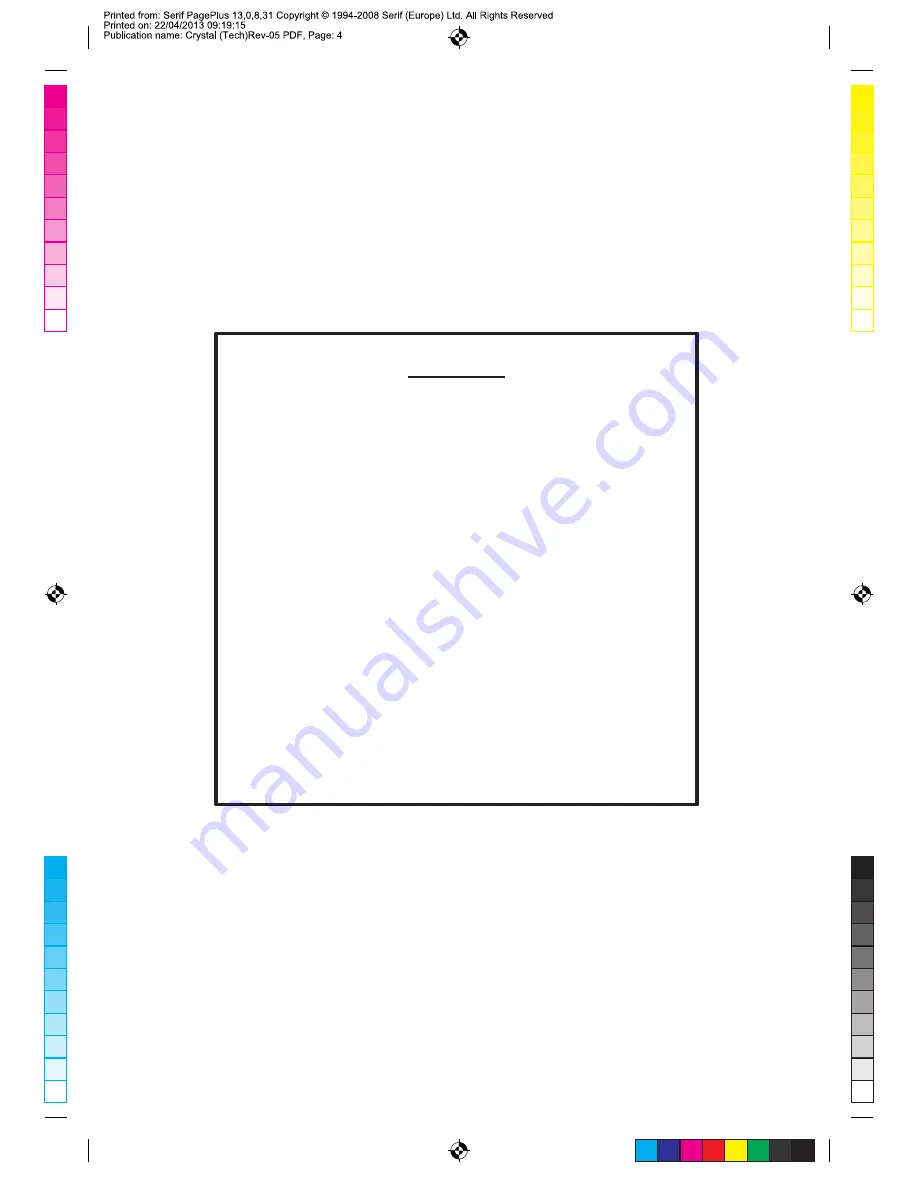
4
Contents
SECTION
1
User Categories
2
Specifications
3
Powerchair Diagram
4
Maintenance Checks
5
Tool Requirements
6
Upholstery
7
Armrests
8
Footrests
9
Brakes
10
Push Handles
11
Frame, Locking Links And Cross Braces 12
Castors
13
Power Drive System
14
Electrical System
15a
Programmable Controller (P&G Pilot) 15a
Programmable Controller (Dynamic DL) 16
Elevating Legrest
17
Armrest Outriggers
18
Detachable Tray
19
Transportation.