value at sensor 2 is exceeded.
0000000C
Temperature sensor 3 exceeded
The set point temperature value at sensor 3 is exceeded.