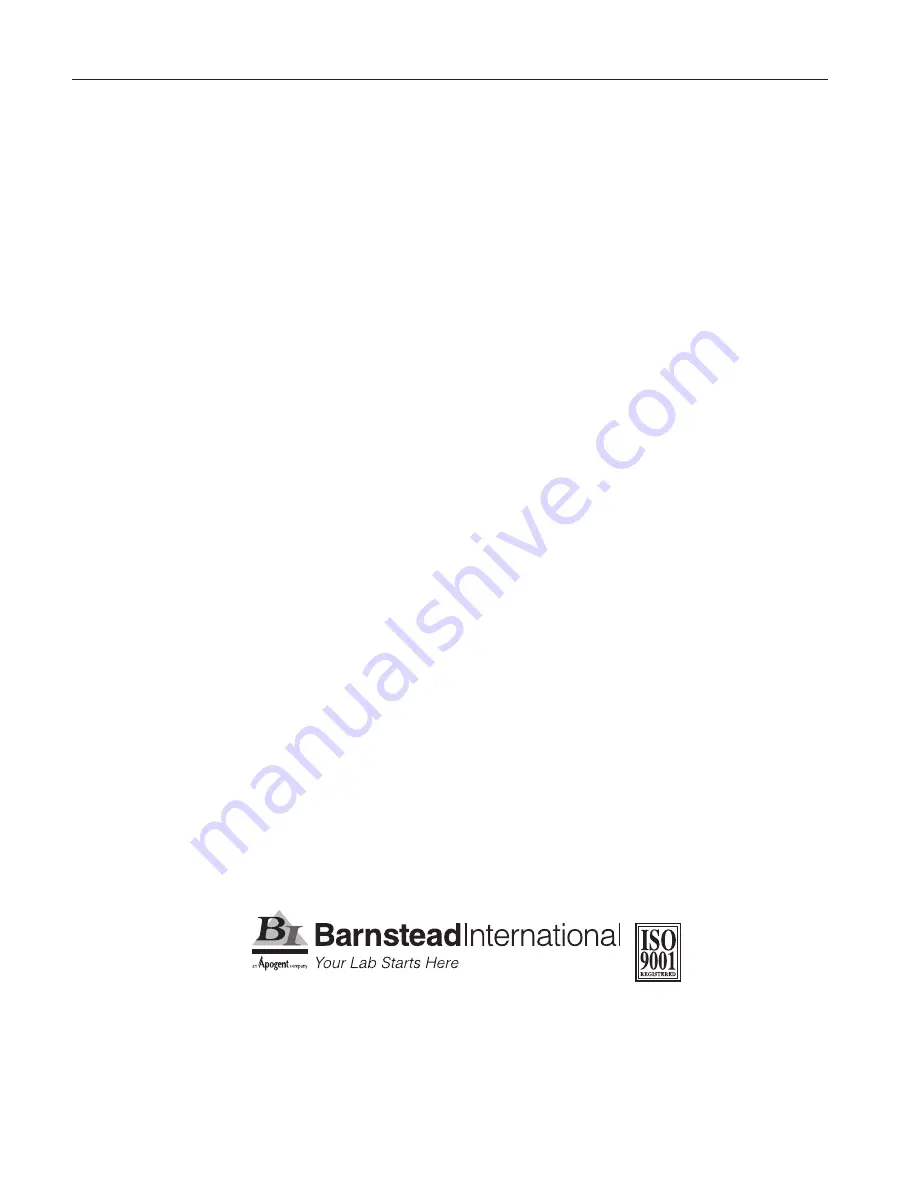
40
40
One Year Limited Warranty
Barnstead International (“BARNSTEAD”) warrants that if a product manufactured by Barnstead shall be free of
defects in materials and workmanship for one (1) year from the first to occur of (i) the date the product is sold by
BARNSTEAD or (ii) the date the product is purchased by the original retail customer (the “Commencement
Date”). Except as expressly stated above, BARNSTEAD MAKES NO OTHER WARRANTY, EXPRESSED OR
IMPLIED, WITH RESPECT TO THE PRODUCTS AND EXPRESSLY DISCLAIMS ANY AND ALL WARRANTIES,
INCLUDING BUT NOT LIMITED TO, WARRANTIES OF DESIGN, MERCHANT ABILITY AND FITNESS FOR A
PARTICULAR PURPOSE.
An authorized representative of BARNSTEAD must perform all warranty inspections. In the event of a defect
covered by BARNSTEAD’s warranty, BARNSTEAD shall, as its sole obligation and exclusive remedy, provide free
replacement parts to remedy the defective product. In addition, for products sold by BARNSTEAD within the con-
tinental United States or Canada, BARNSTEAD shall provide provide free labor to repair the products with the
replacement parts, but only for a period of ninety (90) days from the Commencement Date.
BARNSTEAD’s warranty provided hereunder shall be null and void and without further force or effect if there is
any (i) repair made to the product by a party other than BARNSTEAD or its duly authorized service representa-
tive, (ii) misuse (including use inconsistent with written operating instructions for the product), mishandling, conta-
mination, overheating, modification or alteration of the product by any customer or third party or (iii) use of
replacement parts that are obtained from a party who is not an authorized dealer of BARNSTEAD.
Heating elements, because of their susceptibility to overheating and contamination, must be returned to the
BARNSTEAD factory and if, upon inspection, it is concluded that failure is due to factors other than excessive
high temperature or contamination, BARNSTEAD will provide warranty replacement. As a condition to the return
of any product, or any constituent part thereof, to BARNSTEAD’s factory, it shall be sent prepaid and a prior writ-
ten authorization from BARNSTEAD assigning a Return Materials Number to the product or part shall be
obtained.
IN NO EVENT SHALL BARNSTEAD BE LIABLE TO ANY PARTY FOR ANY DIRECT, INDIRECT, SPECIAL, INCI-
DENTAL, OR CONSEQUENTIAL DAMAGES, OR FOR ANY DAMAGES RESULTING FROM LOSS OF USE OR
PROFITS, ANTICIPATED OR OTHERWISE, ARISING OUT OF OR IN CONNECTION WITH THE SALE, USE
OR PERFORMANCE OF ANY PRODUCTS, WHETHER SUCH CLAIM IS BASED ON CONTRACT, TORT
(INCLUDING NEGLIGENCE), ANY THEORY OF STRICT LIABILITY OR REGULATORY ACTION.
The name of the authorized Barnstead International dealer nearest you may be obtained by calling
1-800-446-6060 (563-556-2241) or writing to:
2555 Kerper Boulevard
P.O. Box 797
Dubuque, Iowa 52001-0797
Phone: 563-556-2241 or 800-553-0039
Fax: 563-589-0516
E-mail: [email protected]
www.barnstead.com