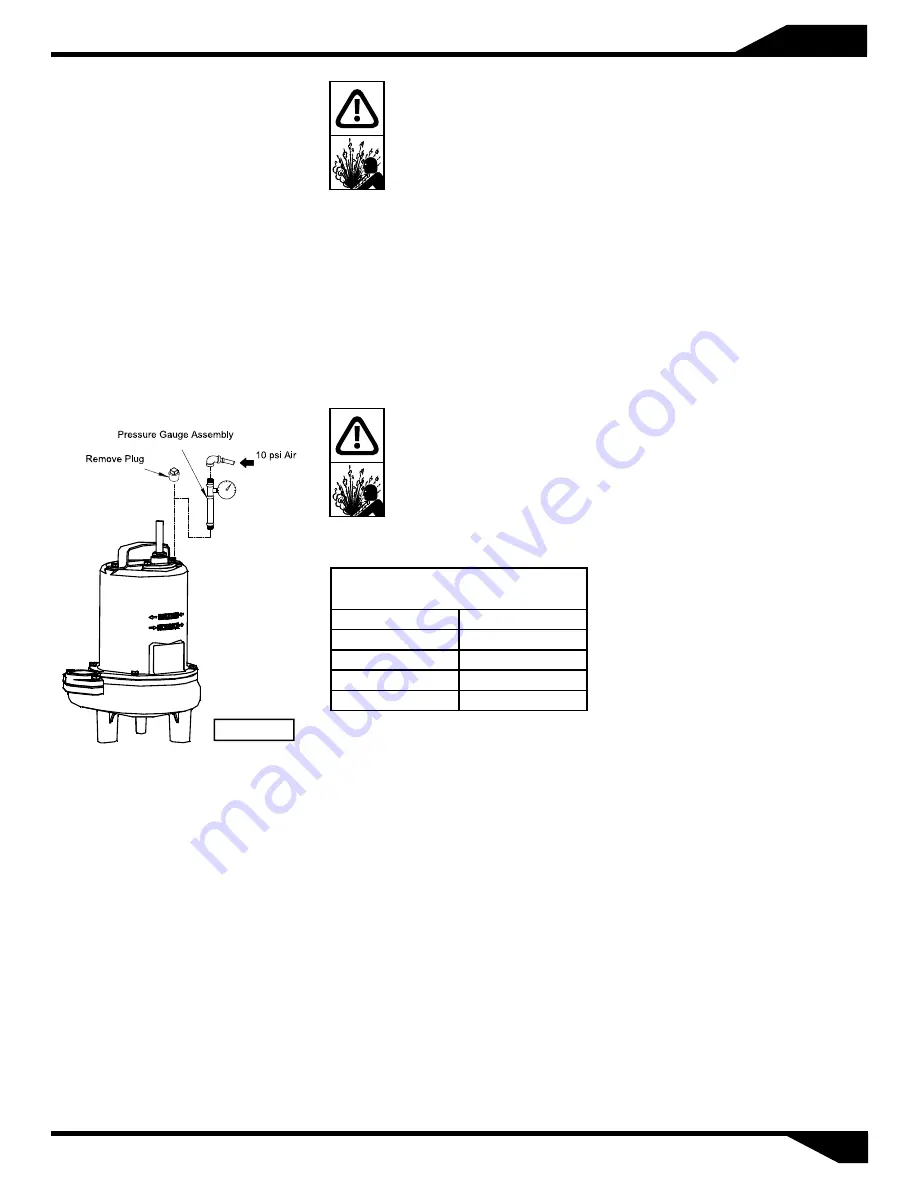
Pressure Test (If oil has been
drained)
- Remove pipe plug (34)
from housing (3). Apply pipe sealant
to pressure gauge assembly and
tighten into hole. Pressurize motor
housing to 10 PSI. Use soap solution
around the sealed areas and inspect
joints for "air bubbles".
If, after five minutes, the pressure is
still holding constant, and no
"bubbles" are observed, slowly bleed
the pressure and remove the gauge
assembly. Replace oil. Leek must be
located and repaired if pressure does
not hold.
Pressure Test (If oil has NOT been
drained)
- Oil should be at normal
level. Remove pipe plug (34) from
housing (3). Apply pipe sealant to
pressure gauge assembly and tighten
into hole. Pressurize motor housing
to 10 PSI. Use soap solution around
the sealed areas above the oil level
and inspect joints for "air bubbles".
For sealed areas below oil level, leeks
will seep oil. If, after five minutes, the
pressure is still holding constant, and
no "bubbles", oil seepage is
observed, slowly bleed the pressure
and remove the gauge assembly.
Replace oil. Leek must be located and
repaired if pressure does not hold.
Oil Replacement
- Set unit upright
and refill with new cooling oil as per
table below. Fill to just above motor,
but below capacitor as an air space
must remain in the top of the
housing to compensate for oil
expansion. Apply pipe thread
compound to threads of pipe plug
(34) then assemble to housing (3).
Cooling Oil
Recommended Supplier/Grade
BP
Enerpar SE100
Conoco
Pale Parafin 22
Mobile
D.T.E. Oil Light
Shell Canada
Transformer-10
Texaco
Diala-Oil-AX
Disassembly
Impeller and Volute:
1. Disconnect power.
Motor and Capacitor:
6. Position unit upright using blocks
or 4" piece of pvc pipe, to avoid
resting unit on shaft.
05
Service
Pressure builds up extremely
fast, increase pressure by
"TAPPING" air nozzle. Too
much pressure will damage
seal.
DO NOT exceed 10 PSI.
DO
NOT
overfill
oil.
Overfilling of housing with oil
can create excessive and
dangerous hydraulic pressure
which can destroy the pump
and create a hazard.
Overfilling oil voids warranty.
5. Remove v-gasket (23) and replace if
damaged.
2. Remove capscrews and washers
(13), vertically lift motor housing and
seal plate assembly from volute (18).
Clean out volute if necessary.
3. Inspect gasket (14) and replace if
cut or damaged.
4. Clean and examine impeller (16),
for cracks or breakage and replace if
required. To remove impeller (16),
remove impeller nut (17) with a
wheel
puller,
pull
impeller
straight of shaft and remove key.
7. Remove wire nut, friction rings and
grommet from motor housing (3).
Pull cord through and disconnect the
wires from the terminals.
8. Disconnect all wires noting where
each is connected. There is a number
next to each pin for reference on the
bottom of the block.
12. On Single Phase units only. Check
motor capacitor (4) with an Ohm
meter by first grounding the
capacitor by placing a screwdriver
across both terminals and then
removing screwdriver. Connect Ohm
meter (set on high scale) to
terminals. If needle moves to infinity
(∞) then drifts back, the capacitor is
good. If needle does not move or
moves to infinity (∞) and does not
drift back, replace capacitor (4).
13. Inspect motor winding for shorts
and check resistance values. Check
rotor for wear. If rotor or the stator
windings are defective, the complete
motor must be replaced.
9. Remove screws (12) and lift motor
housing (3) from seal plate (15).
10. Remove o-ring (2), replace if
damaged.
11. Remove motor bolts, lift motor
stator assembly from seal plate (15).
Figure 2
barmesapumps.com
Summary of Contents for 2BSE102SS
Page 12: ......