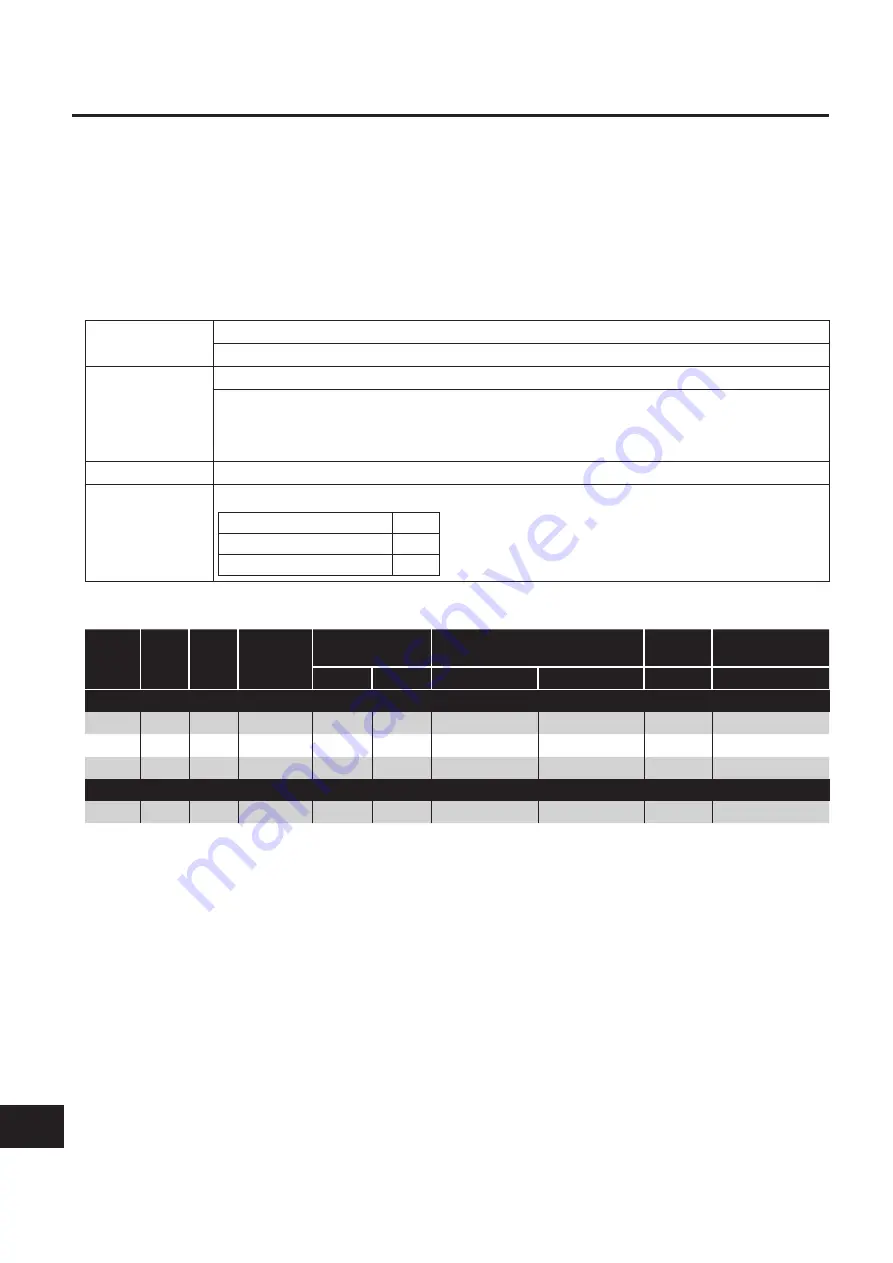
54
| E3 IP66 Outdoor Rated User Guide |
Version 1.25
www.bardac.com
10. Technical Data
10.1. Environmental
Operational ambient temperature range
:
-20 ... 40°C (frost and condensation free)
Storage ambient temperature range
:
-40 … 60°C
Maximum altitude
:
2000m. Derate above 1000m: 2.5% / 100m
Maximum humidity
:
95%, non-condensing
Environmental Conditions
:
IP66 E3 drive products are designed to operate in 3S3/3C3 environments in
accordance with IEC 60721-3-3.
10.2. Input Power Supply Requirements
Supply Voltage
200 – 240 RMS Volts for 230 Volt rated units, + /- 10% variation allowed.
380 – 480 Volts for 400 Volt rated units, + / - 10% variation allowed.
Imbalance
Maximum 3% voltage variation between phase – phase voltages allowed.
All E3 drive units have phase imbalance monitoring. A phase imbalance of > 3% will result in the drive tripping.
For input supplies which have supply imbalance greater than 3% (typically the Indian sub- continent & parts of Asia
Pacific including China) Bardac recommends the installation of input line reactors. Alternatively, the drives can be
operated as a single phase supply drive with 50% derating.
Frequency
50 – 60Hz + / - 5% Variation.
Maximum Supply
Short-Circuit Current
Capacity
The maximum permissible short circuit current at the E3 drive Power terminals as defined in IEC60439-1 is:
230V single phase input drives
5kA
230V three phase input drives
100kA
400V three phase input drives
100kA
10.3. Rating Tables
Frame
Size
kW
HP
Input
Current
Fuse / MCB
(Type B)
Maximum Cable Size
Output
Current
Recommended
Brake Resistance
Non UL
UL
mm
2
AWG
A
Ω
110 - 115 (+ / - 10%) V 1 Phase Input, 230V 3 Phase Output (Voltage Doubler)
1
0.37
0.5
7.8
10
10
8
8
2.3
-
1
0.75
1
15.8
25
20
8
8
4.3
-
2
1.1
1.5
21.9
32
30
8
8
5.8
100
200 - 240 (+ / - 10%) V 1 Phase Input, 3 Phase Output
1
0.37
0.5
3.7
10
6
8
8
2.3
-
Technical Data
10